Why Use Hot Runner Systems for Injection Molding?
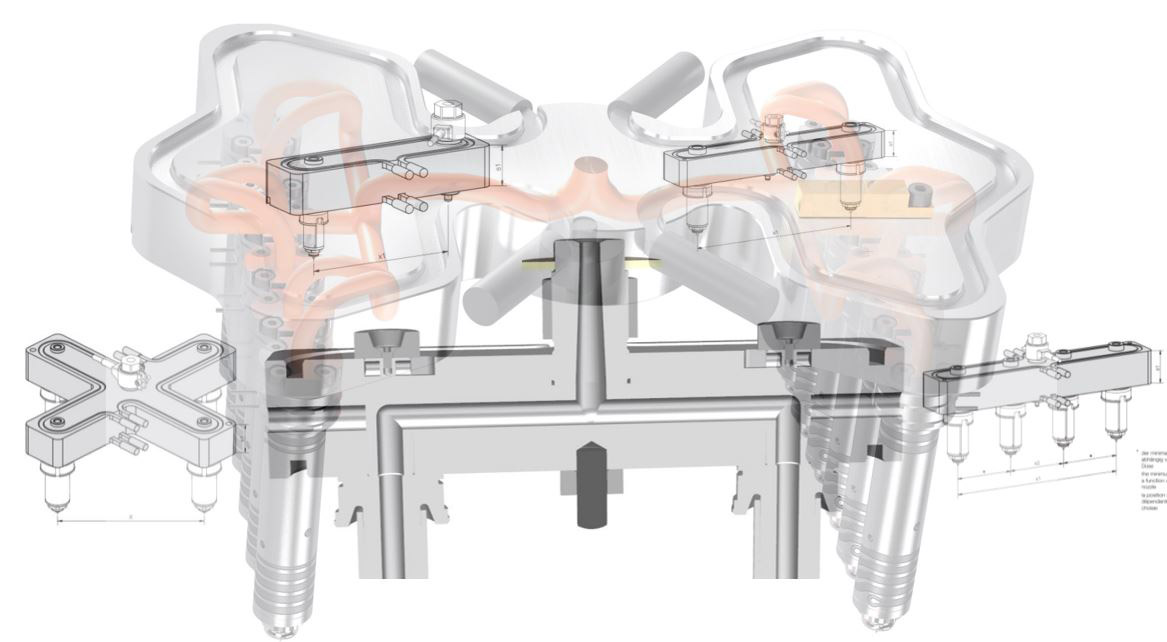
For more than 70 years, hot runner systems have become a vital technology in plastic injection molding, improving production efficiency and enhancing product quality.
Hot runner systems involve a specially designed manifold that maintains the temperature of the plastic melt, allowing continuous flow through the runners to the mold cavities without solidification. This technology, which differs significantly from traditional cold runner systems, has transformed how plastic parts are manufactured, offering a range of advantages in various industries.
You can also read: Injection Molding Factors Influencing Part Quality,
What is a Hot Runner System?
A hot runner system consists of a heated manifold and nozzles in plastics injection molds that keep the thermoplastic material in a molten state throughout the molding process. This system is thermally isolated from the rest of the mold, ensuring the plastic stays liquid until it reaches the mold cavities. Hot runners are used for molding thermoplastics and crosslinking plastics (elastomers and thermosets). They allow for precise flow control, reducing waste, shorter cycle times, and improved part quality.
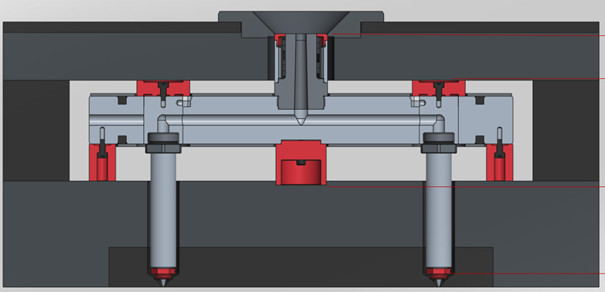
A hot runner system consists of a heated manifold and nozzles in plastics injection molds that keep the thermoplastic material in a molten state throughout the molding process. This system is thermally isolated from the rest of the mold, ensuring that the plastic stays liquid until it reaches the mold cavities. Courtesy of Witosa
A Brief History of Hot Runner Systems
The hot runner system’s development began in the mid-20th century as industries sought to improve the efficiency of injection molding processes. In the 1960s and 1970s, the early versions of hot runner systems emerged with the company Mold-Masters. Husky Injection Molding Systems was another significant player in the early development of hot runner systems. Husky focused on improving hot runner technology to meet the needs of industries requiring precision molding. In the 1980s, companies like Incoe Corporation, also contributed by introducing new designs that improved temperature control and reliability.
