Two Ways to Reduce Energy Consumption in Injection Molding
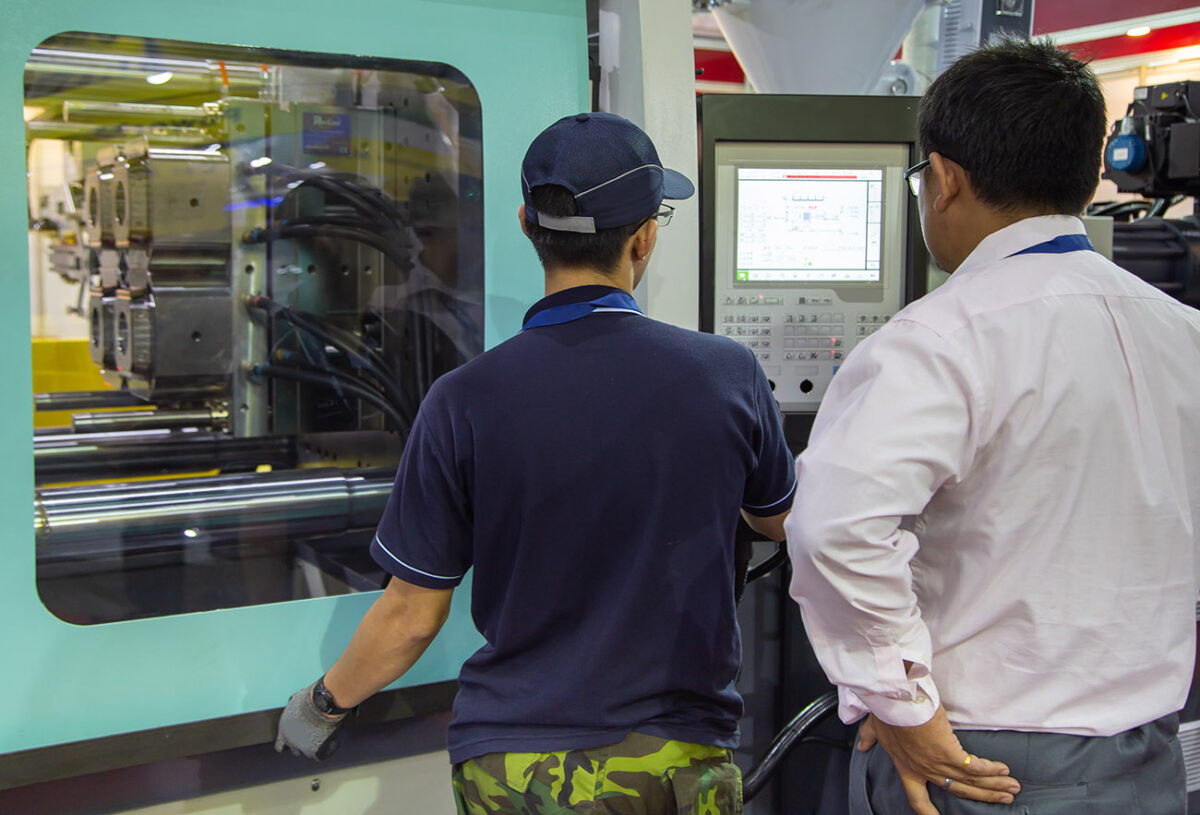
Energy consumption in injection molding can be reduced by paying attention to material selection and by closely watching different stages in process parametrization.
Energy is one of the most relevant variables determining a molded part cost. While some companies track globally the energy consumption in the shop, there is little understanding on how our everyday parametrization decisions affect energy consumption.
Depending on whether the machines use hydraulic, hybrid, or electric drives, they feature varying energy conversion systems and efficiencies. Also, the possibility to parallelize processes or shut down motors while inactive has lowered energy consumption levels in injection molding at least 20% down from where we were 20 years ago. In general, the energy savings have been better capitalized in lower clamping machines, as this is where electric drives have achieved the larger penetration.
The visibility of energy consumption in every machine, in dependence of material selection and process parametrization, enables reducing energy consumption typically between 7% and 13%.
Yet, while machines have always more sensors and more options to track and consolidate energy consumption data, it is still uncommon to find a processor focused on optimizing energy consumption via material selection and process parametrization.
