MacroCycle’s Molecular Approach to PET and Polyester Recycling
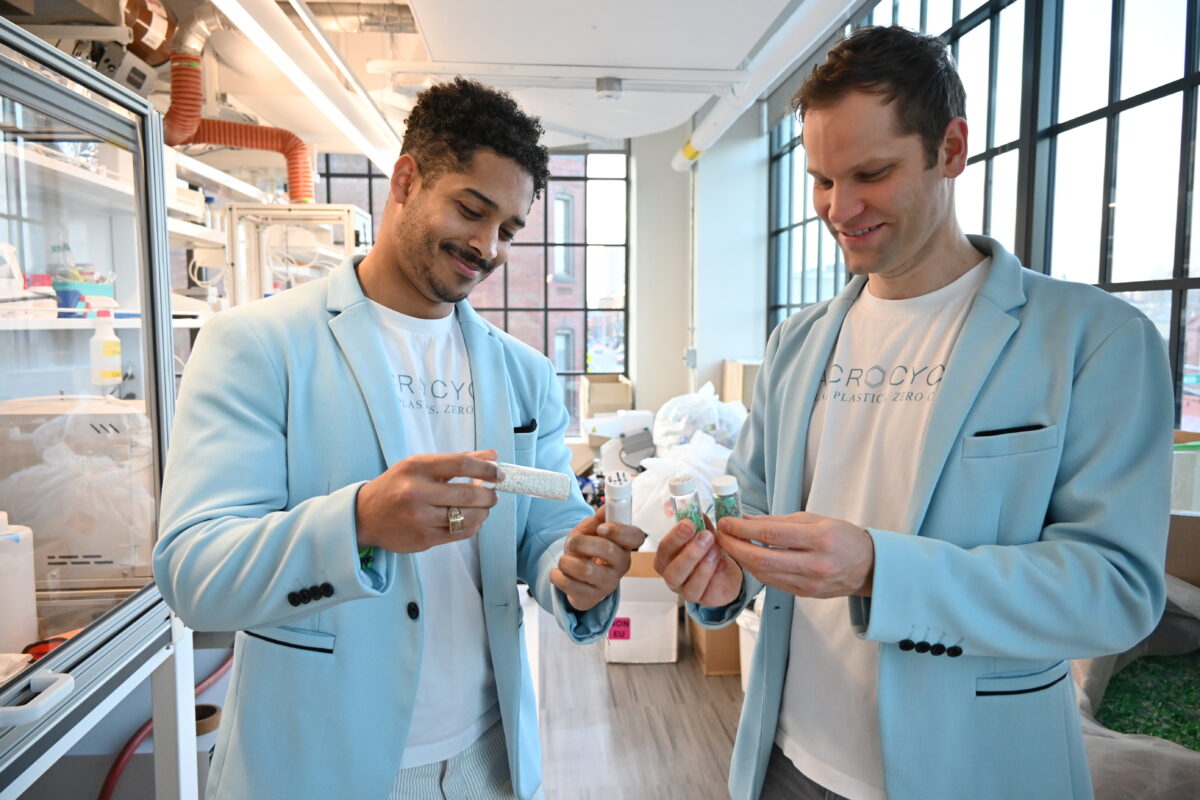
MacroCycle Technologies is redefining PET recycling through a scalable, energy-efficient molecular upcycling process.
The plastics industry faces increasing pressure to adopt sustainable solutions, yet conventional recycling methods struggle to meet the growing demand for high-quality recycled materials. MacroCycle Technologies, founded by Stwart Peña (CEO) and Jan-Georg Rosenboom (CTO), proposes PET and polyester recycling with a molecular upcycling approach that is more energy-efficient, cost-effective, and scalable than traditional chemical and mechanical recycling methods.
You can also read: Rethinking the System: We Need Molecular Recycling.
In an exclusive interview with Plastics Engineering, Peña and Rosenboom shared insights into their groundbreaking process, its industry impact, and their vision for the future of plastic recycling.
A New Approach to PET Recycling
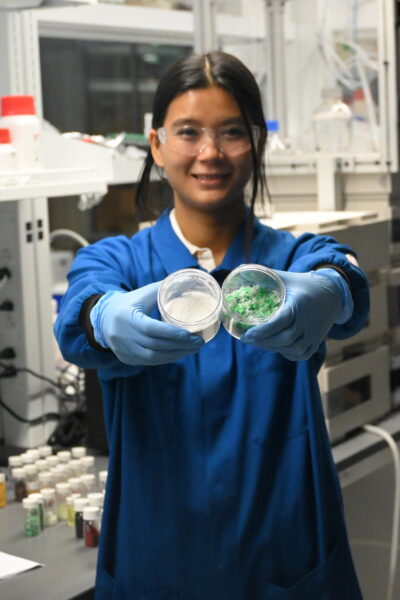
MacroCycle employs an alternative method based on the synthesis of cyclic macromolecules (macrocycles), enabling the effective recycling of PET or other polyesters. Courtesy of MacrocCycle Technologies
Unlike conventional depolymerization, which breaks down plastics into monomers, MacroCycle employs an alternative method based on the synthesis of cyclic macromolecules, or macrocycles, enabling the effective recycling of PET and other polyesters.
Their process takes the broken polymer chains in PET waste and converts them into macrocyclic intermediates for re-polymerization into high-quality PET through Ring-Opening Polymerization. Because this method avoids petrochemical monomers, it supports true circularity while reducing reliance on fossil-based raw materials in the production cycle.
