Evaluating Fatigue Performance of 3D-Printed Carbon Fiber Composites
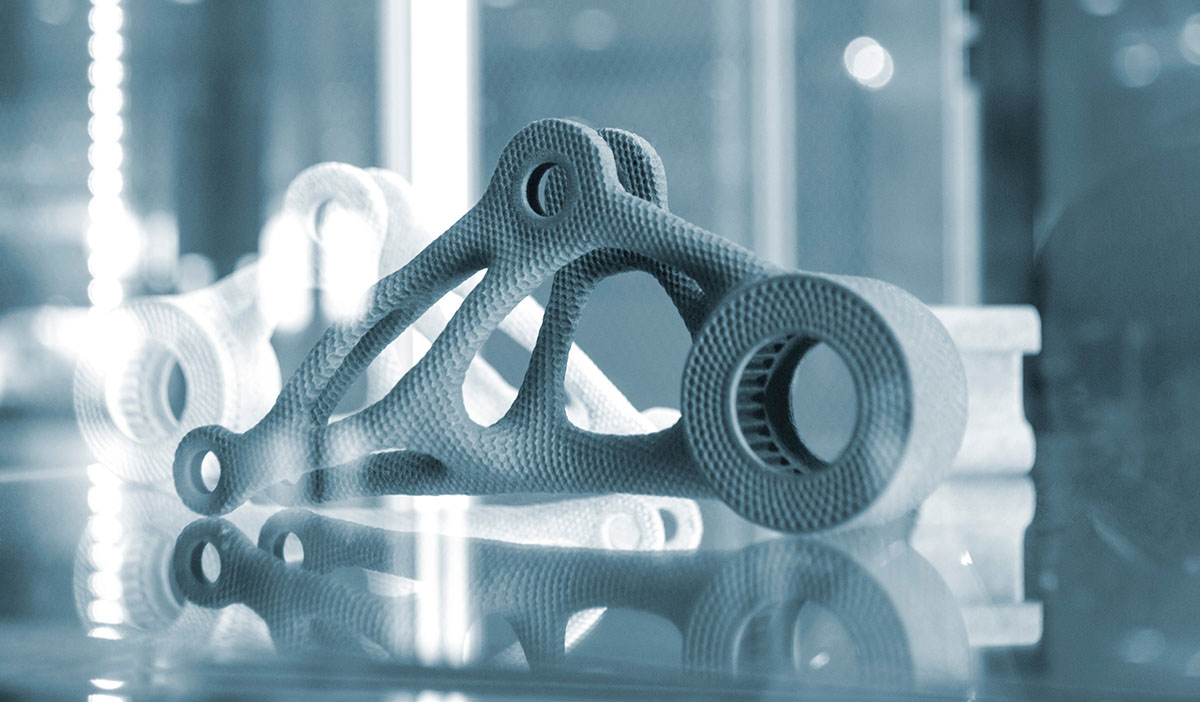
The Polymer Composites (PC) Journal by SPE has selected “Evaluation of Fatigue Characteristics of 3D-Printed Composites Reinforced with Carbon Fiber Using Design of Experiments” as its Editor’s Choice article for December 2024.
Advances in 3D printing technology have revolutionized material engineering, enabling the creation of custom composites with superior mechanical properties. A recent study by Imran M. Jamadar, Pavankumara Kamate, and Prasanta Kumar Samal examines the fatigue performance of 3D-printed composites reinforced with carbon fiber, focusing on PLA and ABS materials. Moreover, the research emphasizes how adding carbon fiber significantly enhances durability, making these composites suitable for demanding engineering applications. Additionally, the study highlights their potential use in aerospace, automotive, and robotics industries, where lightweight, durable materials are essential.
You can also read: AI-Driven Carbon Fiber.