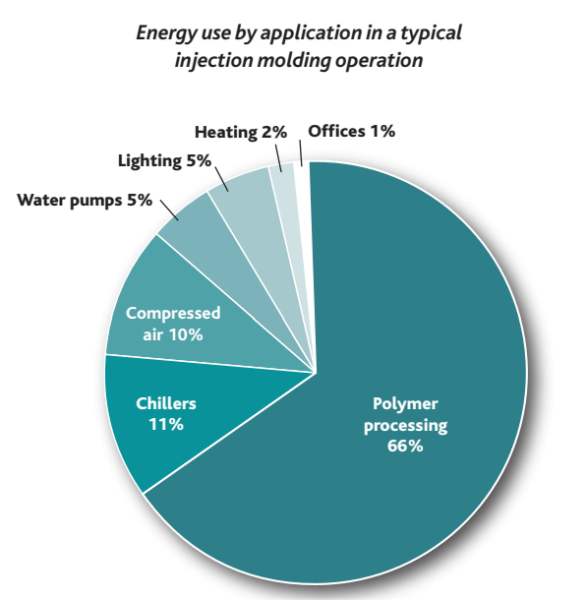
An Energy Saving Guide for Plastic Injection Molding Machines. Courtesy of Mobil.
Choosing The Right Material
Material selection tends to be a way to lower part costs or to increase part performance. But another take into material selection is energy consumption.
The more viscous the material – or the lower de MFI, the higher the energy required for plastification and injection. These more viscous materials may need higher temperatures to flow, and this will increase the energy consumption via higher energy demand in electric resistances along the barrel. Besides, they will impact cycle time, for the higher you heat, the longer you need to wait for the material to cool down.
Also, it is important to pay attention to variables such as HDT and thermal conductivity. HDT is the Heat Deflection Temperature, and it basically tells you how soon you may eject the part out of the mold; the higher the HDT, the faster your cycle time.
The same happens with thermal conductivity. While polymers are inherently quite good at isolating heat, you may find differences between grades when it comes to the ability of the material to transfer heat to the mold. So, you will always want to choose a material with higher thermal conductivity. This will shorten your cycle time and therefore reduce energy consumption associated to tempering in the mold.
Parametrization is The Key
The past couple of years I have been working with companies in the optimization of the molding process. A tool able to measure the energy consumption at each step of the process has proved to be very valuable at identifying potential improvement opportunities.
The figure provided by Kern IoP demonstrates energy consumption over cycle time for two different process setups. The curve shows all the process stages: closing the mold, volumetric injection, packing and holding, cooling and plastification, followed by mold opening. The area under each curve represents energy consumption over time, which serves as the parameter to optimize.
Reducing speed in injection molding allowed to reduce the peak in energy consumption in this region. When the screw run backwards, the energy was reduced by a proper combination of counterpressure and a progressive set up of rotation speed.
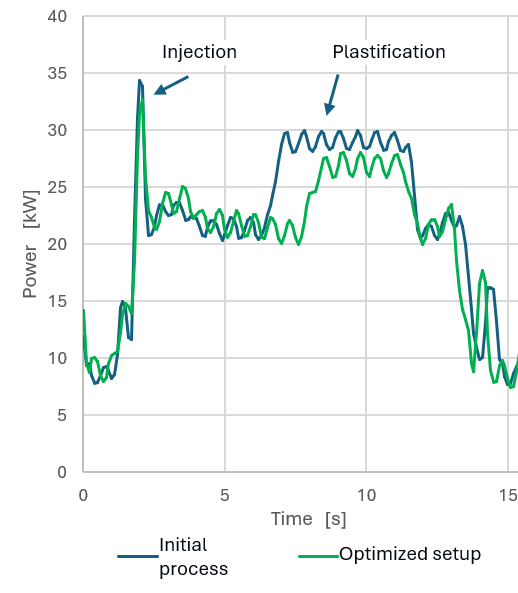
Kern IoP is a tool providing a detailed description of energy consumption over cycle time. Through the correct combination of process parametrization it is possible to reduce the area under the curve. Courtesy of Kern IoP.
It was also evident that closing the mold too fast did not make a significant difference in cycle time but it did on energy consumption. All these optimizations where done using Kern IoP. The resulting energy savings where 5,7%, without any modifications in material, mold or machine.