Essential Additives for Plastic Modification
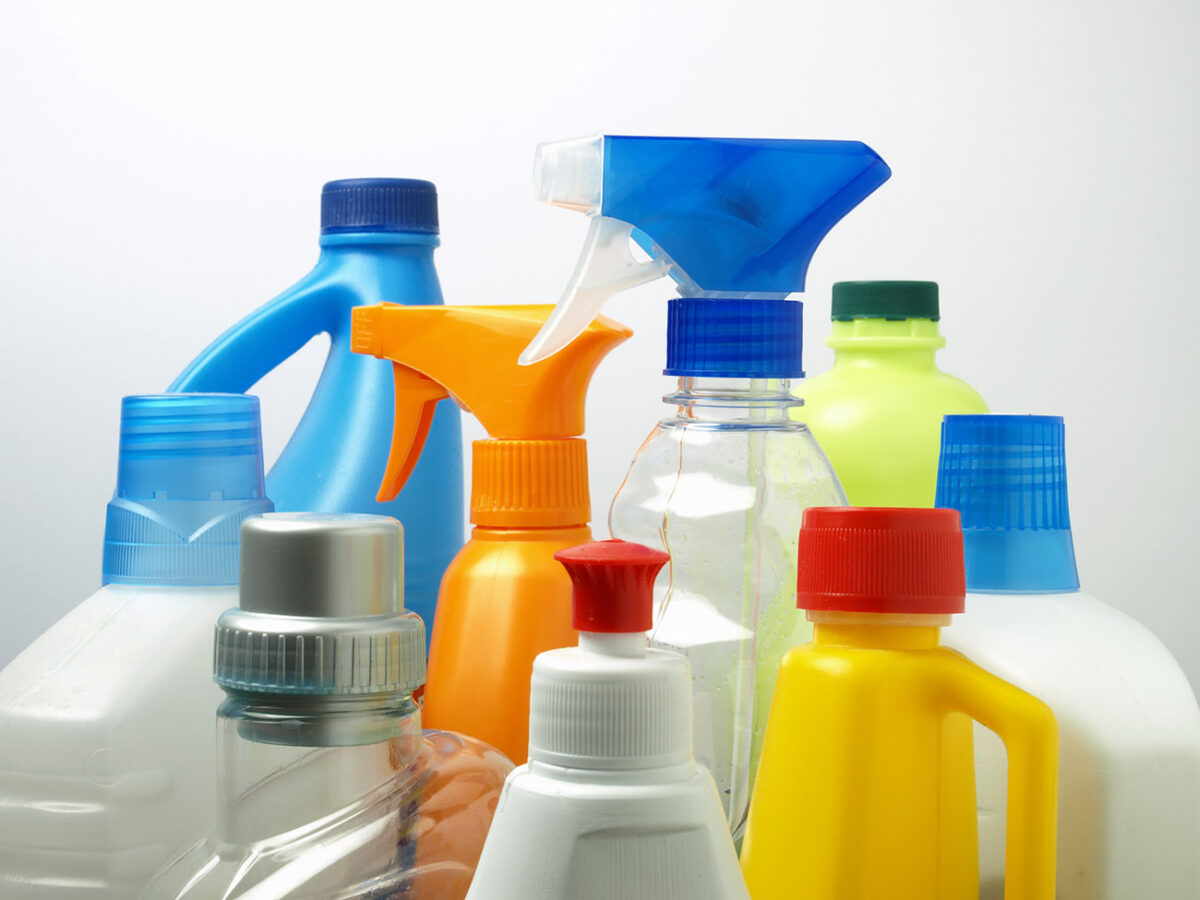
Plastic modification involves selecting the right additives to enhance the polymer’s properties, such as mechanical strength, surface quality, or processability.
Additives play a crucial role in improving the performance and lifespan of the product, and choosing the correct ones can significantly affect the final product. Here’s a breakdown of the most common additives and their specific functions in plastic modification.
You can also read: Fluorination in Packaging and PFAS Contamination
Processability
Lubricants, release agents, and stabilizers are commonly added to plastics to enhance their processing ease during manufacturing.
- These additives reduce friction and wear during production, enabling smoother molding or extrusion processes. For example, lubricants can decrease the viscosity of the polymer melt, making it easier to flow into molds and reducing energy consumption.
- They can reduce die buildup.
- They facilitate faster color changeovers.
Enhancing Mechanical Properties
Additives such as plasticizers, toughening agents, and impact modifiers are used for applications requiring greater toughness, flexibility, or impact resistance.
- Plasticizers increase the flexibility of rigid plastics, making them more suitable for products like PVC cables or flexible containers.
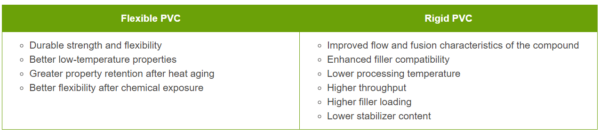
Different types of PVC resins require different impact modification additives. Courtesy of SpecialChem.
- Impact modifiers are crucial in applications where high strength and durability are needed, such as in automotive components.
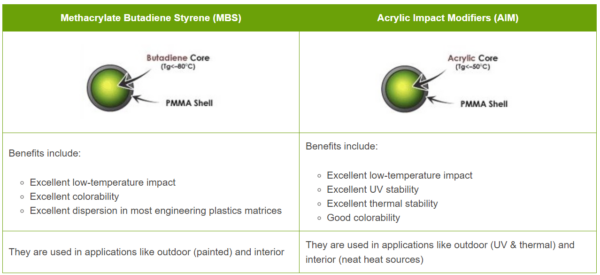
MBS impact modifiers vs. acrylic impact modifiers. Courtesy of SpecialChem.