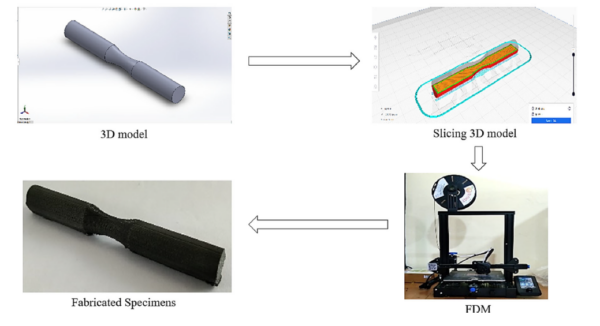
Flow chart for fabrication using FDM technique. Courtesy of Evaluation of fatigue characteristics of 3D printed/composites reinforced with carbon fiber using design of experiments.
Materials and Methods
The study investigated four materials: PLA, ABS, PLA reinforced with short carbon fibers (PLA-CF), and ABS reinforced with short carbon fibers (ABS-CF). Carbon fiber reinforcement significantly improved the strength, stiffness, and fatigue life of both PLA and ABS.
Researchers fabricated specimens using Fused Deposition Modeling (FDM) to evaluate fatigue performance. The manufacturing process used precise parameters, including a thickness of 0.16 mm and a nearly complete infill density of 99.99%. Specimens were tested in various orientations (0°, 45°/−45°, 90°) under different loads and rotational speeds using a custom-built rotating bending fatigue machine.
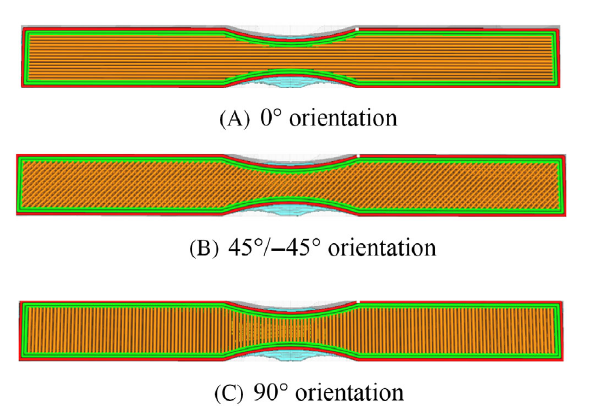
Specimen orientation. (A) 0° orientation. (B) 45°/-45° orientation. (C) 90°orientation. Courtesy of Evaluation of fatigue characteristics of 3D printed/composites reinforced with carbon fiber using design of experiments.
Optimizing Parameters with Taguchi Method
The study employed the Taguchi Design of Experiments (DOE) approach to optimize material composition and testing parameters. Using an L9 orthogonal array, the researchers systematically varied print orientation, load, and testing speed to determine their influence on fatigue life.
Results revealed that print orientation played a crucial role in durability. Specimens printed with a 0° orientation exhibited higher fatigue life compared to other orientations. The combination of lower applied load and moderate rotational speed further enhanced performance.
Key Findings for PLA- Carbon Fiber
PLA-CF demonstrated the best fatigue performance among the materials tested. A sample with 0° print orientation, a 0.5 kg load, and a 3000 rpm speed achieved the highest fatigue life of 57,540 cycles. Adding carbon fiber reinforcement significantly improved the durability of both PLA and ABS.
While PLA-CF outperformed all other materials, ABS-CF also showed marked improvements over pure ABS. This enhanced performance demonstrates the value of carbon fiber reinforcement in improving the mechanical properties of 3D-printed materials.
Industrial Applications
The superior mechanical properties of carbon fiber-reinforced PLA and ABS make them ideal for demanding aerospace, automotive, and robotics applications. Their lightweight nature and enhanced fatigue resistance enable the creation of durable yet cost-effective components for these industries. For example, PLA-CF and ABS-CF could be used in parts subjected to repetitive loading, such as gears, frames, or housings.
Broader Implications
This research underscores the potential of carbon fiber-reinforced composites to expand the utility of 3D-printed materials. By optimizing print orientation and processing parameters, manufacturers can produce significantly longer fatigue-life components, reducing costs and waste in industrial applications.
Furthermore, the study highlights the need to continue exploring advanced materials to improve sustainability and reliability in 3D-printed products. With their impressive performance characteristics, PLA-CF and ABS-CF pave the way for more durable and sustainable solutions in engineering and manufacturing.
To read the complete study click here.