Elastomer Recycling: Three Paths to Sustainable Rubber
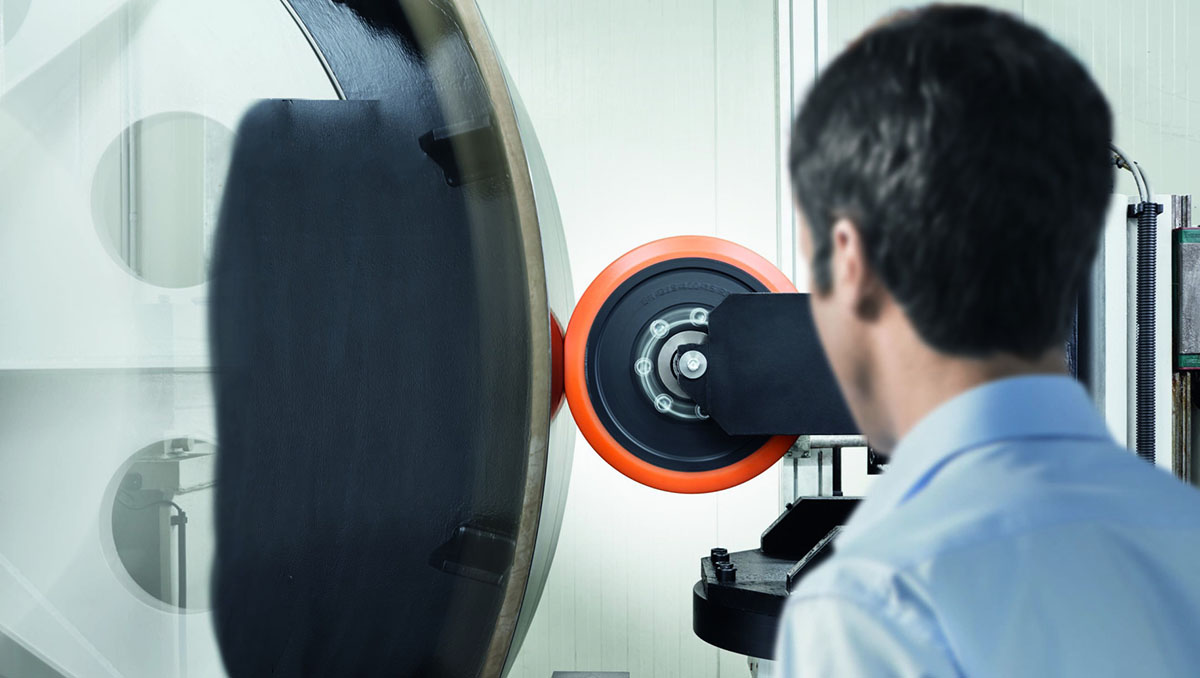
Elastomer recycling sector is undergoing significant transformation as new technologies emerge to address the limitations of traditional methods.
Let’s check about the current status that highlight three distinct approaches to rubber recycling, each with varying degrees of material preservation and environmental impact.
You can also read: Recycled Rubber – A Sustainable Alternative to Carbon Black in Tires
1. Mechanical Reclamation Delivers Cost-Effective Elastomer Recycling
The rubber industry widely uses mechanical reclamation for its affordability, but this elastomer recycling method shows clear limitations. The grinding process damages polymer chains, typically reducing tensile strength by 40-60%. These recycled rubber products mainly serve low-grade applications like playground surfaces or rubber mats, selling at just 30-50% of virgin material prices. The mechanical approach works for basic recycling needs but can’t restore high-performance properties.
2. Selective Devulcanization Advances Rubber Recovery
Emerging devulcanization technologies offer smarter rubber recycling by precisely targeting sulfur bonds while preserving polymer integrity. This elastomer treatment maintains 70-85% of original material characteristics, enabling reuse in more demanding applications. Recent studies confirm devulcanized rubber can achieve 90% of virgin material performance in specific uses, though manufacturers still struggle with batch consistency. This middle-ground solution bridges the gap between basic recycling and premium material recovery.
