4 Companies Advancing Sustainability with Recycled Content
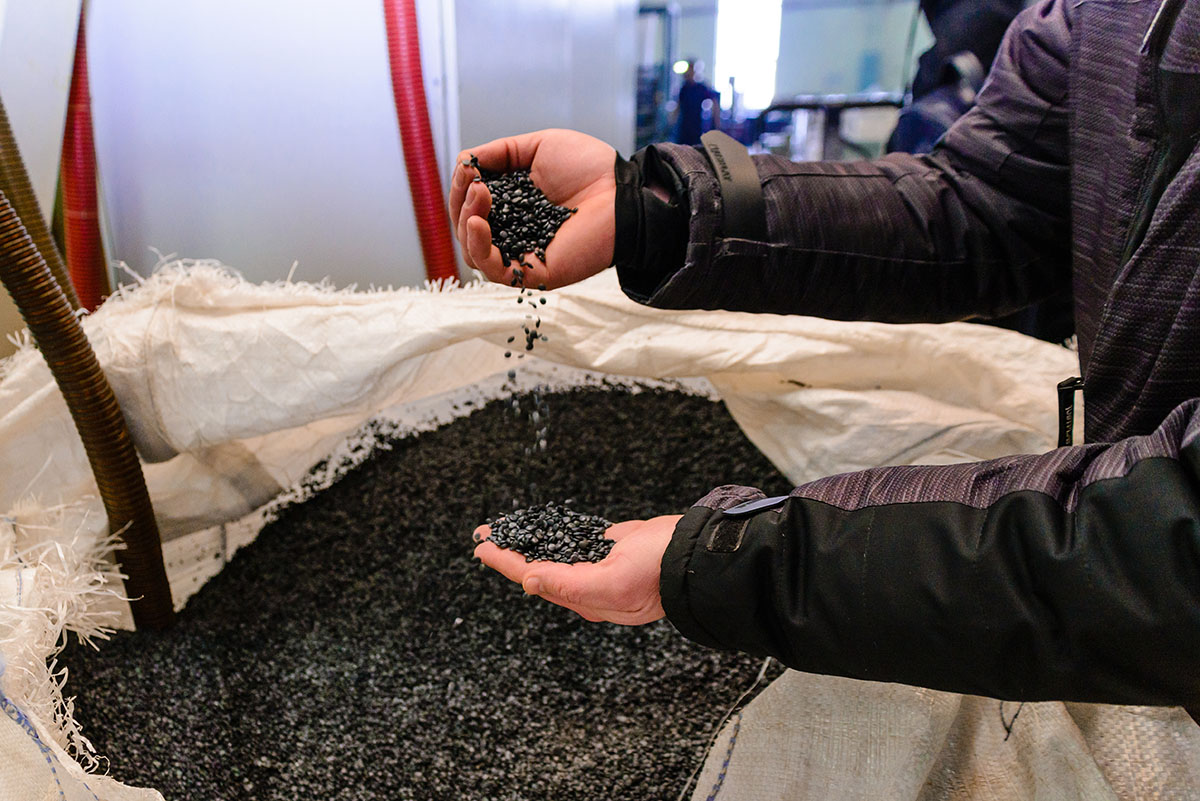
Companies worldwide are reevaluating their production processes. One major shift is the use of recycled content in manufacturing.
Industries are increasingly utilizing recycled plastics, metals, and paper, thereby reducing their reliance on virgin resources that consume more energy and raw materials.
Read also: Post-Consumer Recycled Market: Forecasts to 2029.
This shift supports a circular economy, where materials are reused rather than discarded. Leading companies demonstrate that sustainability can uphold quality and performance. Their innovations highlight how recycled content enhances both efficiency and environmental responsibility.
Here are some of the leading companies using recycled content to drive sustainability:
1. Faerch: Pioneering Circular Food Packaging
Faerch is leading the way in sustainable food packaging. The company has introduced CPET trays for chilled ready meals containing 40% recycled PET (rPET). This initiative promotes a circular economy, where materials are reused rather than discarded.
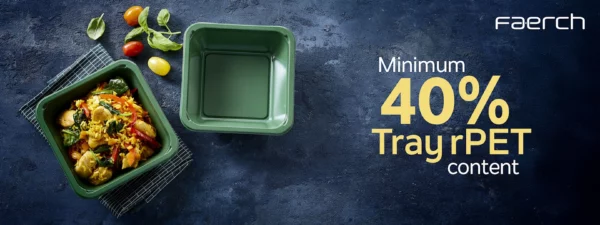
Faerch introduces chilled ready meal trays containing at least 40% Tray rPET. Courtesy of Faerch.
