Lightweight Plastics: Transforming Metal-Based Applications
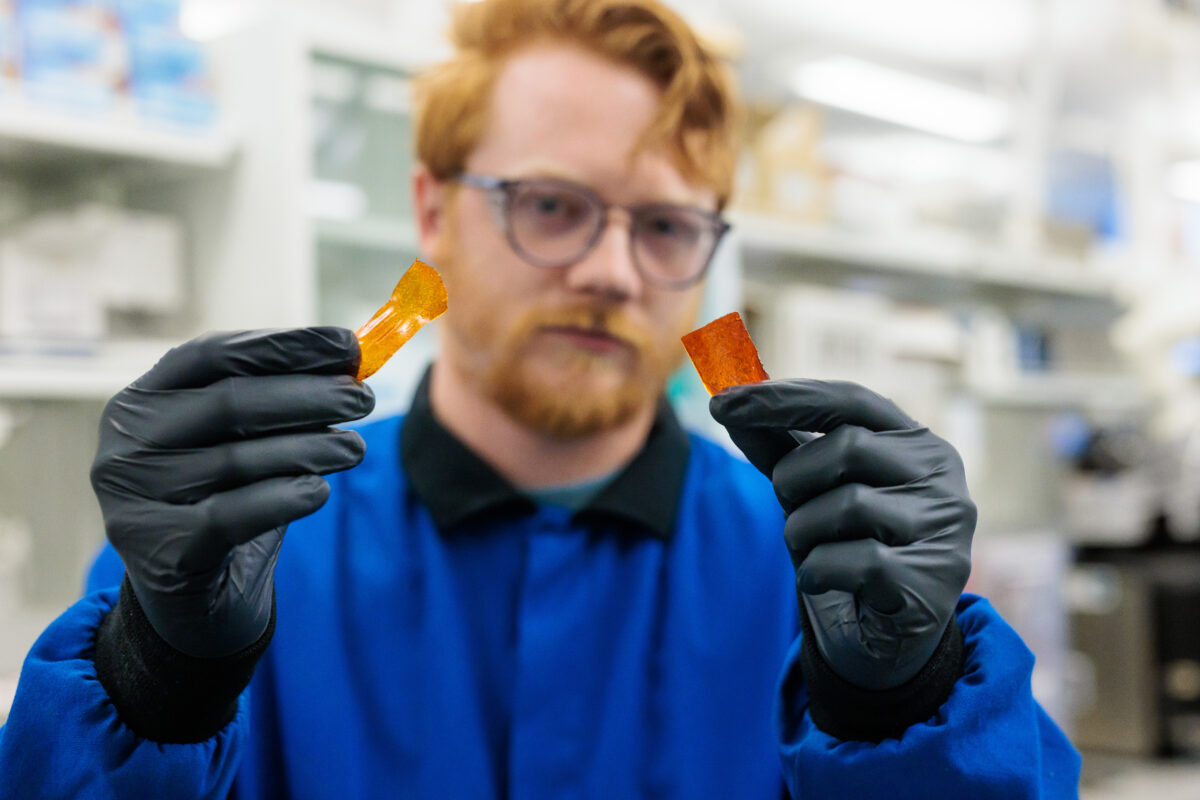
Manufacturers increasingly use lightweight yet durable plastics to replace metals, with new applications emerging regularly.
Plastics not only perform well in applications that previously used metals like aluminum, brass, and stainless steel but also reduce material and assembly costs. A single plastic part often replaces multiple metal components, further improving efficiency. As a result, highly versatile polymers are rapidly gaining ground in industries such as aerospace, automotive, industrial, agriculture, oil and gas, healthcare, and others.
You can also read: From Metal to Plastic: Game-Changing Approach to Electric Vehicles
Established Materials Replacing Metals
Depending on the specific application, various plastics, from commodity-grade to engineered, effectively substitute for metals.
Common plastics like polyethylene, polypropylene, polystyrene, and polyvinyl chloride offer fatigue resistance, impact strength, chemical resistance, and environmental tolerance. Engineered grades such as nylon (PA6, PA66, PA12), polycarbonate, ABS, acrylic, acetal, and structural foam provide similar qualities with added strength and flexibility.