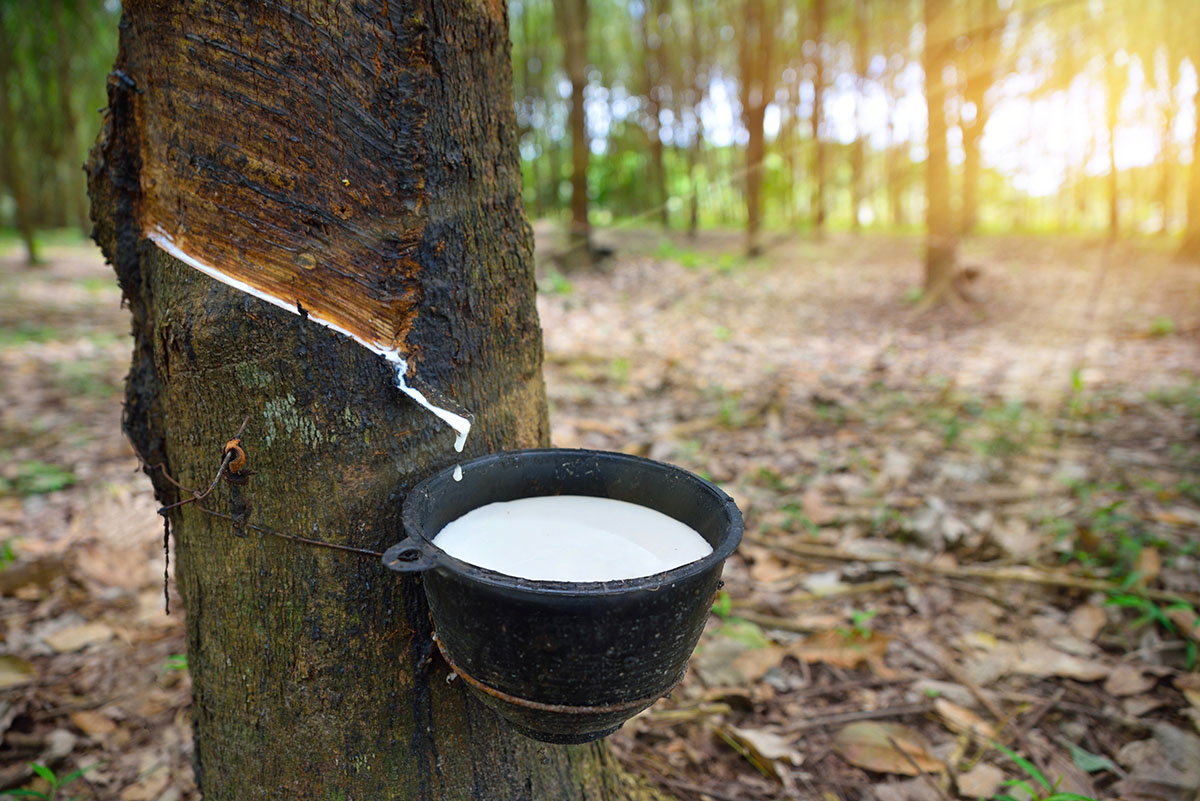
Recent progress in rubber regeneration confirms the technical feasibility of high-quality recycling. However, achieving scale requires standardized testing, better collection systems, supportive policies, and ongoing research investment.
3. Chemical Depolymerization Pioneers Circular Rubber
The most advanced elastomer recycling technique breaks rubber down to molecular components for true closed-loop regeneration. Current pilot projects in Covestro demonstrate this rubber-to-raw-material process can retain 85-95% of original properties, though requires significant energy input. Early data suggests this cutting-edge recycling method could slash lifecycle emissions by 50-65% compared to conventional production, potentially revolutionizing high-performance rubber applications.
Comparing Rubber Recycling Technologies
Feature | Mechanical | Devulcanization | Depolymerization |
---|---|---|---|
Property Retention | Moderate | Good | Excellent |
Energy Needs | Low | Medium | High |
Cost Efficiency | High | Moderate | Low |
End Uses | Basic | Diverse | Premium |
Overcoming Rubber Recycling Challenges
- The elastomer recycling sector must address several hurdles to achieve widespread adoption. High capital costs exceeding $50 million per facility deter many potential operators, while inconsistent feedstock quality plagues recycling efficiency. The market also hesitates to adopt recycled high-performance rubber, despite technological advances.
- The industry now explores hybrid elastomer solutions combining different recycling approaches. Some operators already blend mechanical recycling for bulk applications with chemical methods for specialty rubbers. This balanced strategy may deliver both environmental benefits and economic viability for sustainable rubber production.
- Recent progress in rubber regeneration confirms the technical feasibility of high-quality recycling. However, achieving scale requires standardized testing, better collection systems, supportive policies, and ongoing research investment. As material scientists, manufacturers, and policymakers collaborate, advanced elastomer recycling methods promise to transform rubber sustainability without compromising performance.
To read more: Covestro to invest in Pilot Plant for Recycling of Elastomer