Using Recycled Plastic in Food Packaging
Faerch has a long history of using recycled materials. In 2019, it launched Evolve by Faerch, a packaging solution with up to 70% post-consumer recycled content. Building on this success, Faerch is now taking another step forward.
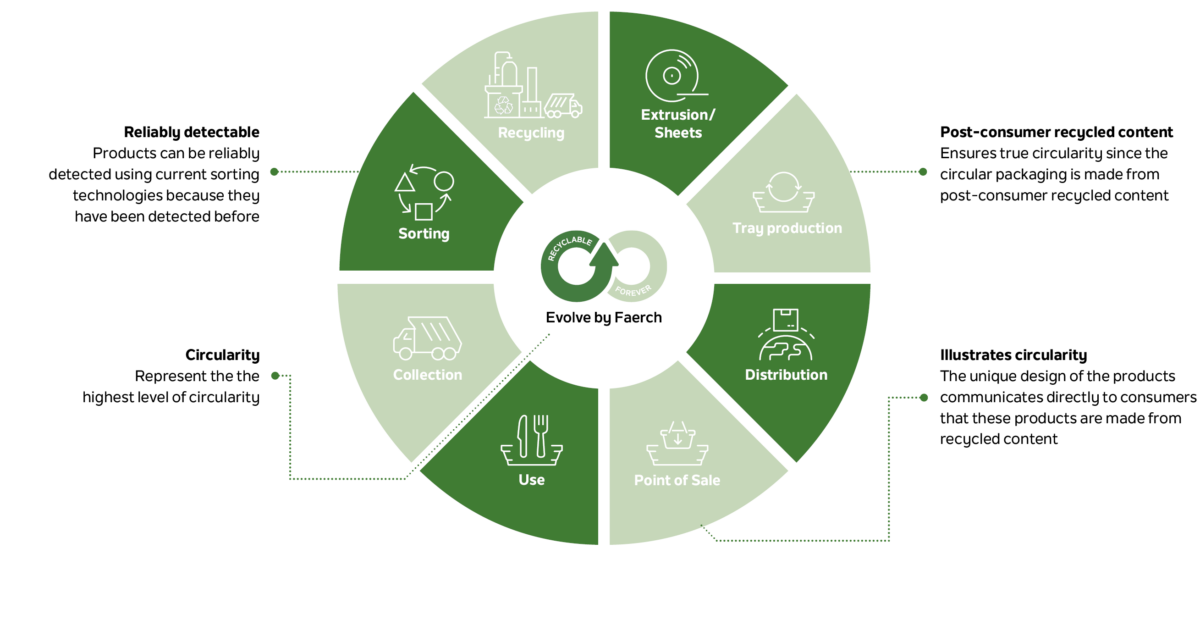
Evolve by Faerch. Courtesy of Faerch.
Starting in January 2025, all CPET trays for chilled ready meals will contain at least 40% Tray rPET. This ensures that a significant portion of each tray comes from previously used plastics. Despite using recycled materials, the trays will maintain the same strength, durability, and food safety standards as virgin plastic.
How Faerch’s Recycling Process Works
The recycled PET in these trays comes from kerbside-collected waste. Used plastic trays are collected, processed, cleaned, and then recycled to create new ones. This process reduces the demand for virgin fossil-based plastics and prevents waste from being sent to landfills or incinerators. By keeping plastic in circulation, Faerch helps to lower pollution and promote responsible recycling practices.
Environmental Benefits of Tray rPET
Faerch’s commitment to sustainability is backed by scientific research. A recent carbon footprint study showed that Tray rPET reduces carbon emissions by 57% compared to virgin PET. It also has a 35% lower footprint than recycled PET from plastic bottles. These findings underscore the environmental advantages of utilizing recycled plastic in food packaging. By choosing Faerch’s trays, food brands can reduce their carbon footprint and support a more sustainable packaging industry.
Industry Impact and Future Goals
Faerch is setting new industry standards by ensuring third-party certification for its recycled content. This provides transparency and helps food brands meet their sustainability commitments. Consumers and regulators are demanding higher recycled content in packaging, and Faerch’s initiative helps businesses meet these expectations.
Lars Gade Hansen, CEO of Faerch, emphasizes the importance of this initiative. He believes food packaging should be part of a closed-loop system. He states that just as bottles should be recycled into new bottles, trays should also be recycled into new trays. This approach prevents valuable materials from being lost and ensures plastic remains in use.
Faerch plans to further increase the recycled content in its products, building on its current 40% Tray rPET content. This commitment drives the development of more sustainable packaging solutions, moving the industry closer to fully circular food packaging.
