Energy Management Systems – Injection Molding II
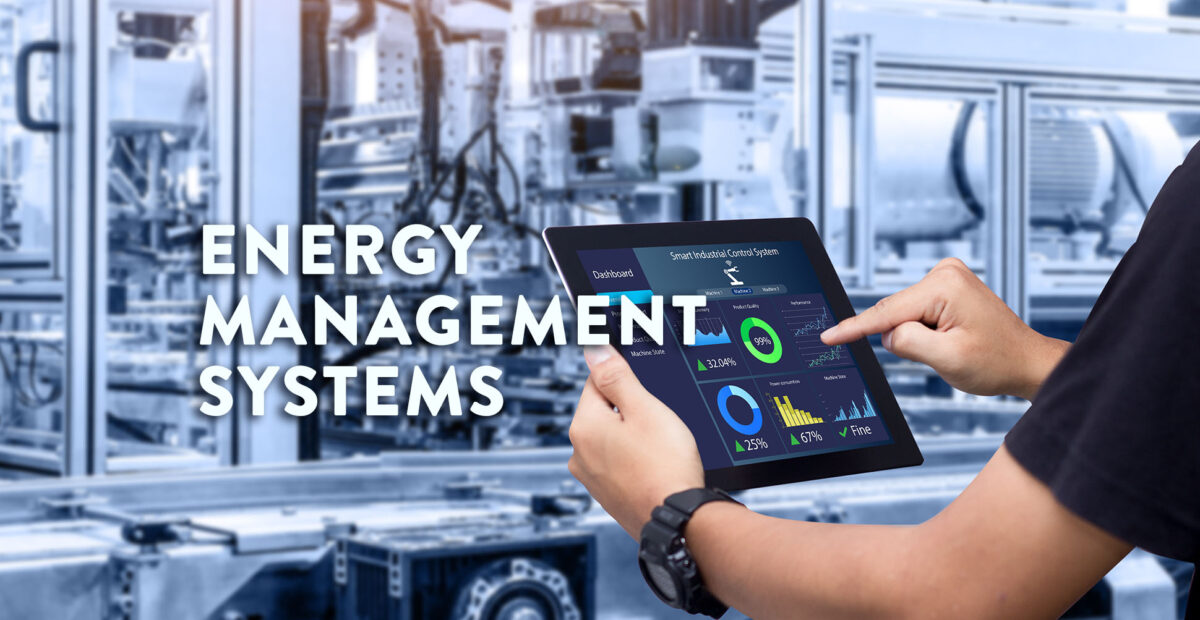
Simple process energy measurement and analysis quickly and easily shows that machine selection and operation can dramatically affect energy use and profitability of injection molding.
You can also read: Energy Management Systems – Injection Molding 1
Barrel heating efficiency can be improved by using insulation and by making sure there is good contact between heater bands and the barrel.
Action:
- Monitor machine energy use to identify changes in the machine condition, e.g., stopped, idling and running.
- Good maintenance can give significant energy savings. Look at areas such as temperature controllers, hydraulic valves, hydraulic oil viscosity and screw wear.
- Investigate process settings and look for areas where changes can be made. Look for areas such as barrel temperatures set too high, back pressure set too high, clamp force set too high, hold pressure too high, hold time too long, cooling time too long, screw-back too fast, etc.
- Heater bands should be ‘bedded-in’ by repeatedly tightening and loosening the heater band to get a good seating. Use a conductive metal compound between the heater band and the IMM barrel to maximize the heat transfer.
- Integrally insulated barrel heating bands reduce energy consumption used in heating by up to 17%, depending on the machine and application. Check the heater bands being used and calculate the costs/benefits of replacing these with insulated heater bands.
Learn more
Also read:
- Energy Management Systems – Injection Molding 1
- Energy Management Systems – The Gas Bill
- Energy Management Systems – Assessing Performance
- Energy Management Systems – Electricity Bill
- Energy Management Systems – Getting Started
- Energy Management Systems – Site Surveys
By Robin Kent | September 10, 2024