Understanding Recycled Materials for Rotomolding
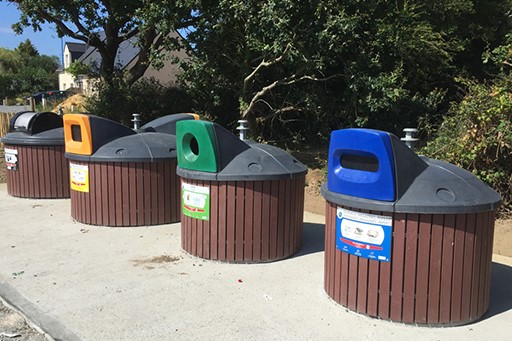
When we hear “recycled,” we often assume that the material originated from previously used products. However, “recycled” is evolving in rotomolding, driven by the need for more sustainable practices, market demand, and regulatory pressures.
The sector is integrating recycled and eco-friendly materials, but it still faces quality, cost, and scalability challenges. Companies use reprocessed materials like off-cuts, scrap, and post-consumer waste in sandwich structures, significantly reducing reliance on virgin polymers. Researchers have demonstrated that reprocessed materials can match the mechanical properties of virgin polymers. However, they also identified limitations such as reduced impact resistance and increased brittleness, which must be overcome for wider adoption.
You can also read: Rotational Molding: Balancing Sustainability and Performance
Leveraging Reprocessed Materials in Sandwich Structures
Reprocesses have the potential to transform the rotational molding industry’s sustainability landscape. According to a study published by Saifullah et al. (2022), reprocessed polyethylene (PE) materials used in rotationally molded sandwich structures demonstrated a 91% post-impact residual strength at low-impact energy levels compared to 93% for non-reprocessed materials.
This highlights reprocessed materials can be a sustainable alternative despite minor performance trade-offs, especially for less demanding applications. However, their integration into sandwich structures, such as skin-foam-skin configurations, is a valuable strategy for reducing the consumption of virgin polymers.
Off-Cuts and Manufacturing Scrap
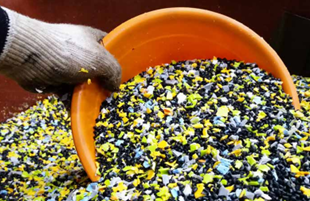
The cutting and molding processes leave behind remnants, which manufacturers typically discard.
The cutting and molding processes leave behind remnants, which manufacturers typically discard. Instead, they can grind these remnants into a fine powder and reintroduce them into the polymer matrix for new products. When used strategically in non-load-bearing layers of sandwich structures, these materials offer similar mechanical properties to virgin polymers at a lower environmental cost.
Post-Consumer Waste
Manufacturers blend recycled plastics, like polyethylene (PE), from household items or industrial packaging with virgin materials to create high-quality sandwich structures.
Manufacturers often process post-consumer waste into fine powders and mix it with blowing agents to create foam-core layers in sandwich structures. Although this approach requires meticulous quality control to avoid contamination, it has proven effective in maintaining structural integrity.
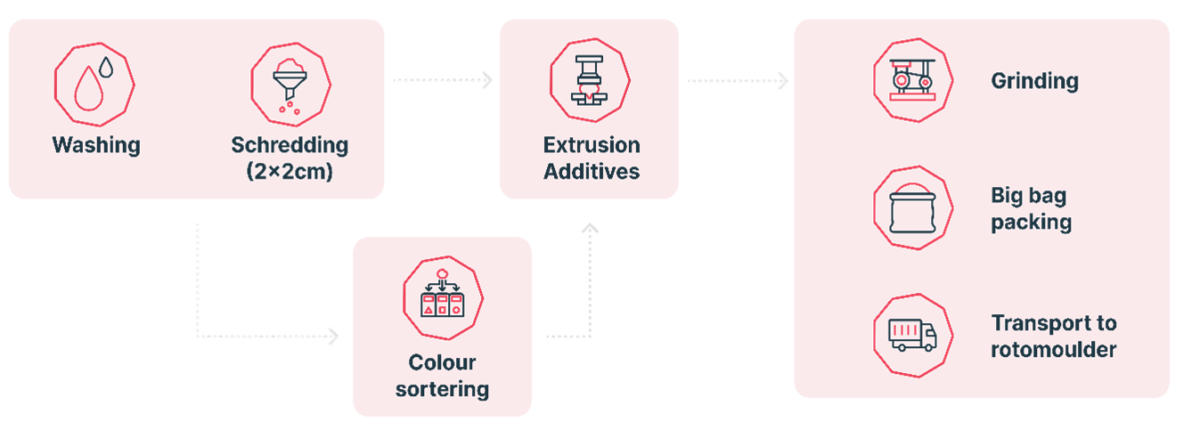
Recycling used rotationally molded products this way allows for the creation of high-quality rotational moulding material (rPE) suitable for manufacturing superior products. Courtesy of www.pentasmoulding.com
Regrind from Purge and Non-Used Moldings
Another valuable resource is reprocessed materials derived from defective parts or unused moulds. These materials are often reground to the desired size and incorporated into layers that do not require high aesthetic qualities but still maintain mechanical performance.
Challenges in Recycling Rotomolded Products
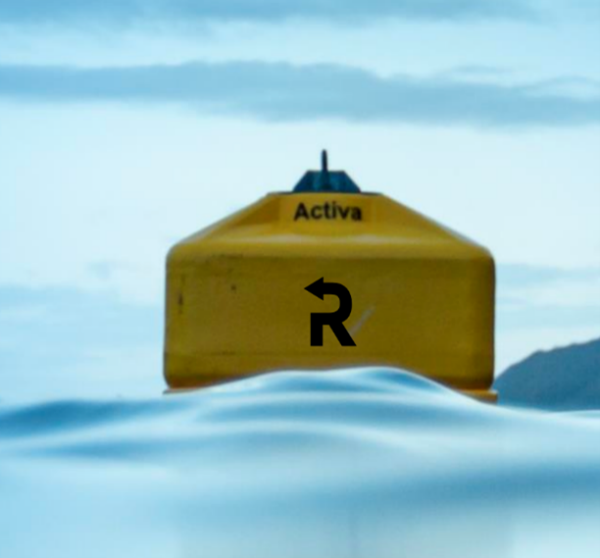
Introducing a specialized recycling label, like R-PE, for rotational moulding materials is essential to ensure proper sorting and efficient recycling. Courtesy of Pentas Moulding.
While reprocessed materials show promise, there are challenges in ensuring consistent quality, avoiding contamination, and maintaining mechanical properties. Some key strategies to address these challenges include:
To improve the use of reprocessed materials, advanced sorting and cleaning technologies are essential. These systems eliminate contaminants and ensure that recycling facilities select only high-quality materials for reuse. Additionally, optimizing blends of reprocessed materials with virgin polymers in strategic ratios allows manufacturers to balance sustainability with product performance. Furthermore, investing in material characterization technologies, such as X-ray tomography, is crucial. These tools ensure that reprocessed materials meet performance expectations, particularly in complex applications like sandwich structures, where precision and durability are critical.
By adopting these strategies, the industry can unlock the full potential of reprocessed materials, ensuring that they contribute effectively to sustainable manufacturing practices while maintaining product quality and performance.
You can also read: Sustainability Management Strategies – Create and Deliver a Staff Training Course
An excellent overview , not only for recycling related to the rotomolding area, also for the recycling market in general.
The ability to.up grade the recycling stream will be critical when selling or using the recycled resin in the market place. After all the recycled resin
will be competing with prime resin for the same application.