Polycarbonate: The New Rotomolder’s Best Friend
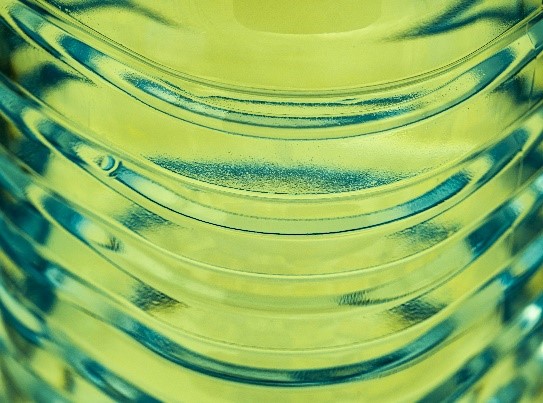
Polyethylene dominates rotomolding, making up nearly 95% of materials used—but alternatives have their place. Jake Kelly-Walley explains why PC is the new best friend of rotomolders.
It is no secret that the rotational molding (RM) industry has a strong relationship with polyethylene. Considering the complementary thermal characteristics and melting temperature, as well as the blend of stiffness, toughness, and ease of processing, it is an obvious choice. It is fair to say that polyethylene is a rotomoulder’s best friend. Although around 95% of the materials used are PE, there are many other materials to choose from.
You can also read: Precision and Efficiency: A New Era in Rotomolding Technology.
New Applications, New Requirements, New Materials
Despite the versatility of PE, some applications may be considered outside
its technical reach, yet they are ones where RM can add value. In particular, applications that require a high degree of transparency, such as street lamps, high-end products, or those where visibility of the contents is essential. Polyethylene, in all its forms —linear low-density (LLDPE), medium-density polyethylene (MDPE), and high-density polyethylene (HDPE)—is inherently semi-crystalline resulting in a hazy, translucent appearance. But are there alternative materials to think about? Absolutely.
Polycarbonate Chemistry
The industry is no stranger to overcoming transparency challenges through materials selection. Molders have, for several years, been manufacturing with polycarbonate (PC). The inherent properties of this material allow full transparency, giving a unique appearance unmatched by other materials.
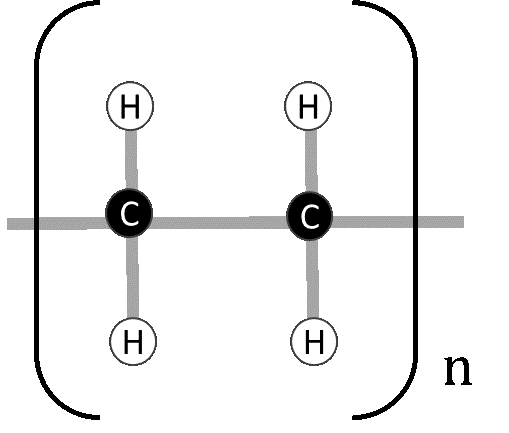
PE structure (PE).
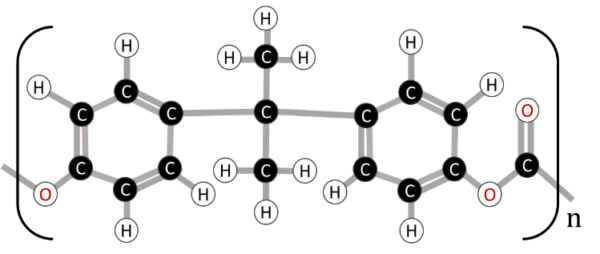
Polycarbonate structure (PC) repeat units.
By examining material chemistry, we can see the key differences between the well-known and widely used polyethylene repeat unit and that of polycarbonate. But what truly matters? Polyethylene’s simple molecular chains allow for easy crystallization, giving it a balance of toughness, stiffness, and a naturally translucent appearance. In contrast, polycarbonate’s more complex, “cluttered” structure—filled with carbonate groups—prevents crystallization. This highly amorphous nature results in exceptional transparency, creating a glass-like aesthetic.
It’s easy to see why moulders might select polycarbonate for its clarity. But what other properties set it apart? As expected, polycarbonate differs significantly from polyethylene. In comparison, it offers substantially greater stiffness and hardness, making it a strong alternative for specific applications. While polycarbonate has good toughness, it is not as ductile as polyethylene, particularly at the low temperatures of the I-ARM impact test. However, PC does offer some flame-retardant properties, including self-extinguishing behaviour when exposed to flames—an important factor for applications requiring compliance with internal lighting regulations.
