EPS Foam Adds Drama to Chocolate Store’s Ceiling
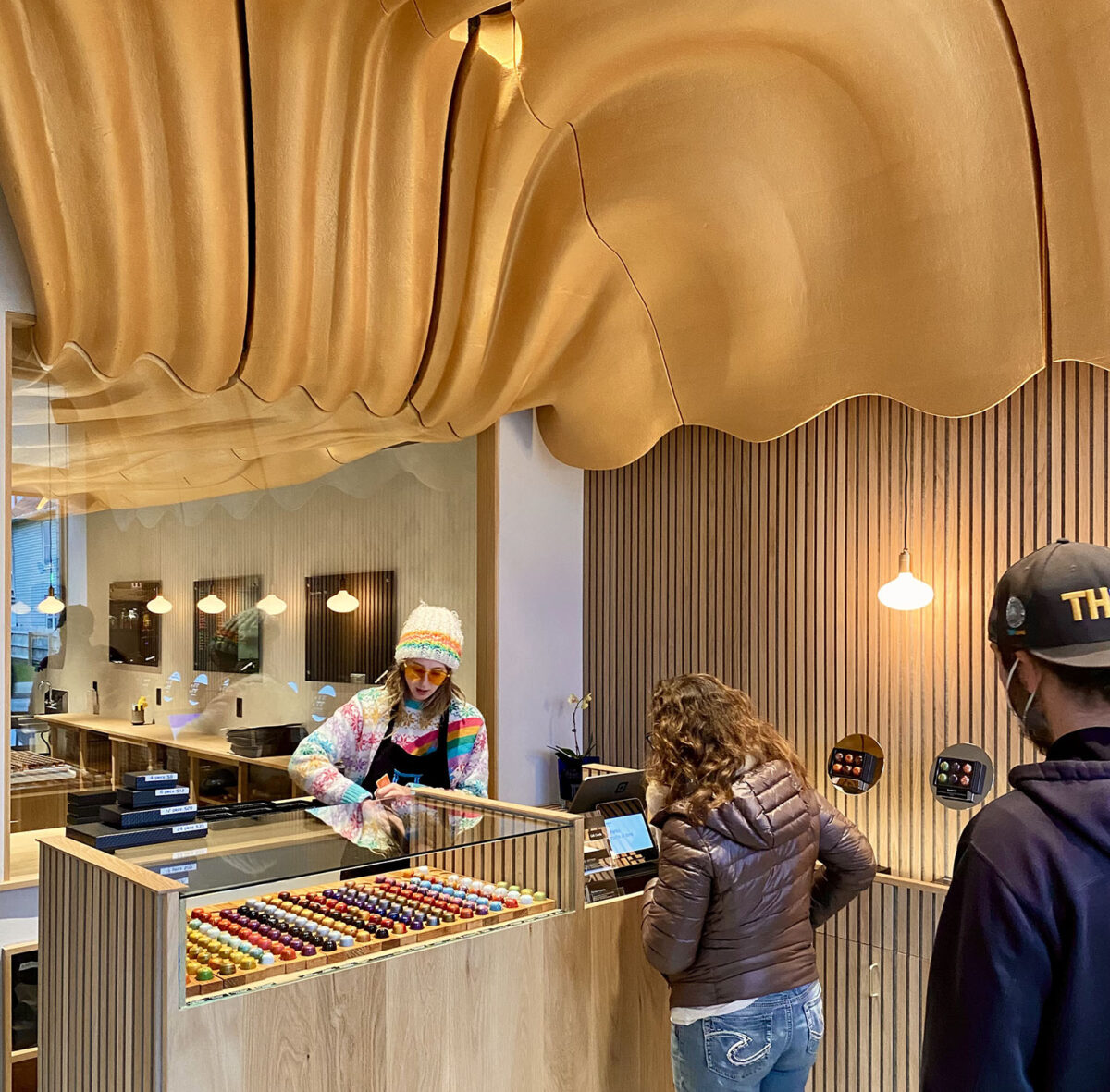
Inspired by molten chocolate, a Buffalo architectural firm gets creative to a stunning effect.