Additionally, their dissolution-based purification method enhances the molecular weight and purity of materials, eliminating the need for toxic solvents commonly used in other processes. As a result, MacroCycle’s approach consumes 80% less energy than traditional plastic production, allowing for the full electrification of the entire process.
This electrification enables zero-carbon emissions at the production stage, further aligning with global efforts to decarbonize plastic manufacturing systems.
“I did my research on macrocyclic chemistry Ring-Opening Polymerization while working on bioplastics derived from renewable biomass sources.
In that process, I learned how to convert biomass into macrocyclic intermediates, then polymerize them into high-value plastic materials.
Later, I discovered that this approach not only works for biomass-based monomers but also applies to plastic waste.
That’s because macrocyclic trans-esterification chemistry can be used with any polyester-based material already circulating in the waste stream.
As a result, the method provides a powerful and flexible tool for both renewable feedstocks and post-consumer polyester recycling.” Said Jan-Georg Rosenboom, (CTO) of Macrocycle Technologies.
What Sets MacroCycle Apart?
MacroCycle Technologies offers an alternative to both mechanical and chemical recycling, filling gaps where current solutions fall short. Their key differentiators include:
- High-purity recycled PET without the degradation seen in mechanical recycling.
- Energy efficiency, with an 80% reduction in energy use compared to virgin plastic production.
- A fully electrifiable process, allowing for a carbon-neutral footprint.
- No toxic solvents, unlike many chemical recycling methods.
Additionally, their process eliminates the need for petrochemical-derived monomers, making it a genuinely circular and sustainable solution for recycling PET and polyester.
Scalability and Market Integration
MacroCycle Technologies collaborates with waste collectors and suppliers to transform plastic waste into resin pellets. Their primary customers include brands, packaging manufacturers, and textile mills, all of whom require high-quality recycled PET or polyester for their products.
One of the biggest challenges in PET recycling is the limited supply of high-quality recyclates, particularly from textiles. Most recycled polyester (rPET) comes from bottles, not textile waste, creating a major gap in textile-to-textile recycling. MacroCycle’s technology directly addresses this issue by enabling closed-loop polyester recycling, an innovation that could dramatically reduce waste in the fashion and textile industries.
Additionally, their cost-competitive approach ensures that companies can adopt this technology without relying on green premiums, making circular plastic solutions more accessible to a wider market.
Challenges in Plastic Recycling
Despite its benefits, plastic recycling still faces multiple challenges, including:
- High costs and limited supply of quality recyclates.
- Misinformation about chemical recycling, as many ineffective or environmentally harmful methods have given the field a bad reputation.
- Lack of policy support and public awareness, leading to slow adoption of innovative recycling solutions.
MacroCycle Technologies believes that education is key to overcoming these barriers. By engaging with industry leaders, policymakers, and consumers, they aim to foster a deeper understanding of molecular recycling and its potential to transform plastic sustainability.
“Cost is one of the main challenges our customers are currently facing. Everyone wants to use more recycled plastic, but the reality is that there isn’t enough available on the market. When it is available, the price is often too high, or the quality is too low. At MacroCycle, we’re offering a technology that solves both of these issues. Our process is waste-resilient, delivering high-quality PET with significantly lower energy demands—and, as a result, much lower costs than other available technologies”. Said Stwart Peña, CEO of Macrocycle Technologies.
Public Education Around Recycling
Beyond its technological innovation, MacroCycle Technologies places strong emphasis on public education around recycling.
As widely recognized within the industry, one of the greatest barriers to scaling effective recycling systems is the limited access to high-quality material supply. Improving collection efforts and enhancing the quality of recycled inputs requires greater public awareness and participation. Moreover, a core part of MacroCycle’s mission is to promote education about recycling. Teaching people how to properly sort and dispose of plastic waste is essential to realizing a truly circular economy.
This educational outreach must extend across all levels of society—particularly to policymakers and government leaders, who are uniquely positioned to establish the infrastructure and policies that can drive meaningful, large-scale change.
A Vision for the Future
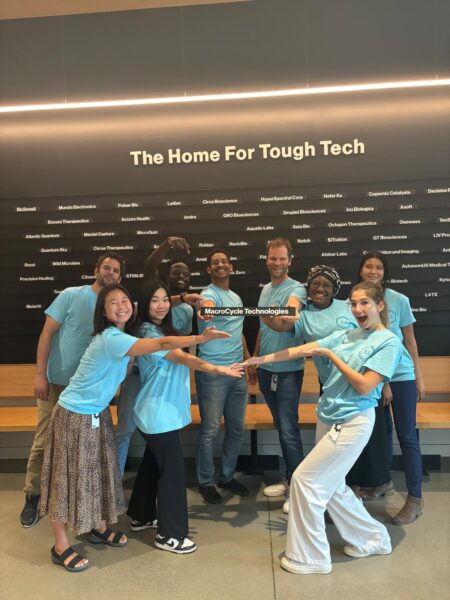
MacroCycle Technologies Team. Courtesy of MacroCycle Technologies.
MacroCycle Technologies aims to become the largest PET and polyester producer by scaling a zero-carbon upcycling process for global adoption. In addition, they plan to license their technology worldwide once it has been scaled up, creating a flexible solution adaptable across industries and geographic regions. Rather than replacing mechanical recycling, they position their method as complementary, targeting waste streams traditional systems are unable to process.
By collaborating with existing recyclers, they work to close the loop on end-of-life PET and polyester waste and reduce fossil-fuel dependency in plastics. Their vision combines innovation and partnership to advance a circular economy and reshape the future of sustainable plastic production. The company is proving that innovative molecular upcycling can transform the future of PET and polyester recycling.