2. Leadec and Jayplas: Creating a Closed-Loop Recycling System
Leadec and Jayplas have developed a fully closed-loop recycling process for plastic waste. This collaboration demonstrates how companies can turn waste into valuable resources. By recycling low-density polyethylene (LDPE) film waste, they have created plastic sacks with 100% recycled content.
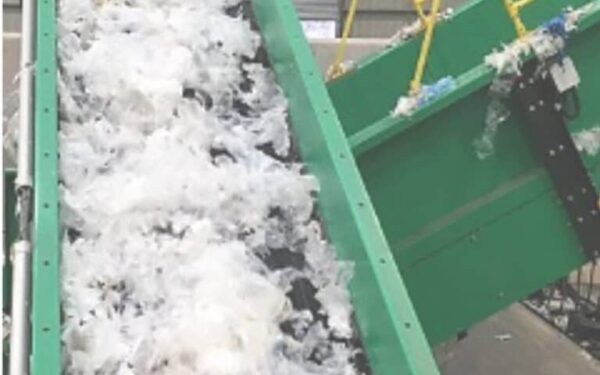
Low-density polyethylene (LDPE) film waste. Courtesy of Jayplas.
Transforming Plastic Waste into New Products
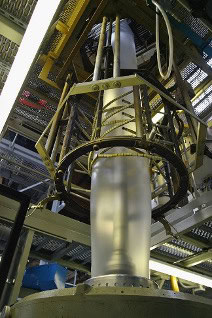
From the used bag to the new, clear film. Courtesy of Leadec.
Leadec generates large amounts of plastic waste in its operations. Instead of disposing of it, the company partnered with Jayplas to recycle it. The process starts with collecting waste LDPE film at Leadec’s Halewood site. The team carefully sorts the plastic, ensuring only the right type of film enters the recycling process.
Jayplas sorts the plastic and sends it to their advanced recycling facility, where they further separate it using Optical Near-Infrared (NIR) technology. This process ensures that only the correct polymers move forward. Jayplas then washes, melts, and processes the sorted plastic into recycled pellets. Later, they use these pellets to manufacture new plastic sacks at their packaging facility.
The Benefits of a Closed-Loop System
This recycling process keeps plastic waste within the UK, reducing the need for virgin plastic. Each year, Leadec’s Halewood site uses around 250,000 plastic sacks. By switching to 100% recycled sacks, the company prevents 32.5 tonnes of plastic waste from entering landfills or incinerators. This approach also lowers carbon emissions by reducing the demand for new plastic production.
A key benefit of this system is its efficiency. The same plastic waste collected from Leadec is transformed into new products for its operations. This creates a circular process where waste is continuously reused. It also ensures a steady supply of high-quality recycled plastic for manufacturing.
Read Also: Post-Industrial Recycled Content Means Better Plastic.
Industry Collaboration for a Sustainable Future
This project shows the power of collaboration in building sustainable solutions. Leadec and Jayplas worked closely to develop a process that meets industry standards. They aligned on material specifications, tested collection methods, and ensured the final product met quality requirements. Their success demonstrates that companies can reduce waste without compromising product performance.
Jayplas has been a leader in plastic recycling for decades. It operates several recycling facilities across the UK, handling different polymer types. By partnering with Leadec, the company is helping businesses achieve their sustainability goals. Leadec, a global specialist in industrial services, is also taking a strong stance on sustainability. Its Green Factory Solutions initiative supports industries in reducing waste and moving toward zero-emission operations.
A Model for Circular Economy in Manufacturing
This project serves as a model for other industries looking to reduce plastic waste. By integrating recycling into their operations, companies can reduce waste and lower their environmental impact. The success of Leadec and Jayplas proves that a circular economy is possible in manufacturing.
Going forward, more companies can adopt similar approaches. Businesses that rely on plastic packaging can collaborate with recyclers to create sustainable solutions. This shift will not only benefit the environment but also meet the growing demands of regulators and consumers for responsible waste management.
Read Also: Sustainable Tech: Durable Products from Recycled Materials
3. AkzoNobel: Advancing Sustainable Packaging in the Paint Industry
AkzoNobel is making significant progress in sustainable packaging. The company aims to use at least 50% recycled content in its plastic packaging for decorative paints in Europe by 2025.
Increasing Recycled Content in Packaging
Most plastic packaging used in the paint industry is made from virgin materials. AkzoNobel is working to change this by introducing more recycled content. The company collaborates with packaging suppliers to develop solutions that meet performance standards while using sustainable materials.
