Enhancing Manufacturing with Virtual Reality
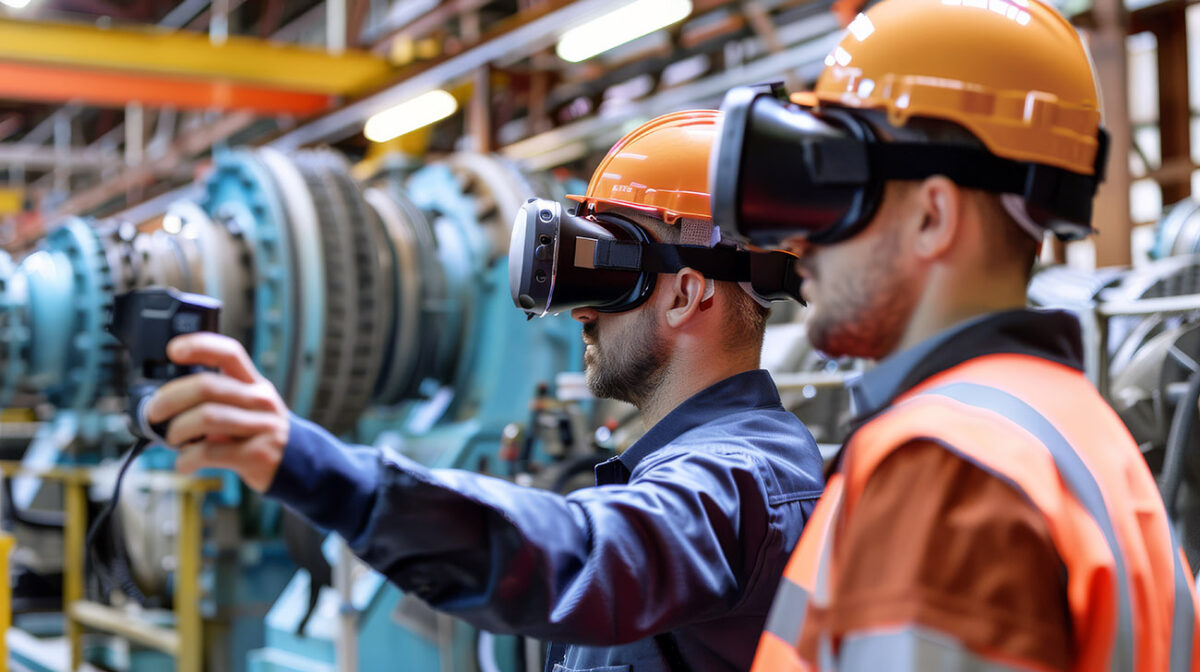
Virtual reality is revolutionizing the plastics industry, turning complex challenges into streamlined solutions from design to maintenance.
Virtual Reality (VR) has emerged as a transformative tool in Industry 4.0 for the plastics sector. By addressing traditional challenges, VR enhances efficiency and safety across production plants, revolutionizing operations from product design to equipment maintenance.
You can also read: AI-Driven Predictive Maintenance in the Plastics Industry
Overcoming Challenges with Innovation
VR’s potential in the plastics industry becomes particularly evident when we consider the complex processes, safety concerns, and training needs inherent to the sector. Traditional methods to address these issues can be costly and time-consuming. These technologies are a solution that creates interactive, three-dimensional environments that simulate real-world scenarios, making it easier to manage these challenges.
VR Benefits
Virtual reality offers several key benefits that directly address common issues in plastic plant production:
- Training and Simulation: VR provides immersive training programs that allow personnel to practice in a risk-free environment. These not only accelerate learning but also enhance safety.
- Design and Prototyping: Engineers leverage VR to visualize and modify product designs virtually. It accelerates the design process, reduces reliance on physical prototypes, and lowers associated costs.
- Process Optimization: VR simulations optimize production workflows and machinery layouts. It results in increased efficiency and reduced downtime.
- Maintenance and Troubleshooting: Integrating VR with IoT technology facilitates real-time monitoring and predictive maintenance, which helps minimize disruptions and improve equipment reliability.
Real-World Applications
Companies have successfully applied the benefits of VR in real-world settings:
- Arburg, the leading machinery manufacturer, has developed VR solutions to simulate the operation of its equipment. This allows clients to visualize how machines will perform in their facilities and provides effective staff training.
- BASF, the global chemical company, integrates VR into its product design and development processes. This allows engineers to visualize and adjust plastic compounds in a virtual space before production. It optimizes the development process and reduces time to market.
You can also read: Industry 4.0 in Injection Molding
Landscape of VR in Manufacturing
While the current applications of VR have already made a significant impact, the future of this technology in the plastics industry promises even greater advancements. As VR technology continues to advance, its integration with AI and AR will drive further innovation in manufacturing. VR is set to play a pivotal role in enhancing efficiency and fostering growth in the plastics industry. However, companies must address challenges such as high initial investment, technical limitations, and resistance to change to achieve broader adoption.