3D Printing in Space with Liquid Crystal Polymers
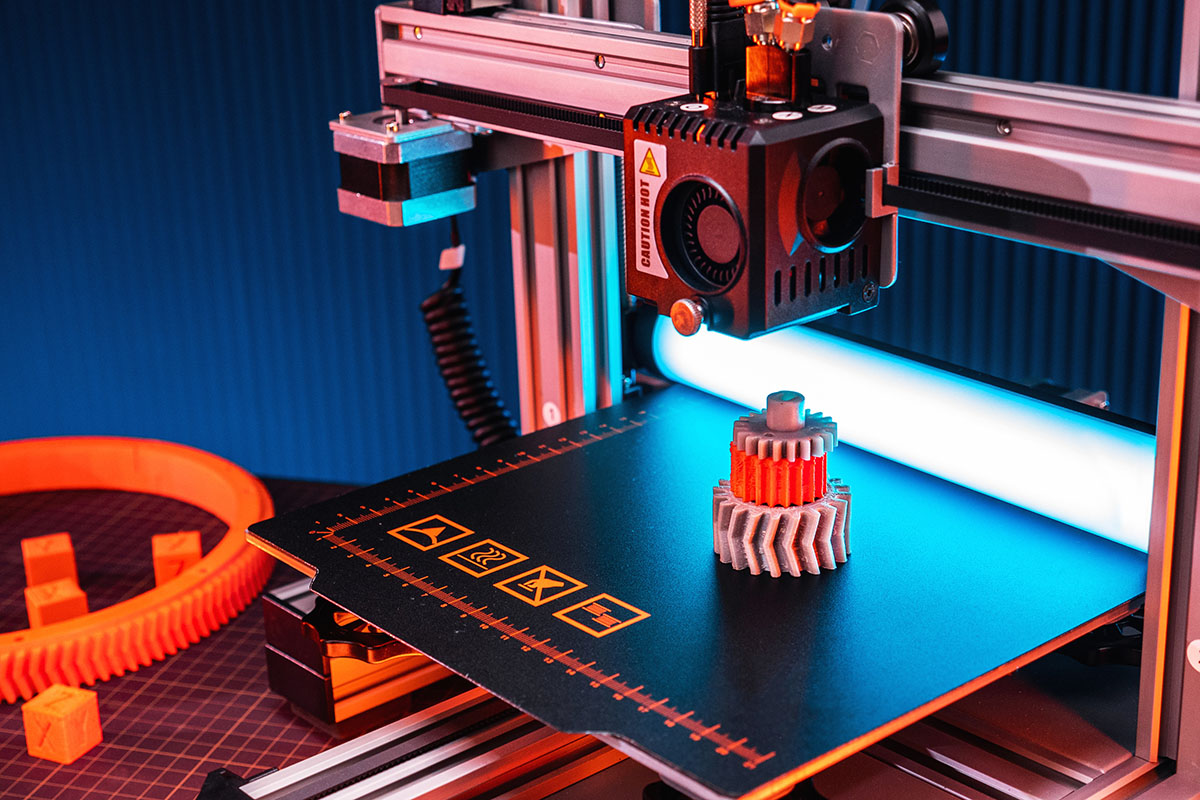
Thermotropic Liquid Crystal Polymers (LCPs) have emerged as a high-performance engineering polymer, comparable to PEEK and PEI, for 3D printing in space environments.
The European Space Agency (ESA) plans to establish a circular economy in space by 2050. They aim to develop in-orbit manufacturing, assembly, and recycling capabilities. To achieve this ambitious goal, ESA has explored innovative processes and identified fused filament fabrication (FFF) as a key technology. However, researchers face the critical challenge of finding printable polymer materials that withstand the harsh conditions of space.
You can also read: Composite 3D Printing in Aerospace and Robotics
Innovating for Space Circularity
Researchers from Switzerland and the Netherlands addressed this challenge by evaluating 3D printed thermotropic liquid crystal polymers (LCP). They subjected LCPs to four key space conditions, gathering valuable data on the material’s performance and potential for space applications.
Atomic Oxygen Exposure and Vacuum UV Radiation
They first exposed the materials to atomic oxygen and vacuum ultraviolet radiation. Atomic oxygen exposure caused surface erosion comparable to that seen in polymers like PEEK and PEI, demonstrating similar resistance. However, ultraviolet radiation caused significant damage, revealing the need for protective coatings to prevent degradation.
Electron Irradiation
During electron irradiation tests, the material developed green zones after exposure to 1 MeV electrons. Heating the samples to 200 °C removed these zones, showing that the structural changes were reversible.
Thermal Cycling Insights
Thermal cycling tests showed that low printing temperatures reduced mechanical performance, while high temperatures attenuate this effect. Researchers also observed anisotropy, with differences in performance depending on load orientation.
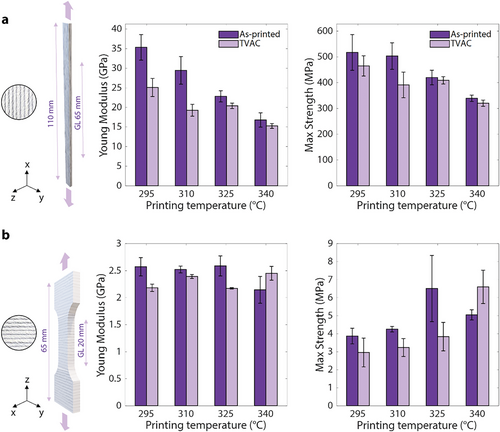
The figure illustrates the mechanical performance of LCPs at four different printing temperatures, both with and without exposure to TVAC (thermal cycling). A) Performance tested in the longitudinal direction, aligned with the printing direction. B) Performance tested perpendicular to the printing plane. Courtesy of 3D Printing of Liquid Crystal Polymers for Space Applications.
Mechanical Performance
You can also read: Bio-based Solvents for Polyimide Synthesis in Space Applications
Finally, although radiation exposure caused a slight decrease in storage modulus, tensile properties such as Young’s modulus and maximum tensile strength remained almost unchanged.
In conclusion, 3D-printed LCP demonstrates great potential for in-orbit manufacturing. Its mechanical properties and resistance to space conditions could maximize durability. It makes it an excellent alternative to polymers like PEEK and PEI. Additionally, the material’s easy recyclability, due to the absence of additives and compounds, strengthens its appeal for sustainable space applications.
To read the full article, click here.