Building a Resilient Supply Chain in Packaging
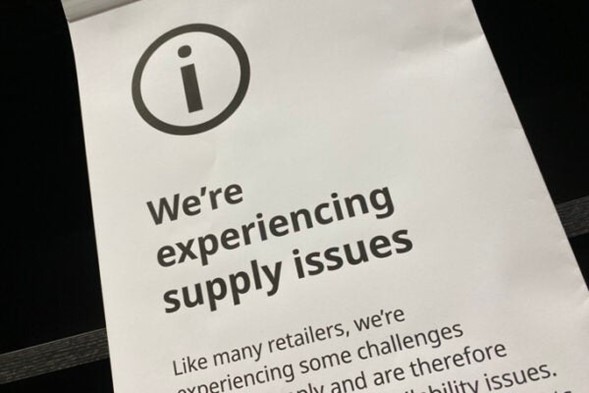
Frequent out-of-stock (OOS) situations disrupt operations, leading to revenue losses, production delays, and customer dissatisfaction.
The polymer packaging industry is critical in global supply chains, serving food and beverage, pharmaceuticals, and consumer goods sectors. Managing OOS risk requires strategic planning, demand forecasting, supply chain optimization, and resilience-building measures to ensure the uninterrupted availability of essential packaging materials.
You can also read: Vietnam – U.S. Plastics Trade: A Strategic Shift in Global Supply Chains.
Understanding OOS Risks in Packaging
Supply chain disruptions are a leading cause of OOS situations in polymer packaging, driven by geopolitical conflicts, natural disasters, and logistics bottlenecks. The Russia-Ukraine war has led to petrochemical shortages, while the 2021 Texas winter storm severely impacted U.S. polyethylene and polypropylene production.
Port congestion and the 2021 global container shortage worsened delays, leaving manufacturers scrambling for alternatives. Rising energy prices further strain supply chains, making polymer resin production more expensive and unpredictable. Production constraints, including equipment failures, labor shortages, and regulatory challenges, also contribute to supply instability.
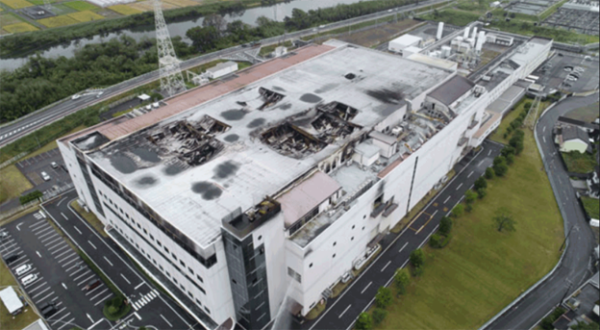
Aerial view of the AKM Factory incident in 2020.Courtesy of Strata.
A fire at a Japanese AKM Factory in 2020 disrupted global deliveries, while pandemic-related workforce shortages hindered Tetra Pak’s ability to meet food packaging demands. Additionally, strict environmental regulations, such as the EU’s plastic tax, have forced companies to adjust production processes, slowing output. The COVID-19 pandemic fueled an e-commerce boom, drastically increasing the need for flexible packaging, leaving major suppliers unable to keep up.
Building a Stable Supply Chain to Prevent OOS
Companies can mitigate OOS risks by improving demand forecasting, diversifying suppliers, and optimizing inventory management. Nestlé utilizes AI-driven analytics for demand planning, while Walmart employs real-time inventory tracking to maintain stock stability. Predictive modeling helps businesses anticipate fluctuations and respond proactively.
Supplier diversification, as seen with PepsiCo’s multi-region sourcing and Unilever’s long-term supplier contracts, ensures continuous supply. Maintaining buffer stock further protects against disruptions.
Enhancing Supply Chain Resilience
Regional sourcing, such as Procter & Gamble’s localized resin procurement, reduces reliance on distant suppliers, while Coca-Cola’s digital twin technology enables real-time supply chain monitoring for proactive risk management. Amazon’s smart warehousing and just-in-time (JIT) systems help maintain optimal inventory levels. Sustainable alternatives, like bio-based plastics, add long-term supply security, ensuring companies stay adaptable in a shifting market.
The Future of OOS Prevention in Polymer Packaging

AI Driven Forecast models in operations. Courtesy of McKinsey & Company.
AI-driven forecasting, real-time supply chain monitoring, and regionalized sourcing will become industry standards, ensuring greater operational resilience. The demand for sustainable packaging will accelerate the shift toward alternative materials and circular economic practices. Companies that implement these strategies will not only strengthen their supply chains but also gain a competitive advantage in an increasingly volatile market. Looking ahead, collaboration among manufacturers, suppliers, and policymakers will be crucial in building a more adaptive and efficient packaging ecosystem.