Fast-Track Aging Simulation for Plastic Components
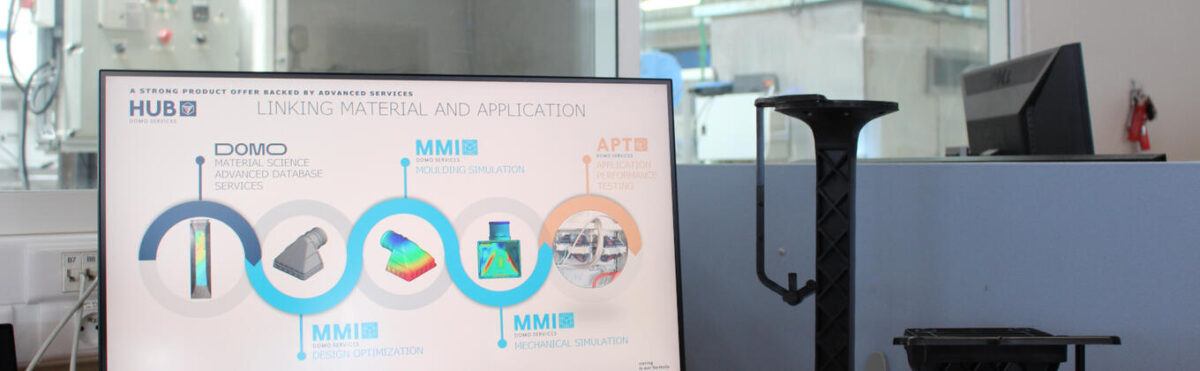
The release of injection-molded thermoplastic parts requires long-lasting and cost-intensive aging tests. A simulation-based approach to assess the aging of thermoplastic parts would constitute an essential asset for any company.
Simulation can reduce development time and increase the opportunities for part optimization. Pursuing this goal, DOMO and nine other partners started a collaborative project (Thermofip) in 2019. The consortium also included OEMs, automotive suppliers, software companies, and academic institutions. The project finished successfully in 2023.
You can also read: Leveraging AI to Speed Product Design Simulations
Development of an Aging Simulation Workflow
The Thermofip project had two primary goals. One was to develop an industrial simulation workflow for estimating the effects of aging on the mechanical performance of thermoplastic parts. The project focused on glass fiber-reinforced polyamide parts exposed to coolants, such as water or water/glycol mixtures. The second goal was obtaining the required material data for feeding the models in the simulation workflow. The project targeted the automotive cooling and oil system market and considered a business perspective. This market experiences steady growth and is avid for low-weight solutions, where polyamides could constitute a pertinent material choice.
You can also read: Nylon Replacing Metal Won a SPE Automotive Award
Numerical Implementation in Commercial Software
The project successfully delivered a breakthrough simulation chain for estimating the mechanical response of a polyamide part in contact with coolant over time. Specifically, Arobas Technologies and Hexagon (Digimat) implemented the required models into their commercial software solutions. As a result, this simulation method is now available for any user. Furthermore, the FE-based workflow consists of several simulation steps. First, a thermal transient simulation is conducted. Next, diffusion simulation of the coolant species and a simulation of hydrolytic aging are performed. Finally, the process concludes with a mechanical simulation that includes the effects of fiber orientation and aging.
Study Case: Filtration Oil Module
The project consortium showcased the capabilities of the simulation method on an industrial case study. They simulated an accelerated aging conditioning and the subsequent burst pressure test of an oil module (designed by Sogefi Filtration) made of glass fiber-reinforced polyamide 66.
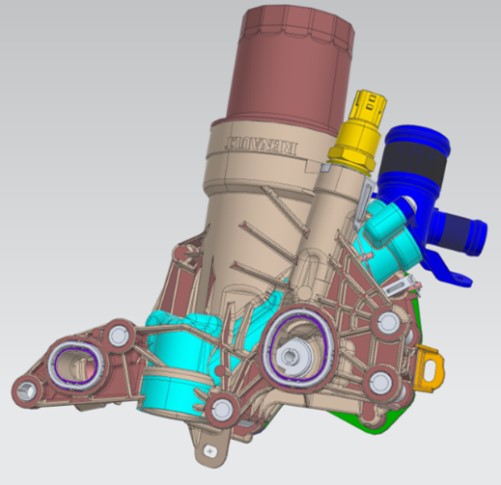
The project simulated an accelerated aging conditioning and the subsequent burst pressure test of an oil module. Courtesy of DOMO.
The analysis of the mechanical simulations revealed that failure occurs as a combination of stress concentration, hydrolysis, and fiber orientation. This result highlights the relevance of considering all those factors in the design optimization of injection molded components.