Oyster Shells to Seawool: A Fabric Revolution
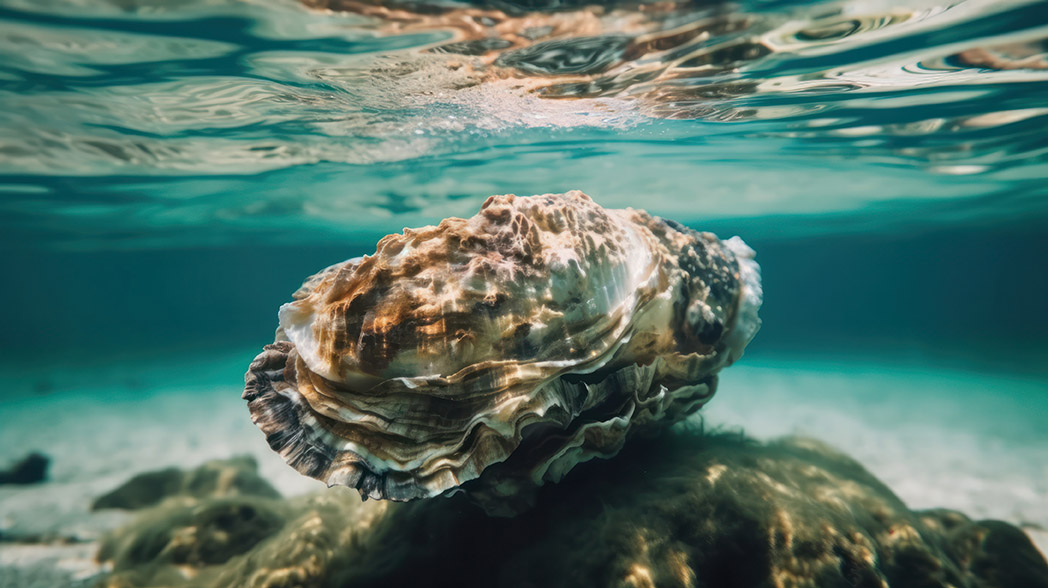
Seawool is produced by grinding oyster shells into nanobeads combined with recycled polyester. This process upcycles the waste material, sparking a fabric revolution in sustainable textiles.
A Sustainable Fabric Journey
In 2010, Wang founded Creative Tech Textile, a company initially focused on producing eco-friendly fabrics from recycled plastic bottles. However, Wang sought to create something more innovative. Partnering with a research institute, he began experimenting with oyster shell residue. By 2013, the team perfected a fabric formula that blended finely ground oyster shells with recycled polyester yarn, resulting in Seawool. This material mimics wool’s insulating properties but with additional environmental benefits.
Seawool: A Magical Yarn
Seawool is created by grinding oyster shells into nanobeads combined with recycled polyester. This process gives the fabric unique properties, such as low thermal conductivity, UV protection, and odor resistance. The carbon-capturing minerals in the shells enhance the sustainability of the production process by eliminating the need for water and reducing the overall carbon footprint.
A Global Market for Seawool
Wang’s factory processes approximately 100 tonnes of oyster shells each year, resulting in the production of 900 tonnes of Seawool. According to the Taipei Times, this fabric has successfully penetrated the outdoor and sustainability-focused fashion markets in Europe and the U.S. Consequently, it has generated millions in revenue. Moreover, Wang has not only transformed waste into a valuable resource but has also created a profitable, eco-friendly solution that underscores the importance of sustainable innovation.
Even though seawall is using discarded oyster shells and reusing poly/plastic bottles, it is still plastic and will not break down in nature. Bravo to the idea, but we still have a plastic problem to begin with.