Through continuous research, AkzoNobel has successfully created key packaging products with up to 70% recycled plastic. Moreover, this achievement proves that high levels of recycled content can be used without compromising durability. By maintaining the same weight and strength, these packaging solutions offer a practical alternative to conventional plastic.
Overcoming Challenges in Sustainable Packaging
One major challenge in using recycled plastic is ensuring product safety and consistency. Paint packaging must be strong, airtight, and resistant to leaks. AkzoNobel has addressed these challenges through innovation and material testing. The company ensures that recycled plastic performs as well as virgin materials in protecting paint products.
Another challenge is securing a steady supply of high-quality recycled plastic. AkzoNobel works closely with suppliers to maintain a reliable source of sustainable materials. This partnership helps the company scale its efforts and expand the use of recycled content across its product range.
Contribution to Circular Economy and Environmental Goals
By increasing recycled content, AkzoNobel reduces its reliance on virgin plastic. This shift helps lower carbon emissions and supports a circular economy. Instead of plastic waste ending up in landfills, it is transformed into new packaging, extending its life cycle.
Using recycled plastic also aligns with global sustainability goals. Many governments are introducing stricter regulations on plastic waste. AkzoNobel’s initiative prepares the company for future environmental policies while meeting consumer expectations for eco-friendly products.
You can also read: 3D Printing with Recycled Materials.
4. Dawn Powerwash™ Dish Spray: Promoting Reusability and Recyclability
Dawn Powerwash™ Dish Spray is an innovative cleaning product that focuses on sustainability. It offers a convenient dishwashing solution while reducing plastic waste. The product’s design encourages consumers to reuse packaging and minimize environmental impact. In addition, Dawn dishwashing liquid now contains 35% PCR (post-consumer recycled) content in clear bottles, reinforcing the brand’s commitment to sustainability.
By integrating recycled materials, Dawn reduces reliance on virgin plastic and supports circular economy goals. As more companies adopt similar strategies, plastic waste is expected to decrease, ultimately leading to a cleaner and more sustainable future.
Recognition for Sustainable Design
Dawn Powerwash™ Dish Spray has gained industry recognition for its eco-friendly packaging. It won the “Award of Distinction” in the Sustainable Package Design category at the 2025 PAC Global Awards. This award highlights its success in combining functionality with environmental responsibility.
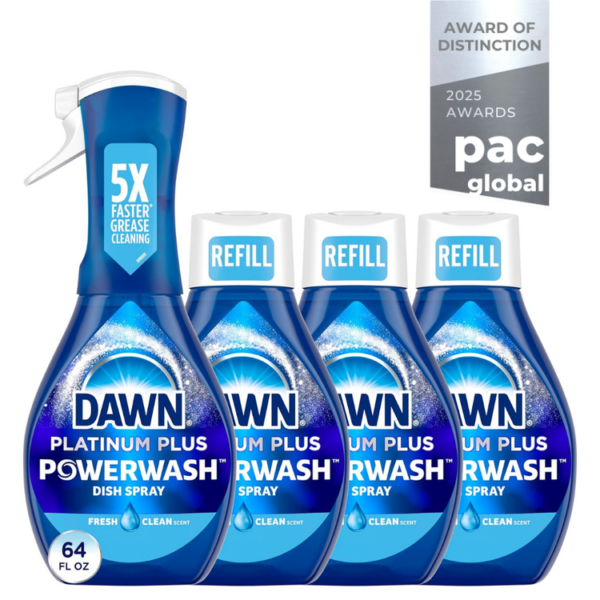
Dawn Powerwash earned the “Award of Distinction” in the Sustainable Package Design category at the 2025 PAC Global Awards. Courtesy of PAC Global Awards.
The recognition reinforces the importance of sustainable packaging in consumer goods. It also encourages other manufacturers to explore ways to reduce plastic waste.
Addressing Challenges and Scaling the Use of Recycled Materials
Integrating recycled content into products is essential for sustainability. Companies like Faerch, Leadec, Jayplas, AkzoNobel, and Procter & Gamble demonstrate this commitment. However, challenges persist, such as ensuring a consistent supply of high-quality recycled materials and adapting manufacturing processes. For instance, in 2023, only 8% of flexible plastic packaging was collected for recycling in the UK.
Read also: Anticipating Challenges as Demand for Recycled PET Increases
To address these issues, businesses can invest in advanced recycling technologies and foster industry collaborations. Nestlé’s £7 million investment in Impact Recycling’s facility to process hard-to-recycle plastics exemplifies such initiatives. By learning from these pioneering companies, others can effectively integrate recycled content, driving the transition toward a more sustainable and circular economy.