Optical Properties
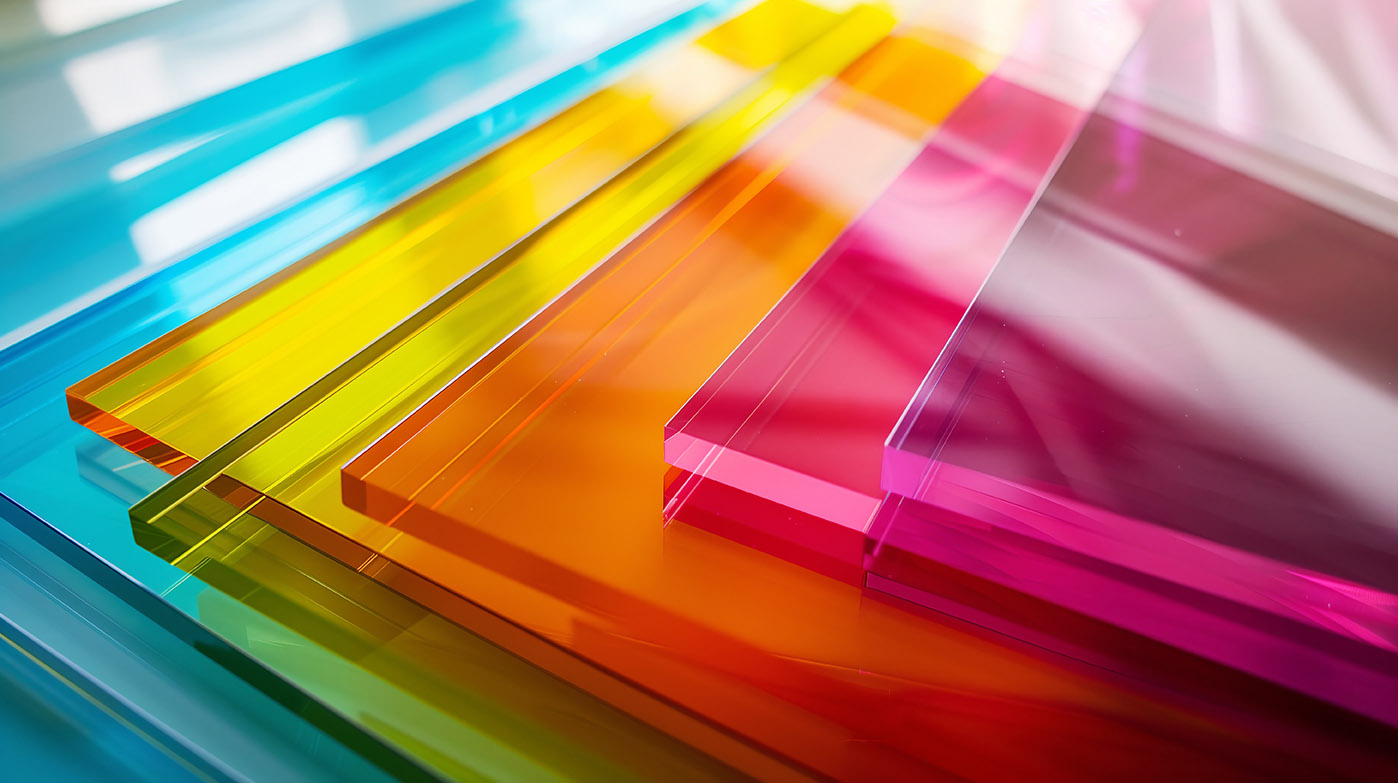
Polymer optical properties, such as gloss, transparency, clarity, haze, color, and refractive index, strongly influence perceptions of a plastic product’s quality.
Manufacturers often add nucleating agents and optical brighteners to products that require enhanced transparency or aesthetic appeal.
- Nucleating agents help control the crystallization process, improving clarity and a smoother surface.
- Optical brighteners enhance the whiteness or brightness of a product, giving it a more appealing look, especially in packaging materials.
Aging Resistance
Antioxidants, UV absorbers, and PVC stabilizers protect plastics from degradation caused by exposure to heat, light, or oxygen.
- UV absorbers, in particular, are essential for outdoor products like garden furniture or window frames, which need to withstand prolonged sunlight exposure without becoming brittle or discolored.
Surface Properties
Surface properties such as anti-static behavior and anti-fogging can be critical in certain applications.
- Anti-static agents prevent the build-up of static electricity, reducing dust and improving the appearance of products like packaging films.
- Anti-fog agents are helpful in food packaging to prevent moisture condensation, ensuring product visibility and freshness.
Reducing Costs
Manufacturers frequently use diluents and fillers to lower production costs without sacrificing plastic quality. These additives decrease the need for expensive base resin while preserving the desired mechanical properties.
- Fillers like calcium carbonate are often added to materials such as piping and packaging to increase bulk and reduce overall material costs.
Other Functional Additives for Plastic Modification
Additives such as blowing, coupling, and chemical crosslinking agents are used in more specialized applications.
- Blowing agents create a foam structure, making them ideal for insulation or cushioning applications.
- Coupling agents improve adhesion between different materials, enhancing the overall structural integrity of the product.
Selecting the suitable additives is critical for achieving optimal performance and cost-effectiveness in plastic modification. By understanding the role of each additive—whether to improve processability, enhance durability, or reduce costs—manufacturers can tailor their plastic products to meet specific needs while maintaining high quality and performance.