Redefining Quality Control with Machine Learning
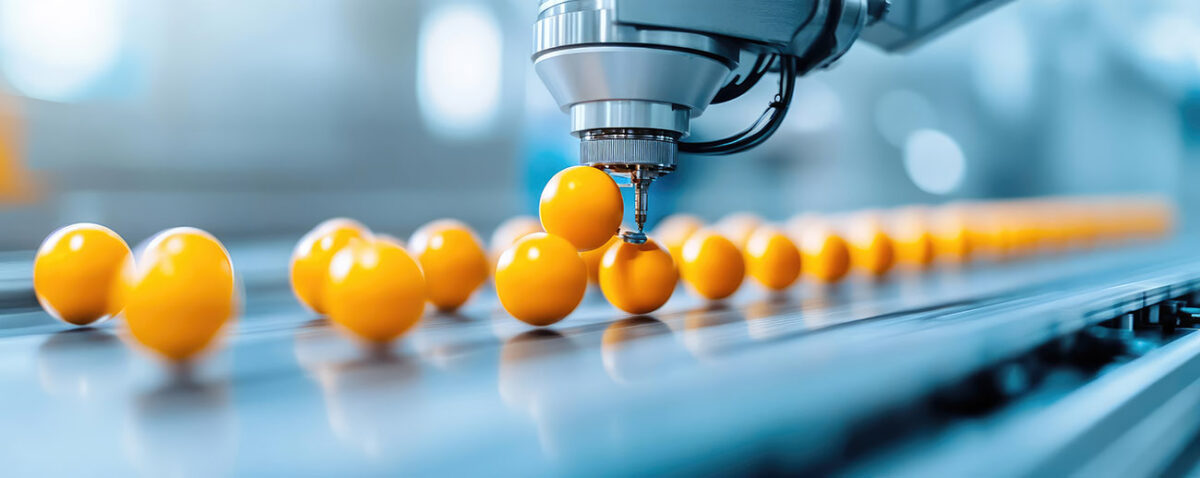
Machine learning (ML) is revolutionizing quality control in manufacturing, enabling faster, smarter, and more efficient processes. By addressing the limitations of traditional methods, ML enhances defect detection, waste reduction, and overall reliability.
Machine learning employs various advanced techniques and algorithms to revolutionize quality control processes in manufacturing. Among the most used are neural networks, random forests, and time series models.
You can also read: Transforming Extrusion Processes with Advanced Machine Learning.
Inspired by biological neural systems, neural networks effectively process non-linear, high-dimensional data, excelling in pattern recognition and defect detection tasks. Furthermore, random forests use ensembles of decision trees to provide accurate predictions, performing well in noisy or high-dimensional data environments. Also, time series models analyze historical data trends, predicting product quality and identifying potential defects before escalating. These algorithms, tailored to specific quality control tasks, improve precision, minimize waste, and enable real-time decision-making in complex manufacturing settings.
A Deeper Look into Predictive Quality Assessment
Predictive quality assessment is one of the most transformative applications of machine learning (ML) in manufacturing. It enables proactive measures to maintain high-quality standards. By leveraging historical data, machine learning models analyze patterns and trends to forecast the quality of upcoming products before they are produced.
This predictive capability allows manufacturers to anticipate and address potential defects, reducing waste, downtime, and overall production costs.
Predictive algorithms uncover patterns that signal emerging quality issues by analyzing multidimensional datasets, such as temperature fluctuations, vibration levels, and raw material attributes.
The benefits of predictive quality assessment extend beyond defect prevention. It also supports better resource allocation by identifying inefficiencies in production lines and streamlining operations. For instance, manufacturers can prioritize maintenance schedules based on predicted quality trends, reducing unnecessary downtime, and optimizing machine utilization.
Machine Learning in Injection Molding Quality Prediction
Selecting the right machine learning (ML) or deep learning algorithms is vital in manufacturing processes, as these methods are sensitive to the type and size of input data.
Injection molding, a particularly complex production system, involves multiple variables such as temperature, pressure, and velocity, which have nonlinear relationships. To address these complexities, researchers from Ulsan National Institute of Science and Technology utilized a dataset from Hanguk Mold an injection molding company in Ulsan, South Korea, to test various ML models for quality prediction.
The study identified key factors affecting injection-molded product quality, including molding temperature, hopper temperature, injection time, and cycle time, and showed that optimizing these significantly reduces defects. Using real-world data, the study validated that autoencoders outperformed traditional methods in both accuracy and F1-score, highlighting the value of ML in effectively managing the complexities of the injection molding process.
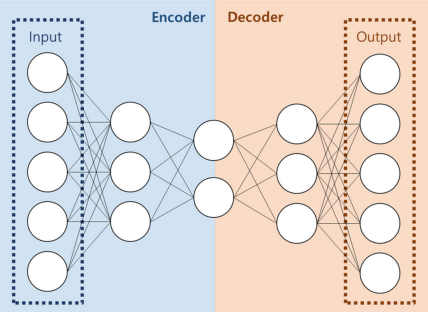
Autoencoder model explanation taken from MDPI.
Autoencoder models train from high-dimensional input to lowdimensional bottleneck intervals by repeatedly compressing and releasing the mapping process. In this process, an information bottleneck is created, and it automatically learns the ability to distinguish between important and non-critical features for restoring input samples. (Jung et al, 2021, p.9)
By integrating ML, manufacturers can enhance product consistency, minimize waste, reduce costs, and promote sustainable manufacturing practices.
Read full paper here: Application of Machine Learning Techniques in Injection Molding Quality Prediction: Implications on Sustainable Manufacturing Industry
Challenges in Predictive Quality Assessment
While the benefits of predictive quality assessment are evident, its implementation comes with challenges. The precision of predictions depends on the quality and significance of the input data. Missing or inaccurate variables, such as undocumented changes in machine settings or inconsistencies in raw materials, can hinder the effectiveness of the model. However, with advancements in data collection technologies and the growing sophistication of ML algorithms, predictive quality assessment is set to become an increasingly vital tool for achieving manufacturing excellence.