What’s Powering the Future of Blow Molding?
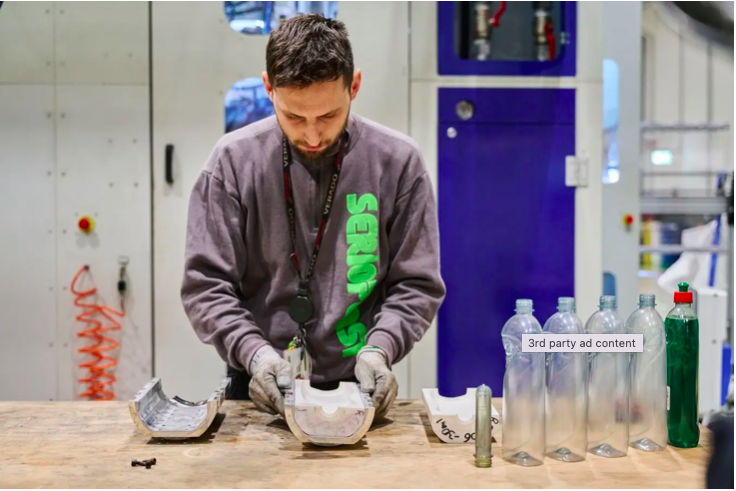
Automation, sustainability, and 3D printing shape the blow molding’s future.
Blow molding (BM) produces lightweight, hollow products with precision and speed. Its unmatched efficiency and versatility drove the global blow-molded plastics market to $80.04 billion in 2023. With a projected compound annual growth rate (CAGR) of 7% from 2024 to 2030, the industry will embrace emerging trends redefining quality, sustainability, and design standards.
You can also read: Trends in Film Packaging – Shaping the Future.
Automation and AI Integration
Automation and AI are transforming multiple industries, including BM. These technologies enable machines to operate with greater precision and speed, reducing downtime and cutting operational costs. Moreover, they boost productivity and ensure consistent quality by allowing real-time adjustments and optimization. Companies like FyagoUnion lead the way by developing BM machines equipped with sensors and AI-driven controls. These innovations streamline operations and reduce human error.
Sustainability Shaping The Process
Sustainability is a central topic of this era and a vital trend shaping Blow Molding’s future. Companies are integrating biodegradable and recyclable materials into the manufacturing process. They are also adopting energy-efficient machines and technologies that minimize waste. Meccanoplastica Group exemplifies this commitment with its extrusion and stretch blow molding machines. These machines achieve some of the lowest energy consumption levels in the industry and earn an energy efficiency rating of 10+ according to the Euromap classification.
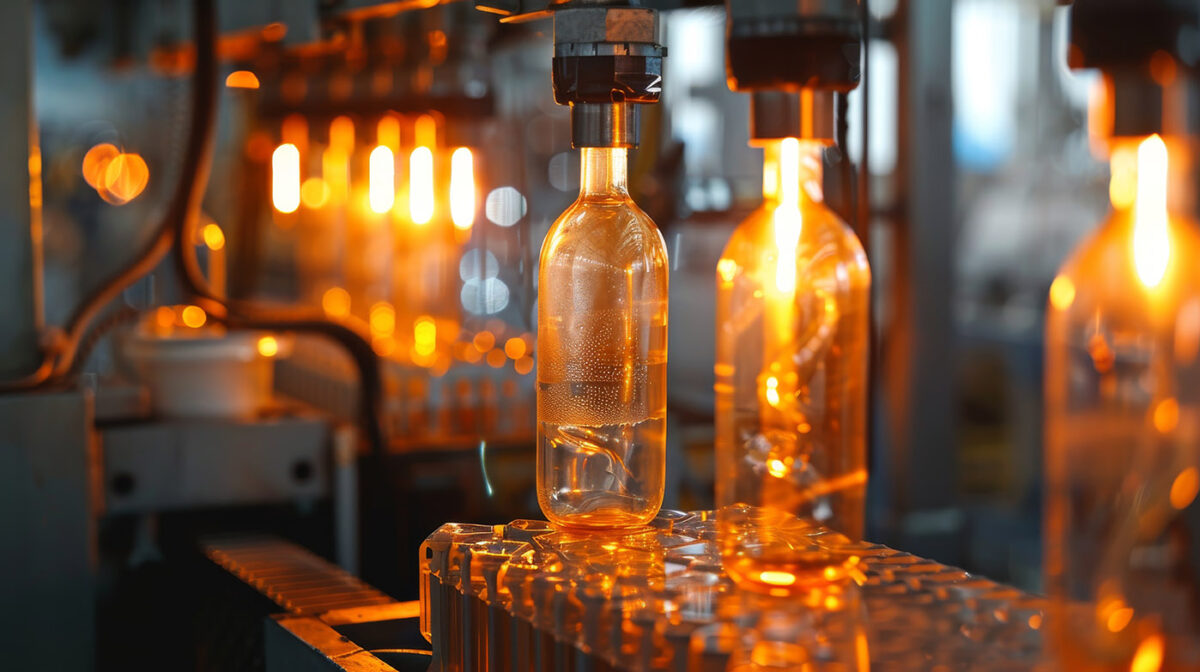
Trends shaping the future of blow molding.
3D Printing as an Innovative Solution
Blow molding also embraces 3D printing as an innovative solution. Traditional prototyping often results in unnecessary waste, high costs, and lengthy lead times. 3D printing simplifies these challenges by enabling rapid prototyping and small-scale production. This technology shortens lead times and speeds up product launches. In 2024, Serioplast and Unilever used 3D printing to create molds for new bottle designs. This approach reduced prototyping and pilot testing times by six weeks and lowered costs by 90%.
Finally, this process will continue evolving as automation, sustainability, and 3D printing shape future advancements. Companies must remain flexible, driving innovation to meet rising demand, lower costs, and prioritize sustainability.