Energy Management Systems – Injection Molding III
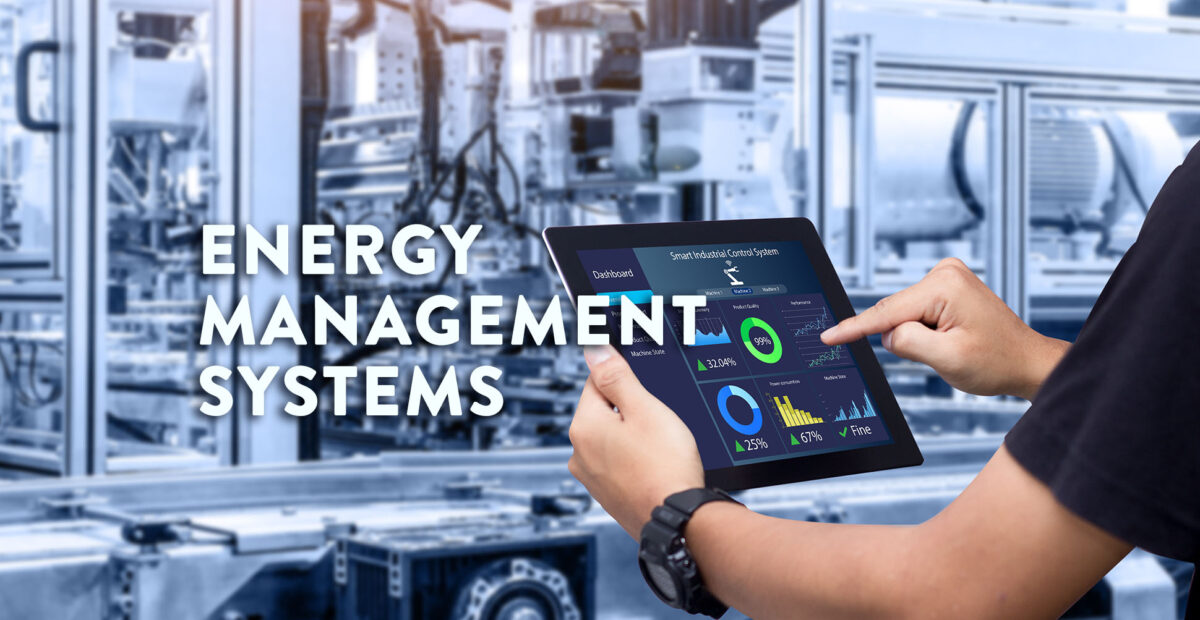
All-electric and servo-controlled machines are more energy efficient than older style hydraulic machines in both controlled trials and from industry operational data.
For some existing machines the installation of retro-fitted Variable Frequency Drives (VFDs) can be used to control the motors and provide a pay-back of less than 18 months.
Mold temperature controllers are not free. They cost money to operate and should be used only when really necessary. Flow and return piping should be insulated where possible to keep the heat where it is needed.
Energy efficiency in mold design is rarely considered but cooling, the size of sprues and runners and how the part is ejected all have energy use implications that should be considered at the design stage.
Action:
- Check the economics of all-electric and servo-controlled machines. The pay-back will make it economic to invest in new technology.
- Check the economics of retro-fitted VFDs. For large machines with high operating hours and long cycle times the pay-back may make it economic to invest in this technology.
- Check that mold temperature controllers are being used wisely and that all piping is insulated.
- Make sure that mold designers are aware of the need to consider energy use at the design stage.
Dr. Robin Kent is the author of ‘Energy Management in Plastics Processing’, published by Elsevier and Managing Director of Tangram Technology Ltd. (www.tangram.co.uk ), consulting engineers for energy and sustainability management in plastics processing.
Also read:
- Energy Management Systems – Injection Molding II
- Energy Management Systems – Injection Molding I
- Energy Management Systems – The Gas Bill
- Energy Management Systems – Assessing Performance
- Energy Management Systems – Electricity Bill
- Energy Management Systems – Getting Started
- Energy Management Systems – Site Surveys