Digital Twin in Manufacturing and Beyond
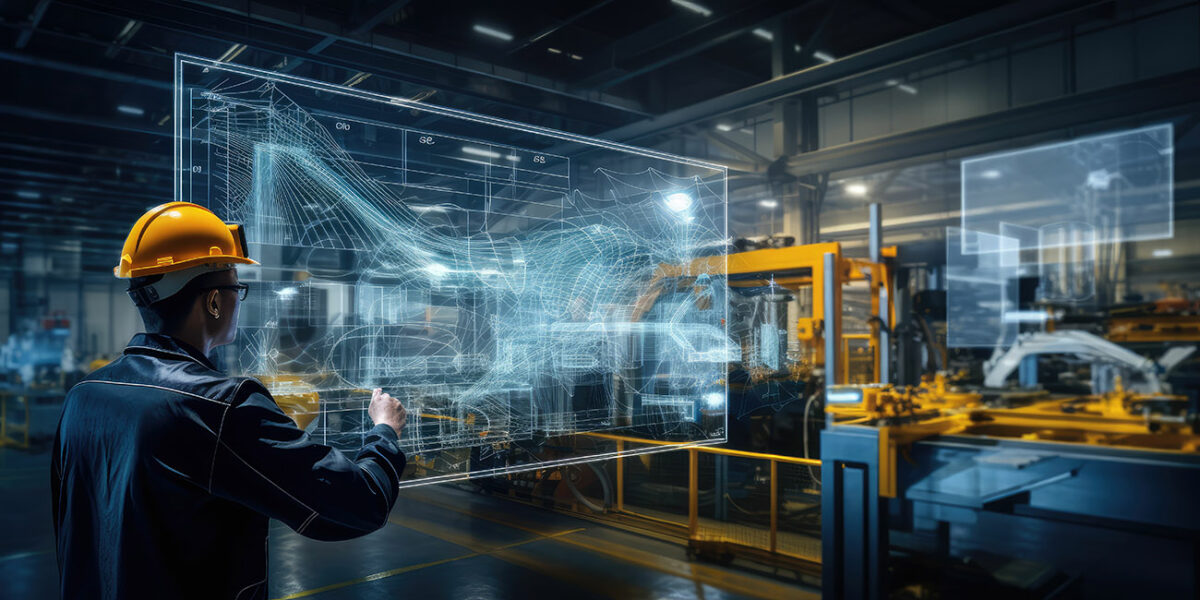
A digital twin includes real-time data and continuous feedback from the physical world. Simulation is typically a static or hypothetical model used for scenario-based analysis.
Both digital twin and simulation are related concepts, they just have key differences in scope, functionality, and real-time application.
You can also read: Maximizing Injection Molding Simulation
A brief History
The concept emerged from NASA’s Apollo space program in the 1960s, where engineers created two identical space vehicles—one on Earth and one in space. This “twin” concept allowed real-time simulation and troubleshooting. The formal term “Digital Twin” was introduced by Michael Grieves in 2003 at the University of Michigan. He defined it as the digital equivalent of a physical product, aimed at improving product lifecycle management (PLM). Prior to this, a similar concept called “product avatar” was introduced in 2006 but was later replaced by Digital Twin terminology.
Advances in Information and Communication Technologies (ICTs), such as CAD, IoT, big data, AI, cloud computing, and 5G, have fueled the rise of Digital Twins. These technologies enable the seamless connection between physical objects and their digital counterparts, allowing for real-time data exchange and advanced simulations.
Digital Twin Definition
A Digital Twin is a digital replica or virtual model of a physical object, system, or process that allows to simulate, analyze, and optimize the performance of its real-world counterpart in real-time. Through this digital representation, industries can monitor conditions, predict outcomes, and make data-driven decisions. The integration of real-time data from sensors, advanced simulations, and machine learning enables the digital twin to evolve dynamically, reflecting changes in the physical object or system. It is composed of:
- Physical entity: The real-world asset or system.
