Enhancing Biodegradability with Foaming Technology
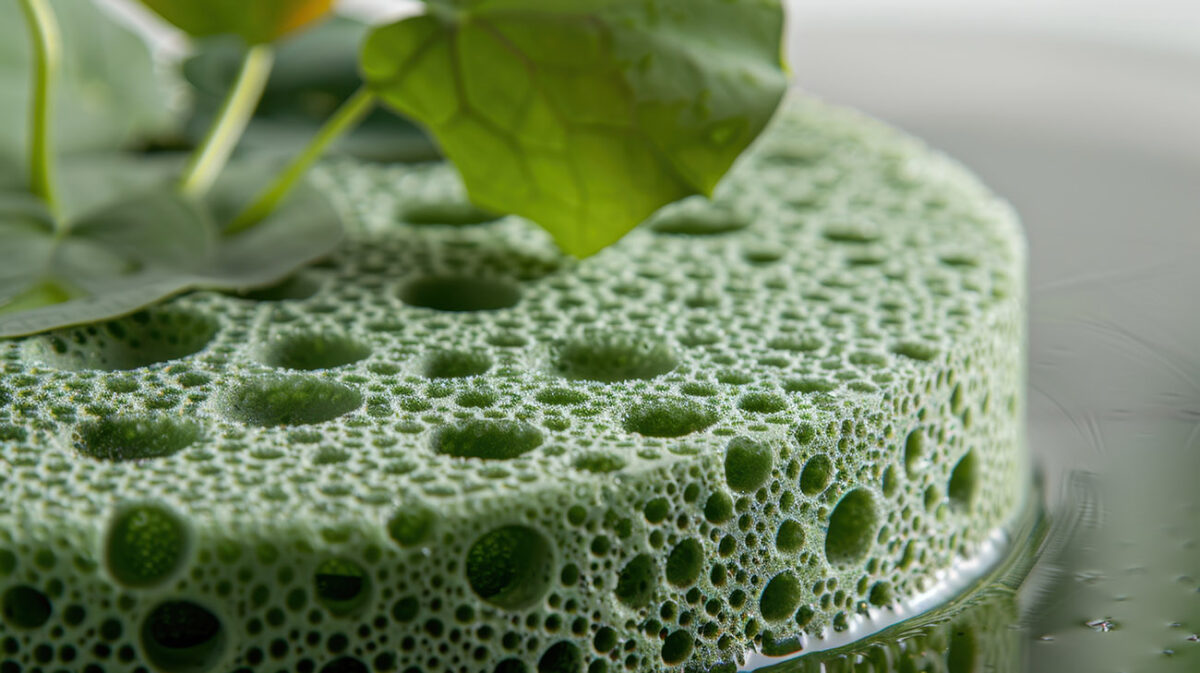
Foaming biodegradable bioplastics offers a revolutionary approach to improving both material efficiency and environmental impact.
By integrating microstructural pores into bioplastics, manufacturers can significantly reduce environmental persistence while enhancing the product’s usability. This innovative method holds great potential for various industries, particularly for applications such as sustainable food packaging.
You can also read: Biodegradable Polyester Fiber for Fashion Solutions
Superior Performance of Cellulose Diacetate (CDA) Foams
Recent advancements in foamed bioplastics, especially cellulose diacetate (CDA) foams, have demonstrated clear benefits over conventional plastic foams like polystyrene. CDA foams, when tested in marine environments, showed considerably faster degradation rates compared to polystyrene. After 36 weeks, CDA foams lost 65-70% of their mass, a striking difference compared to polystyrene’s persistence. In fact, foamed CDA materials degrade about 15 times faster than their solid counterparts, providing a crucial advantage in reducing environmental waste.
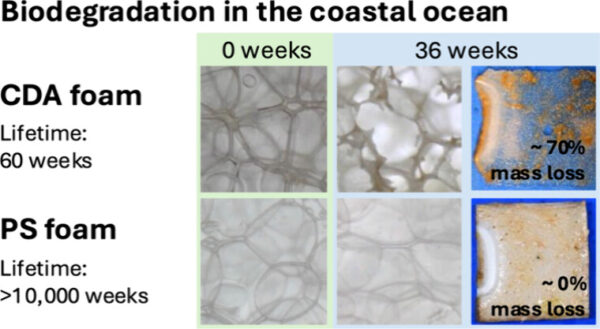
Mismanaged plastic products should be designed to reduce environmental impacts by improving material efficiency and minimizing persistence. Foaming biodegradable bioplastics, by adding microstructural pores, is proposed to achieve this goal. Courtesy of Foaming Enables Material-Efficient Bioplastic Products with Minimal Persistence.
Boosting Material Efficiency and Sustainability
In addition to their biodegradability, foamed bioplastics significantly improve material efficiency by using less raw material to produce the same volume. This reduction in resource consumption not only lowers production costs but also decreases the overall environmental footprint. Therefore, foamed bioplastics, like CDA, become a preferred choice for industries prioritizing sustainability. Companies that adopt these materials can minimize resource use while maintaining the quality and functionality of their products.
Overcoming Challenges with Traditional Plastic Foams
One of the main challenges with traditional plastic foams, such as polystyrene, is their long-term persistence in the environment. These materials resist degradation and contribute significantly to pollution in landfills and oceans. In contrast, biodegradable foams like CDA not only degrade faster but also align with green chemistry principles. Additionally, this innovation helps reduce reliance on non-renewable resources, offering a more environmentally responsible alternative.
Economic and Environmental Impact
Adopting foamed bioplastics presents significant societal and economic benefits for companies and industries alike. Replacing traditional foams with biodegradable alternatives, such as CDA, could save millions of dollars annually by optimizing material use. Moreover, the environmental advantages are substantial, with reduced plastic waste and faster degradation contributing to long-term sustainability. As a result, this shift toward foamed bioplastics represents a key step in addressing the global plastic waste crisis.
Foamed biodegradable bioplastics, such as CDA, provide an innovative solution that balances material efficiency and environmental protection. As industries increasingly prioritize sustainability, adopting bioplastics that degrade faster and use fewer resources will be crucial. Moving forward, foamed bioplastics will play a pivotal role in reducing plastic waste and supporting a more sustainable future.
To read the complete study click here.