Inspired by a photo, architect Seth Amman sculpted and painted slabs of EPS foam to create a stunning ceiling in a boutique chocolate shop in Buffalo, N.Y.
Ben Johnson, owner of Blue Table Chocolates on Seneca Street, loved one particular image. The photo is an abstract shot of molten chocolate. He kept it on his phone and showed it one day to Amman, principal and founder of Arch&Type, whom Johnson wanted to help design his new retail space.
How did They do it?
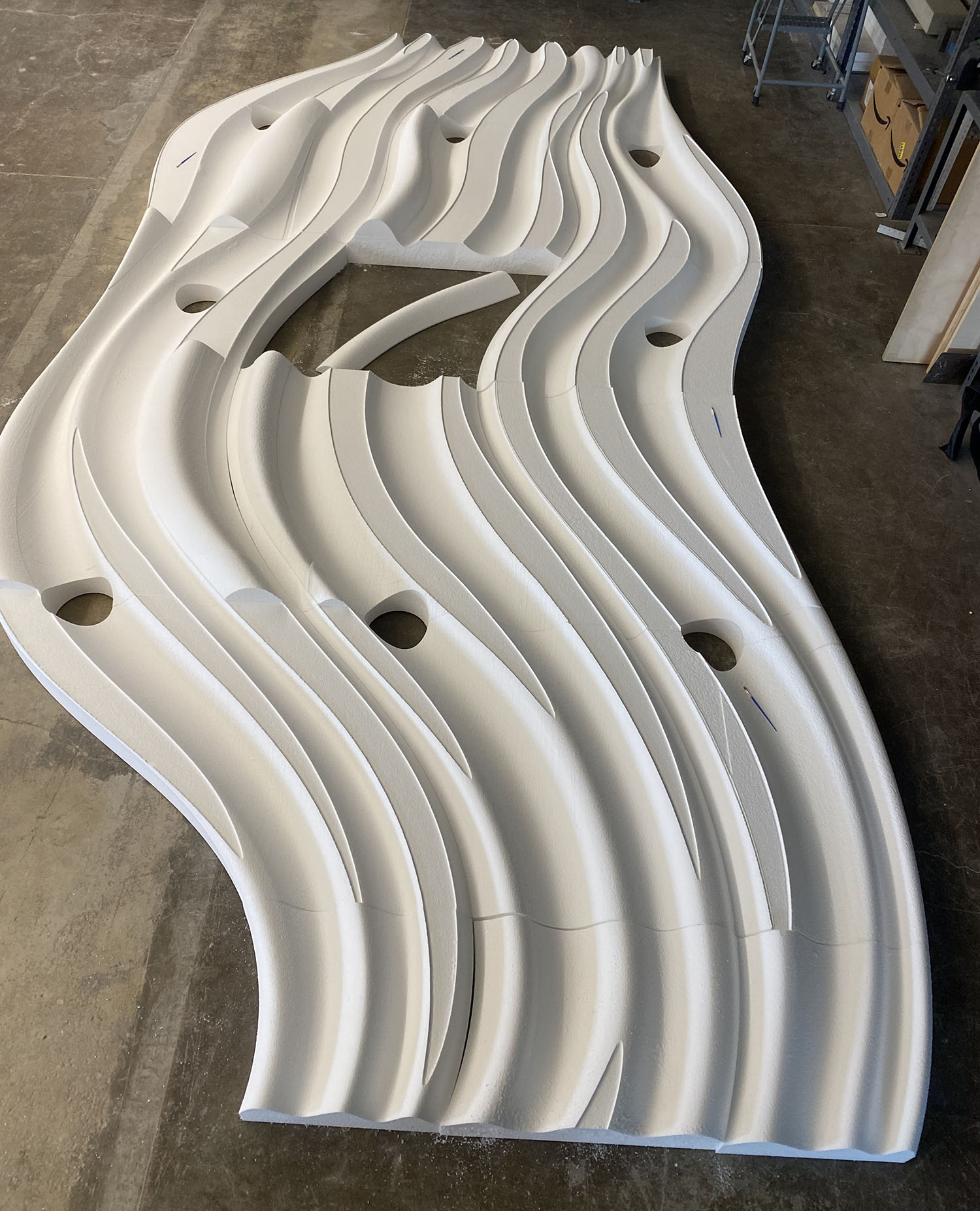
The team acquired 32 slabs of white EPS foam as the raw material for the project. They then glued some together and shaped them. The ceiling design involved milling intricate shapes. Courtesy of Arch&Type
Amman and designer Adam McCullough then devised a plan. While money and time were limited, Amman did have one key advantage. He has also been an adjunct professor at the University of Buffalo for five years. As such, he had access to the university’s digital fabrication lab space and contact with several talented students. Many of these students yearned for real-life experience. Seven of these individuals became interns on this project.