High-performance plastics like polyether ether ketone (PEEK) have proven ideal for parts like gears. According to Victrex, PEEK reduces weight by up to 80% when replacing metal and provides mechanical properties five times stronger.
Aztec Plastic highlights Torlon polyamide-imide as the highest-performance, melt-processable thermoplastic available. Aztec has processed Torlon across a wide range of applications. It is extremely lightweight, robust, and highly customizable.
Torlon’s strength surpasses that of other engineered plastics at temperatures up to 500°F. It also offers superior chemical resistance and impact strength, even at cryogenic temperatures. Torlon’s many grades suit applications ranging from electrical connectors and bearings to transmission parts and oil and gas components.
Another alternative, Delrin acetal homopolymer, outperforms acetal copolymer in high-load applications like gears, safety restraints, and medical devices. Its low friction, high wear resistance, and durability make it suitable for extreme temperatures.
Reinforced Plastics and Emerging Alternatives
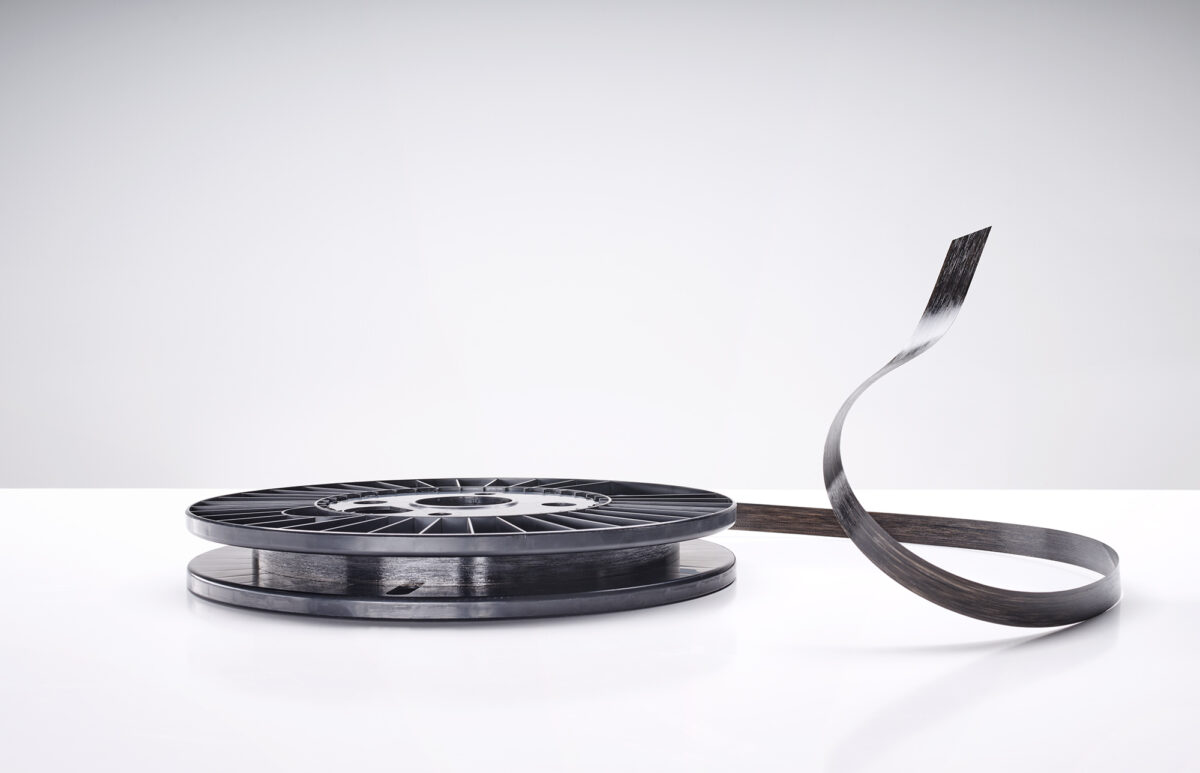
DOMO has developed a polyamide-based unidirectional composite tape called TECHNYL LITE. The tape can be reinforced with glass or carbon fiber and be used to replace metals in not only automotive applications but in the construction and sports and leisure industries. Courtesy of DOMO.