Advantages
- The key economic advantage of hot runner systems is the elimination of material waste. Unlike cold runner systems, where plastic solidifies in the runners and must be removed and reprocessed, hot runners keep the material molten, reducing scrap and the need to regrind the runner. This is particularly beneficial when using expensive or technical thermoplastics, as it minimizes raw material costs.
- Additionally, hot runner systems allow for shorter cycle times. Since there is no need to wait for runners to cool, production is faster. Furthermore, machines can be smaller, as the absence of large, solid runners reduces the required shot volume and clamping forces.
- From a technological standpoint, hot runner systems offer several significant benefits. They allow for automated processes, as runners do not need to be demolded. This is especially advantageous in high-volume production where efficiency is critical. The gating system can be positioned optimally for better flow control, reducing defects and improving the quality of molded parts.
- Another benefit is the ability to minimize pressure losses, as hot runners allow larger runner diameters, facilitating better material flow. Technologies like valve gate nozzles provide even more precision by controlling the flow of material into individual cavities, which enables advanced techniques like cascade gating. Cascade gating allows the material to flow smoothly through multiple nozzles, reducing pressure/clamping force demand, eliminating flow lines and improving part aesthetics.
- Hot runner systems also enable longer holding pressures, reducing shrinkage and warpage in parts. This improves the dimensional accuracy and strength of the molded parts.
You can also read: Plastics Injection Molding: Definition, Benefits and Applications
Disadvantages
- Thermal degradation of sensitive materials can occur if they stay in the heated manifold for too long (residence time). This can be a significant problem for materials with narrow processing windows. Precise temperature control is critical, as inconsistent temperatures can lead to non-uniform filling and part defects.
- The complexity of the equipment requires extensive maintenance to prevent issues which can interrupt production and increase costs. This issues could be leaks or cloggings.
- Higher initial cost of the system and the already mentioned maintenance can also lead to higher operational costs. The defects can include leakage, heater failure, or wear from filled materials .
Hot Runner Innovation Milestones and Trends
- HASCO’s Streamrunner technology is a 3D-printed hot runner system that revolutionizes injection molding by optimizing melt flow with free-form channels. This additive manufacturing approach enables a highly customized and efficient runner layout, reducing pressure loss, improving part quality, and lowering cycle times. The main advantages include minimal wear due to streamlined flow paths, enhanced cooling, and the ability to handle complex geometries.
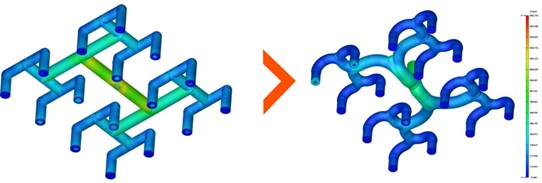
3D-printed hot runner system that revolutionizes injection molding by optimizing melt flow with free-form channels. This additive manufacturing approach enables a highly customized and efficient runner layout, reducing pressure loss, improving part quality, and lowering cycle times. Courtesy of Hasco
- INCOE in partnership with Cavity Eye, integrate sensor technology into their Direct-Flo hot runner systems. These sensors measure variables such as temperature and pressure within the hot runner or tool, providing precise data for improved process control. The data is logged, visualized through software, and can trigger alarms if deviations occur, ensuring consistent quality and operational efficiency. The system enhances Industry 4.0 compatibility, allowing for networked solutions and data mining, leading to better decision-making and reduced downtime.
- Witosa’s hot runner technology features the world’s first additively manufactured, single-piece nozzle, designed for energy efficiency and precision. Utilizing Hexagon technology, the nozzle’s weight is optimized, reducing energy consumption by up to 35%. The innovative design includes an integrated, tamper-proof fastening system and advanced thermal management. With printed insulation, the system holds consistent temperature with a deviation of less than 5°C. Additionally, it eliminates the need for a temperature booster typically required in conventional systems.
You can also read: Next Gen Injection Molding: Best Practices
Now why?
Hot runner systems have transformed the plastic injection molding industry by offering a range of economic and technological benefits. While the upfront costs and maintenance requirements are higher, the advantages in terms of material savings, faster cycle times, and improved part quality make them an excellent choice. As technology continues to evolve, hot runner systems will likely become even more efficient and adaptable, further enhancing their role in modern manufacturing.
To read more: Hot Runner vs. Cold Runner: Why should you choose a hot runner system