Impact of Temperature on Molded Part Quality
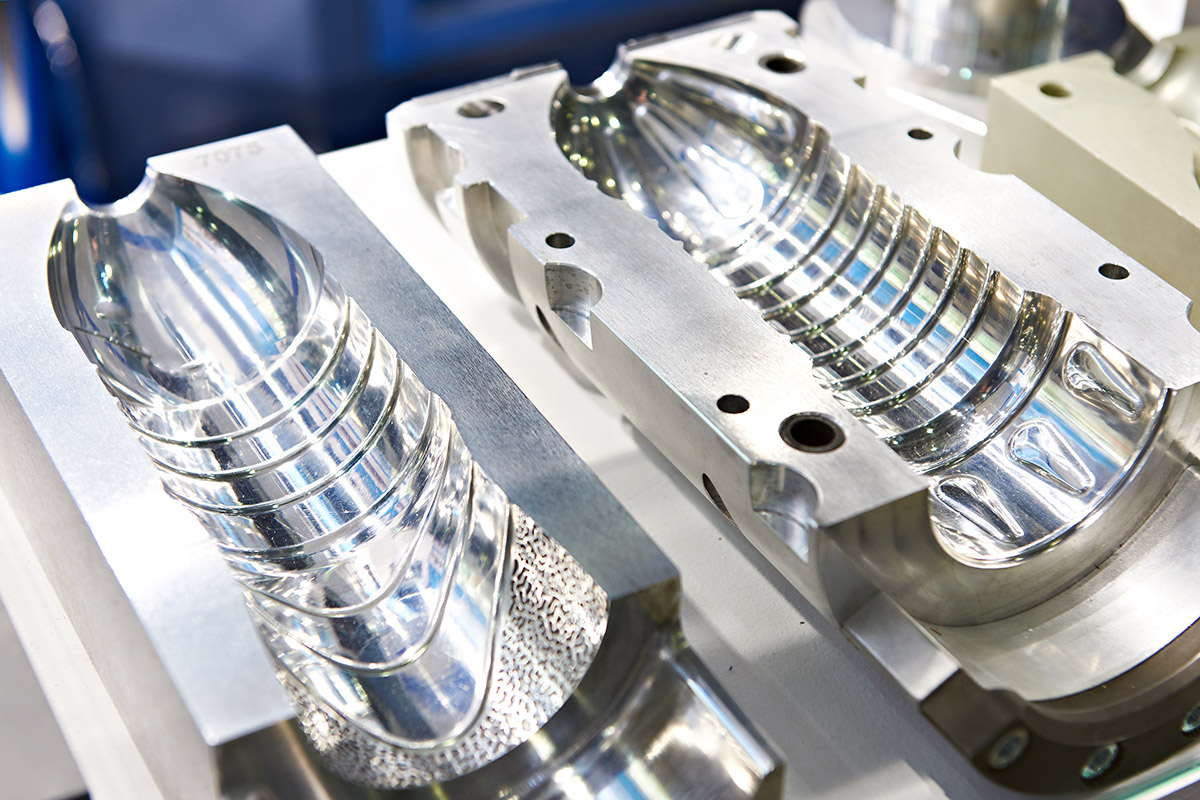
Temperature in injection molding processes plays a crucial role in part quality, either improving or compromising essential attributes.
Injection molding is a complex process, where several variables interact to determine the outcome. Quality, measured as compliance of dimensions, appearance, resistance and performance attributes, is determined by the combination of several factors.
You can also read: Essential Tips for Designing Injection Molded Parts
However, most of the defects normally encountered in injection molding parts come one major source: temperature – either the excess or lack of it in the melt or in the mold. Understanding how temperature affects your part can help you solve variations in product quality.
The Effect of Melt Temperature
Energy in polymers is the source of molecular movement. There will be some scenarios where you want to have more movement, and other scenarios where you want to have less.
Let us consider the first one: a higher temperature in the melt will help you fill better the mold, it will increase the part gloss, and it will give you better quality in the weld lines, where two flow fronts collide.
There is an additional advantage of molding at higher temperatures. You may have heard about viscoelasticity, which is a behavior particular to certain substances – plastics amongst them.
Viscoelasticity- The Dual Nature of Polymers
At lower temperatures polymers will exhibit a more evident elastic behavior, as a solid. At higher temperatures, the viscous behavior will dominate, and the material will relax stresses, as a liquid.
Also, higher melt temperature will of course lower the viscosity and improve homogenization. So if you have dispersion problems, make sure to increase the parameters affecting melt shear and heat dissipation: back pressure and rotational speed of the screw.
On the other hand, excessive melt temperature will lead you to higher cooling times, and under extreme circumstances it may induce degradation. It will also increase the molecular movements, and at the gate or in thicker regions of the part it may induce shrink marks.
How Mold Temperature Works
A lower mold temperature will consistently improve heat transfer and therefore lower molding time. It will also lead to a faster solidification of the part outer layer, and this thicker, more rigid skin may resist better the inner shrinkage, responsible for sink marks.
A higher mold temperature, on the other side, will improve part gloss and smoothen weld lines. Interestingly, it will also reduce residual stresses. As the polymer flows inside the mold, it will have more time to “accommodate” against the mold wall, instead of instantly freezing. So molecules will have time to relax before solidifying. Impact resistance and chemical resistance will therefore be improved.
Always check the recommended mold and melt temperatures advised by your material supplier, to ensure performance within specifications and to avoid risk of part or screw failure.