That said, its use isn’t limited to indoor applications. I have worked with PC materials that demonstrate strong UV stability and perform well in outdoor environments. Some of these materials have been in service for years, maintaining excellent UV resistance.
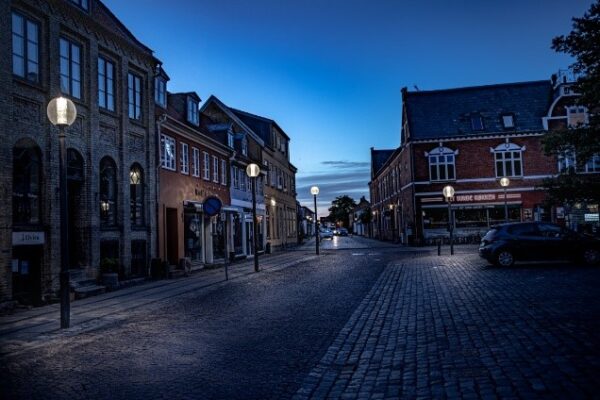
Images Courtsey of Dansk Rotations Plastic ApS.
Can You Feel The Pressure?
When molding polycarbonate—a less conventional choice for rotomoulders—precise process control is essential. Unlike polyethylene, PC is less forgiving and requires careful monitoring of internal air temperature (IAT). Pre-heating the mould can also be beneficial, helping to minimize thermal exposure and reduce cycle times.
Additionally, unlike PE, polycarbonate is hygroscopic, meaning it absorbs moisture. Proper handling and drying procedures are crucial to prevent defects and ensure optimal processing conditions.
While bubble removal is essential for optimal performance in any rotational molding material, it is especially critical for achieving polycarbonate’s glass-like clarity, as demonstrated in various examples. In some applications, complete transparency is the goal. However, I have seen incredible design work where bubbles were intentionally retained or only partially removed, resulting in uniquely striking aesthetics. This creative approach opens exciting possibilities, and it would be great to see further exploration in this area.
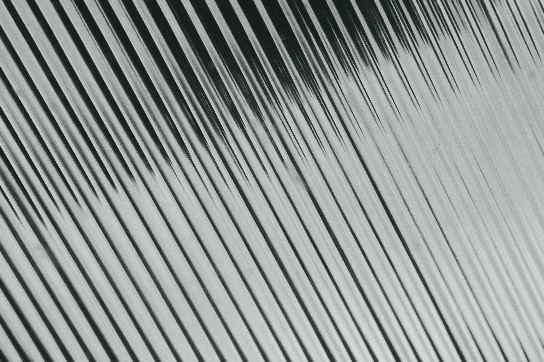
The Rise of Polycarbonate in Rotomoulding Applications. Courtesy of Polilab.
If achieving full clarity is the ultimate goal, applying slight positive pressure to the mould during the process can help eliminate voids. In both industrial molding trials and laboratory-scale experiments, I have observed firsthand how positive pressure encourages bubbles to dissolve into the material. This technique is applied once the polymer has formed a layer on the tooling.
As the industry shifts toward electrically conductive rotational molding with on-tool heating, the ability to precisely control temperature and pressure will expand opportunities for moulders to work with polycarbonate, further unlocking its potential.
Finally, when it comes to processing, polycarbonate exhibits minimal shrinkage due to its amorphous nature. This is an important factor to appreciate, especially in tool design and the demolding process. While it behaves differently from polyethylene, with the right approach, shrinkage can be easily managed.
The Future of Rotomolding Polycarbonate
I’ve seen many successful commercial applications of polycarbonate, and it’s exciting to witness such innovative products being created through rotational molding. I encourage all moulders looking to innovate to consider how they can leverage the unique properties of this material. As the rotational molding industry continues to diversify, the use of polycarbonate will expand. Despite its differences from polyethylene, this aesthetically engineered polymer has the potential to drive high-value applications.
Article by: Jake Kelly-Walley, R&D Engineer at Matrix Polymers and PhD Researcher at Queen’s University Belfast.
Edited by: MSc Juliana Montoya for online publication.