Choosing the Right Polypropylene Grade
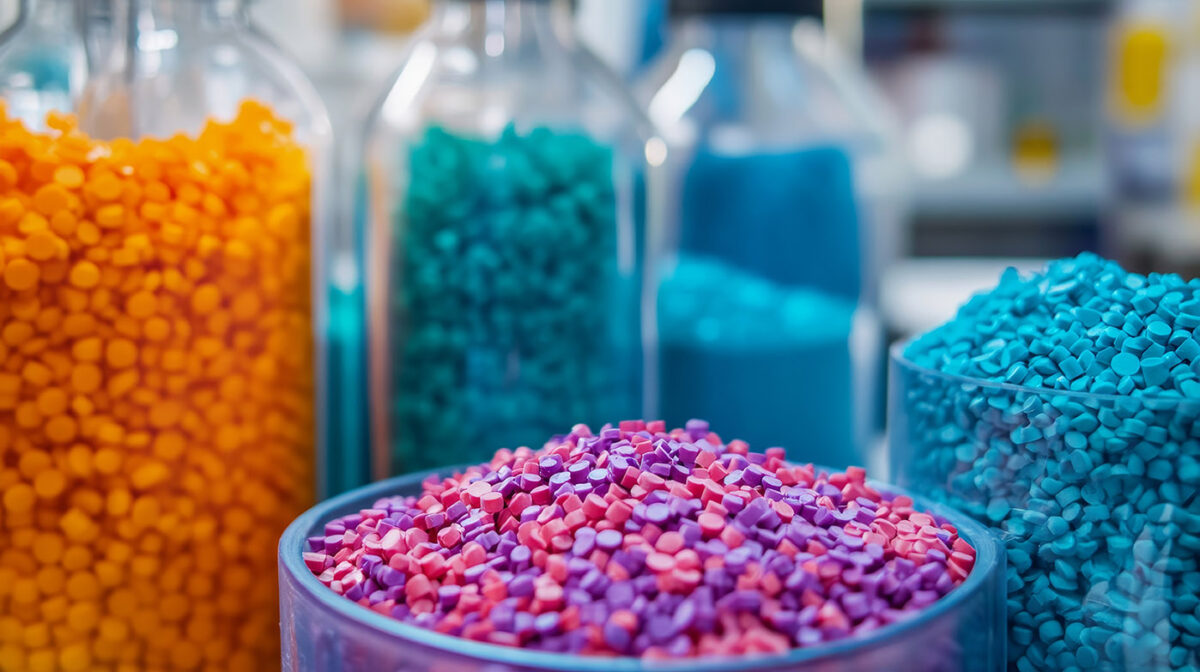
Selecting the right polypropylene grade for your project is crucial to ensuring optimal performance.
Polypropylene (PP) is one of the most versatile thermoplastics, with applications ranging from packaging and automotive parts to textiles and medical devices. However, choosing the appropriate polypropylene grade for your project is essential to achieving the best performance possible.
You can also read: Polypropylene Recycling from Disposable Face Masks
Types of Polypropylene (PP)
Polypropylene Homopolymer (PP Homopolymer)
PP Homopolymer is the most commonly used grade of polypropylene and is a semi-crystalline solid made entirely from propylene monomer. It is versatile and found in applications such as packaging, textiles, healthcare, automotive, pipes, and electrical components.
Polypropylene Copolymer
Polypropylene copolymers are produced by polymerizing propylene with ethylene and are classified into two main types: random copolymers and block copolymers.
- PP Random Copolymer: Polymerizing ethylene and propylene together forms this material, with ethylene units comprising about 6% of the mass. These ethylene units randomly integrate into the polypropylene chains, providing the material with flexibility and optical clarity. It is ideal for applications requiring transparency and an attractive appearance.
- PP Block Copolymer: has a higher ethylene content, typically between 5% and 15%. The co-monomer units are arranged in a regular block pattern, which makes the material tougher and less brittle compared to the random copolymer. This makes it well-suited for high-strength applications like industrial products.
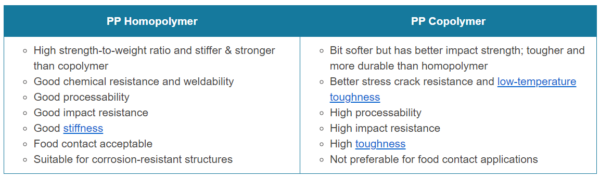
PP Homopolymer Vs PP Copolymer. Courtesy of Omnexus.
Understand Your Application Requirements
The first step is to identify the specific requirements of your application. Different polypropylene grades perform best in specific environments. For example, if a part requires high impact resistance, such as automotive components, impact copolymer PP is the ideal choice. On the other hand, homopolymer PP works better for applications that prioritize stiffness.
Consider Processing Methods
The manufacturing process also determines the best polypropylene grade to use. Injection molding applications typically favor homopolymer or random copolymer grades, which offer easy processability and good mechanical properties. Meanwhile, blow molding may require PP grades that provide better melt strength, especially in packaging applications.
Evaluate Mechanical Properties
Polypropylene comes in several grades that differ in strength, toughness, and flexibility. For applications that require rigidity and high-temperature resistance, a homopolymer grade is recommended. On the other hand, if flexibility or ductility is important, a random copolymer or block copolymer might be the best choice.

PP properties. Courtesy of Omnexus.
Environmental and Regulatory Considerations
Finally, it’s essential to factor in environmental concerns and regulatory requirements. If your product needs to be recyclable or meet FDA regulations for food contact, make sure the polypropylene grade you choose complies with these standards.
Selecting the right polypropylene grade involves understanding the application’s demands, processing techniques, and mechanical requirements. By carefully evaluating these factors, you can ensure the material meets both performance and regulatory standards.