- Digital representation: A model that mirrors the physical asset.
- Data connection: A link between the physical and virtual, driven by real-time data exchange.
Applications of Digital Twins span industries, including manufacturing, healthcare, smart cities, and aerospace, enabling functions such as predictive maintenance, performance monitoring, and optimization.
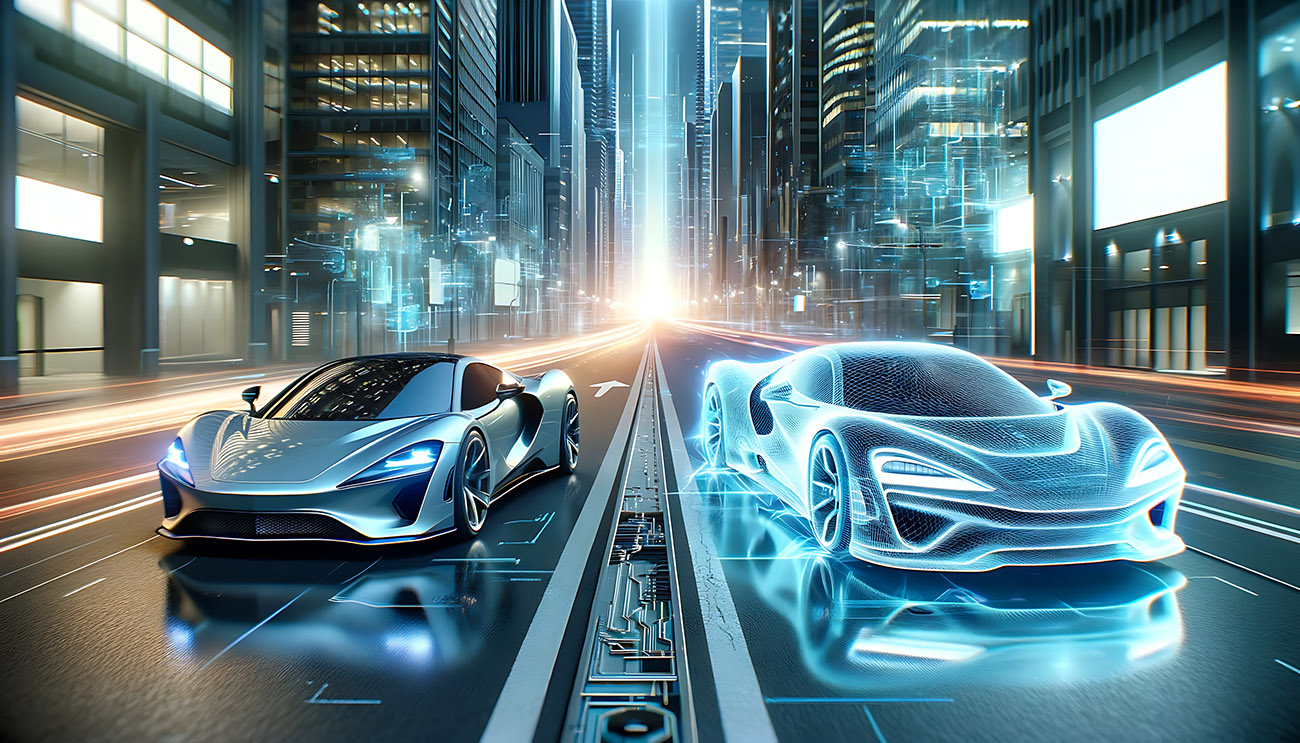
A Digital Twin is a digital replica or virtual model of a physical object, system, or process that allows to simulate, analyze, and optimize the performance of its real-world counterpart in real-time.
Digital Twin Vs. Simulation
While Digital Twins and simulations are related concepts, they have key differences in scope, functionality, and real-time application.