Reinforced plastics, particularly in automotive applications, provide strength and heat resistance. Short glass fiber-reinforced plastics suit parts like cylinder heads, while long glass fibers allow thinner, lighter designs. Carbon fiber-reinforced plastics, about 40% lighter than typical materials, are ideal for large parts such as side panels.
The development of stronger plastic materials continues to offer lightweight alternatives for various industries. In 2024, Celanese introduced Zytel XMP70G50, a polyamide reinforced with 50% short glass fibers, to replace metals in vehicle chassis and structural components.
At Fakuma 2024, DOMO Chemicals unveiled a polyamide brake pedal for heavy-duty trucks, which is 27% lighter and 60% cheaper than its metal counterpart. DOMO also introduced TECHNYL® LITE, a composite tape reinforced with glass or carbon fibers, ideal for automotive, construction, and sports applications.
Researchers from the University of Chicago developed a pluripotent plastic material in February, capable of shape-shifting multiple times. This material, made of dynamic covalent bonds, can be tuned to different mechanical properties, from rigidity to flexibility.
MIT researchers in 2022 created a polymer stronger than steel and lighter than plastic, using a novel polymerization process. This two-dimensional material self-assembles into sheets and can be mass-produced.
The University of Delaware’s Center for Composite Materials developed TuFF in 2020, a short-fiber composite that can be stamped into complex shapes, expanding its use as a metal replacement.
E-Mobility and Energy Solutions with Plastics
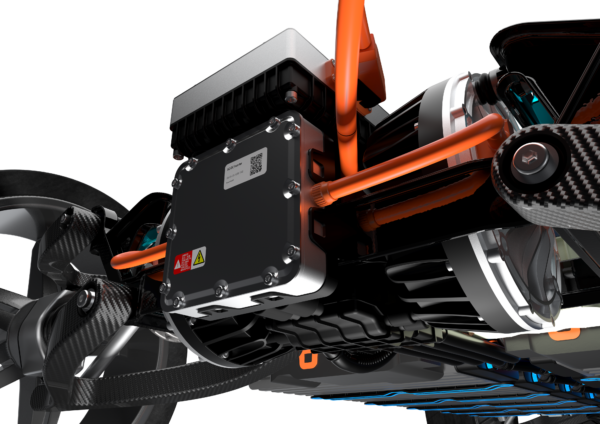
Celanese designed the Zytel XMP70G50 polyamide material, a PA 66 reinforced with 50% short glass fibers, to replace metals in chassis and structural components for internal combustion vehicles and EVs. Courtesy of Celanese.
Plastics continue to replace metals in many high-demand applications, with SABIC introducing several innovative solutions to the market.
- The LNP™ STAT-KON™ compound from SABIC is now utilized in fuel cell plates, cutting electrode weight by 70% and costs by 40%.
- SABIC and Lubrizol have collaborated to create sustainable soft-rigid material solutions for consumer electronics. This pairing combines SABIC’s LNP for rigid substrates with Lubrizol’s ESTANE ECO TPU for durability, drop protection, and a non-slip surface.
- In electric vehicle battery packs, SABIC’s NORYL resins replace metals, effectively reducing weight while accommodating battery expansion during temperature fluctuations.
- Additionally, SABIC developed a plastic-metal hybrid housing for DC-DC converters, achieving a 30% reduction in manufacturing costs compared to traditional aluminum housings.
Non-Metal Medical Miracle
In September, the FDA cleared a 3D-printed PEEK spinal implant that has surpassed titanium in over 15 million applications.
Nvision Biomedical Technologies developed the PEEK Interbody System using PEEK-Optima material from Invibio Biomaterial Solutions. PEEK-Optima mimics bone and offers superior imaging capability, allowing surgeons to monitor bone fusion more accurately.
Surgeon Dr. Steven Lee praised PEEK-Optima for preventing subsidence (bone collapse) and enhancing bone growth into the implant itself. He emphasized that the new implant’s strength, radiolucency, and bone ingrowth properties would improve surgical outcomes for his patients.