Scaling Profitability with Polymer-Based Chillers
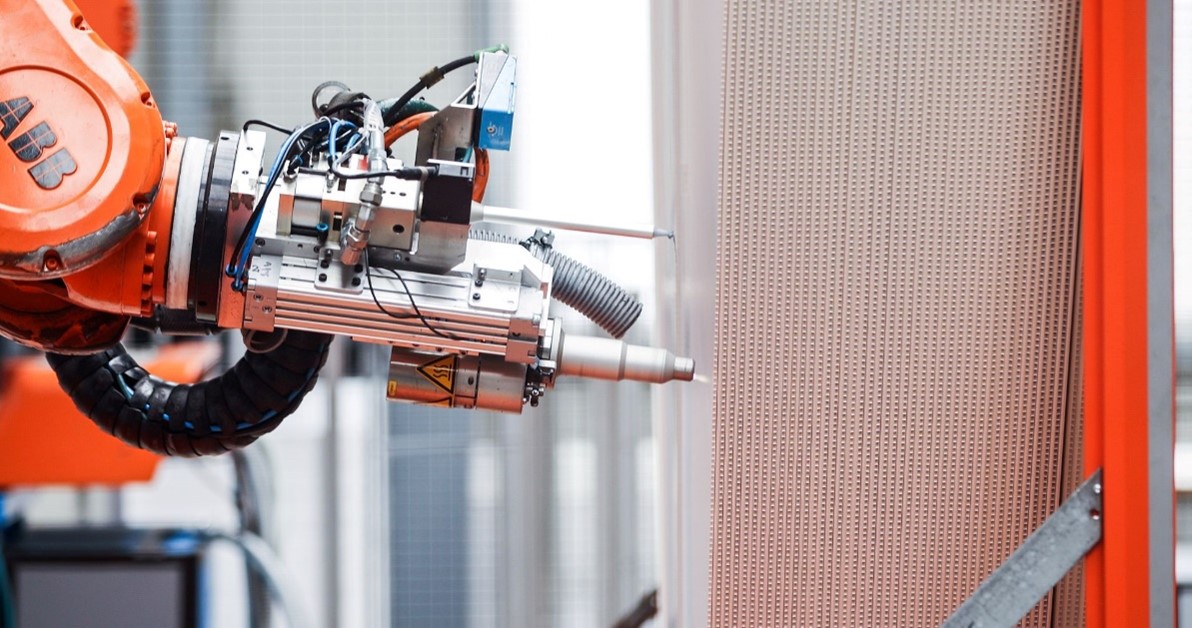
The market for polymer-based chiller components is expanding rapidly as industries seek cost efficiency, corrosion resistance, and energy savings.
Traditionally, metals like copper and aluminum have dominated heat exchangers and structural components, but high thermal conductivity polymer composites (HTCPCs) are now emerging as a viable alternative. These materials offer enhanced durability, reduced weight, and lower manufacturing costs, making them ideal for next-generation chillers.
You can also read: Thermally Conductive Plastic for Cooling Electronics.
Advancements in Polymer Heat Exchangers
Recent studies, including research from the Department of Mechanical Science and Engineering at the University of Illinois, highlight how polymer heat exchangers are revolutionizing the industry. Innovations in microchannel heat exchangers enhance heat transfer efficiency while reducing scaling and fouling issues. These improvements support the global shift toward energy-efficient HVAC systems, making polymer materials a strategic choice for sustainable cooling solutions.
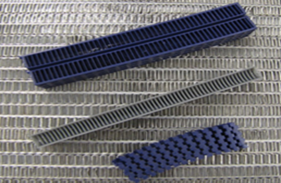
Nonmetallic heat exchangers. Image courtesy of United Technologies Research Center.
The Cost Advantage of Polymer-Based Chillers
One of the primary drivers of polymer adoption in chillers is the substantial cost savings they offer compared to traditional metal-based designs. According to the U.S. Department of Energy (DOE) Advanced Manufacturing Office, using injection molding for polymer-based heat exchangers can cut production costs by up to 50%. This process reduces the need for expensive corrosion-resistant coatings, minimizes raw material consumption, and simplifies assembly.
Additionally, fabrication time for polymer composite components is up to 90% shorter than that of traditional brazed-plate metal heat exchangers. This efficiency allows manufacturers to scale production faster while lowering operational and labor costs.
Cost Comparison: Metal vs. Polymer Heat Exchangers
A study led by United Technologies Research Center found that traditional brazed-plate metal heat exchangers cost approximately $600 per unit when manufactured in the U.S. In contrast, polypropylene-based heat exchangers, produced via injection molding, cost between $100 and $150 per unit, demonstrating a significant reduction in unit price.
With these cost advantages, polymer-based chillers offer an economically viable and scalable alternative to traditional metal-based cooling systems, particularly in price-sensitive markets that prioritize efficiency and sustainability.
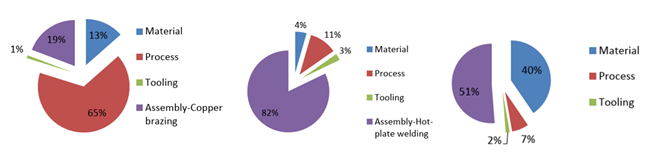
Cost breakdown for SS304 (left), Polypropylene (center) and composite (right), brazed plate heat exchanger manufactured in the US. Courtesy of High Thermal Conductivity Polymer Composites for Low-Cost Heat Exchangers.
Future Outlook for Polymer-Based Chillers
Despite their advantages, polymer-based heat exchangers face thermal conductivity limitations compared to metals. Copper and aluminum have superior heat transfer rates, requiring polymer solutions to use thinner walls or composite materials to enhance conductivity. Researchers are actively exploring nanocomposites and hybrid materials that integrate thermally conductive fillers to improve heat exchange efficiency while maintaining cost-effectiveness and corrosion resistance.
Durability is another concern, as polymers can fatigue, leak, or degrade over time, particularly in high-temperature and high-pressure applications. While advanced materials like Polyetheretherketone (PEEK) and Polyphenylene Sulfide (PPS) improve durability, they come at a higher cost. To address this, Researchers are developing polymer matrix composites (PMCs) to enhance mechanical strength without sacrificing weight and corrosion resistance.
The HVAC and industrial cooling sectors remain highly regulated, favoring traditional metallic heat exchangers. For polymer-based solutions to gain wider adoption, manufacturers must meet rigorous performance standards, obtain regulatory approvals, and demonstrate long-term reliability. This transition requires investment in material validation, industry partnerships, and compliance with evolving standards.
Looking ahead, several innovations could accelerate the adoption of polymer-based chillers. Nanocomposite materials with thermally conductive fillers can bridge the conductivity gap, while hybrid polymer-metal designs enhance efficiency and durability. Moreover, as global demand for sustainable, energy-efficient cooling solutions grows, government incentives and regulatory changes will accelerate polymer chiller adoption. Additionally, low-carbon, corrosion-resistant polymer chillers will gain traction in industrial and commercial sectors due to these supportive policies.