Criteria | Digital Twin | Simulation |
Connection to Real-World Objects | Real-time, dynamic digital replica continuously updated with real-world data from sensors. | Static or isolated model, replicating scenarios based on pre-set conditions, without real-time data. |
Real-Time Feedback | Provides live feedback, continuously evolving with changes in the physical system. | Typically used for one-off analysis, does not evolve with real-time data. |
Scope | Covers the full lifecycle of a product or system, allowing ongoing interaction and optimization. | Focuses on specific phases, such as testing or predicting performance under certain conditions. |
You can also read: Leveraging AI to Speed Product Design Simulations
Application on Plastics Processing
The applications of Digital Twin technology span various phases of the product lifecycle. However, in plastics processing, its most significant advancements have occurred in injection molding. Initially focused on part-filling simulations decades ago, efforts have now progressed toward achieving a full Digital Twin.
One of the milestones are what the companies like SIMCON and SIMPATEC performed with the lead manufacturer ENGEL. Here the injection molding parameters can now be exchanged digitally between simulation software and molding machines, enabling efficient two-way communication. This capability allows first, real-time updates to machine settings, second, fostering better collaboration between engineers and machine operators and finally, a creation of continuous feedback loop for ongoing optimization.
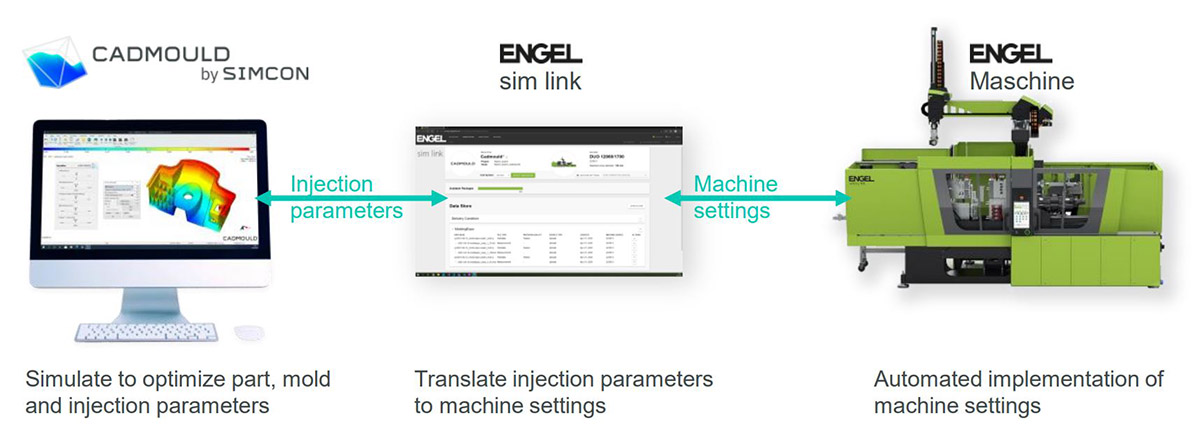
The injection molding parameters can now be exchanged digitally between simulation software and molding machines, enabling efficient two-way communication. This capability allows first real-time updates to machine settings, second, fostering better collaboration between engineers and machine operators and finally, a creation of continuous feedback loop for ongoing optimization. Courtesy of SIMCON
Future Development Work
The future development work to improve the reliability and robustness of digital twin:
- Must address the challenges of data integration and complex phenomena modeling.
- Should focus on bridging the gap between low-level digital design and the high demands placed.
- requires detailed quantitative modeling to enhance the accuracy and performance.
Conclusion
Digital twin technology is revolutionizing the whole industry, including plastics, by enhancing design and development, optimizing production processes, and enabling predictive maintenance. By creating a virtual replica of the plastics transformation process, manufacturers can gain unprecedented visibility and control over their operations. This leads to higher-quality parts, increased efficiency, and reduced costs. As this technology continues to evolve, its adoption is likely to become a standard practice in the industry. It will be a driver for further innovations and improvements.
To read more: Review of digital twin about concepts, technologies, and industrial applications