3 Ideas To Optimize Your Costs in Injection Molding
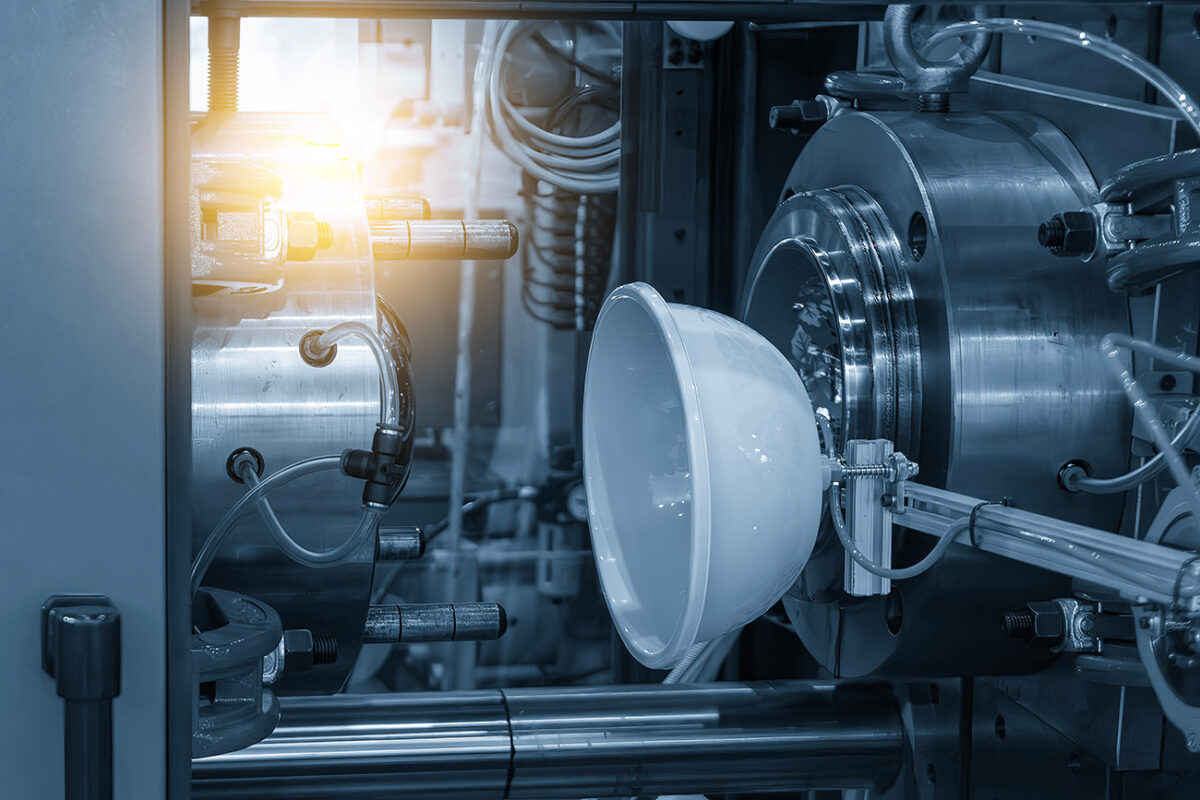
Controlling cooling, energy consumption, and downtime can help you reduce your cost per part using the resources you already have in your shop.
High-quality production is a shared priority for all molders. However, But an opportunity to differentiate is to control parameters determining part cost in injection molding. A detailed analysis of three aspects may give you a competitive cost advantage.
You can also read: Two Ways to Reduce Energy Consumption in Injection Molding
Make Cooling a Priority
Between 50% and 70% of injection molding time is spent cooling. So prioritize keeping your mold channels up and running at the top of their capacity. Besides reducing cooling temperature, ensuring that the water running is kept within a turbulent flow regime is crucial.
Installing equipment to measure flow and keeping flowmeters clean and unobstructed will lead to more reliable measurements. In Table 1, the recommended water flow ensures a turbulent flow above a Reynolds number of 4000, depending on the cooling channel diameter and water temperature.
Nominal Pipe Size (in) | Minimum Flow by Temperature | ||
(GPM) | |||
40 °F | 120°F | 200°F | |
0.250 | 0.88 | 0.31 | 0.18 |
0.375 | 1.16 | 0.42 | 0.24 |
0.500 | 1.41 | 0.51 | 0.29 |
Table 1. Approximate minimum water flow required for turbulence based on Reynolds of 4000. Source: Burger and Brown Engineering.
Also, make sure you avoid scaling. Water serves as a cheap and abundant medium for heat transfer, but its mineral content tends to deposit on cooling channel surfaces. This problem is greater with open cooling systems, such as cooling towers.
To avoid scaling, use a pump to circulate chemical descaling agents through the cooling systems. Also, measure flow as the mold goes out of service and keep a record, to account for the need for more drastic cleaning of the mold channels.
Reduce Energy Consumption
Energy comes into the injection molding system in the form of heat. Heat is brought into the system by friction (around 65% is generated by effect of rotation and back pressure) and electric resistances (around 35%).
A detailed knowledge of the energy consumption and the distribution of energy in each step of the molding cycle gives you information to optimize the process. Some times excessive packing pressure or back pressure can drastically increase energy consumption.
Also, it is important to understand when it is preferrable to increase energy consumption in the electric resistances on the barrel to reduce viscosity, and thus reduce pressure demand. As everything in molding, there is an optimum balance and it is worth to invest time finding the sweet spot.
Increase Uptime
This may seem obvious, but some companies do not monitor the downtime in their machines. It is often hard to find reliable statistics on how much do mold changes last, or how long did an unexpected maintenance take.
It is also hard to find the budget to invest in quick mold change systems, but a deeper look into the statistics may show you how to justify it. Also, if you need to upgrade your automation system, it may be wise to start understanding the time lost by failure in peripheric equipment.
A frequent cause for downtime is color change or resin change. Many companies are still reluctant to use purging systems. Purge seems to be more expensive per pound than PEAD, for example, but the performance of each material is totally different. An important practice in every technical molding is to use purging compound suited to the resin and process temperature you are using.