“Because chocolate has a crystalline structure inherent in it,” explained Ammon in a recent phone interview, “especially at a certain temperature, it was refracting the light, making the chocolate look golden, literally, like metallic golden. … We interpreted that photo and turned it into the ceiling.”
Tapping Into the SMART Lab
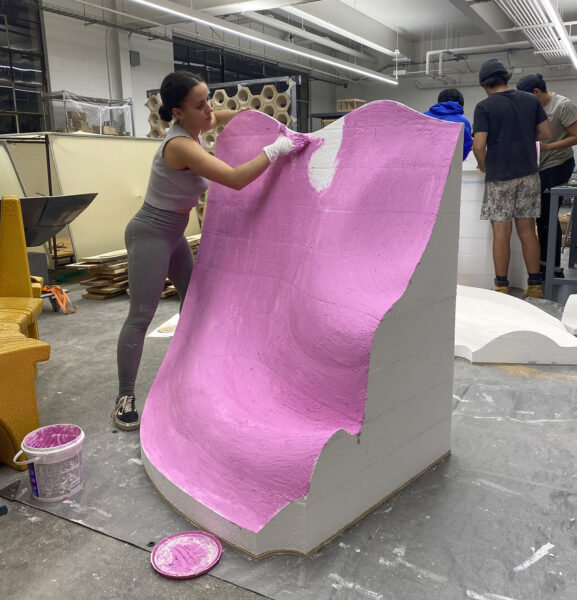
University of Buffalo students served as interns and helped with tasks such as applying to pink joint compound to the formed shapes. Once dry, the compounds turns white.
The university, which has a large architecture school, is also home to the Sustainable Manufacturing and Advanced Robotic Technologies (SMART) Lab, which Amman says has one of the largest material workshops in the nation.
In 2022 Johnson acquired new retail space for his chocolatier shop, growing to about 900 square feet from his previous 500 square feet. It was in a new building, with apartments above it. He knew Amman and sought his expertise in making the space special.
Arch&Type got to work. Using the golden image of molten chocolate as inspiration, they used expanded polystyrene (EPS) foam to create a flowing, curved ceiling. They ordered 32 slabs of 6-inch-thick, 4-foot by 8-foot foam. They had each piece milled and laminated with a 3M-brand industrial foam glue.
Leveraging Stacks of EPS Foam
To create the desired curvature in the ceiling, they CNC milled and stacked up to 10 or 12 of the EPS foam slabs on top of one another, to a height of more than five feet in some cases. For the thickest portions, they added a plywood base and drilled diagonal wooden dowels to help hold everything in place. They used metal Z-clip fasteners through the plywood to attach to the metal framework in the cavity above the ceiling.
Working in a warehouse bay at the university, Amman and the seven interns shaped and prepared the foam blocks.
“We roughly sanded down the foam, and then we coated it with a couple layers of spackling compound or, joint compound, just to give a kind of directionality to the texture. And then, after the drywall compound layers, we coated it in an intumescent paint layer.” Using this type of paint allowed the team to get a one-hour fire rating, which was the local requirement.
From a fire safety perspective, the project benefited from the new building also having sprinklers pre-installed in the ceiling cavities, and Amman’s team added sprinklers below the ceiling line as well. Together, these factors satisfied the local fire marshal.
From Pink to White to Gold
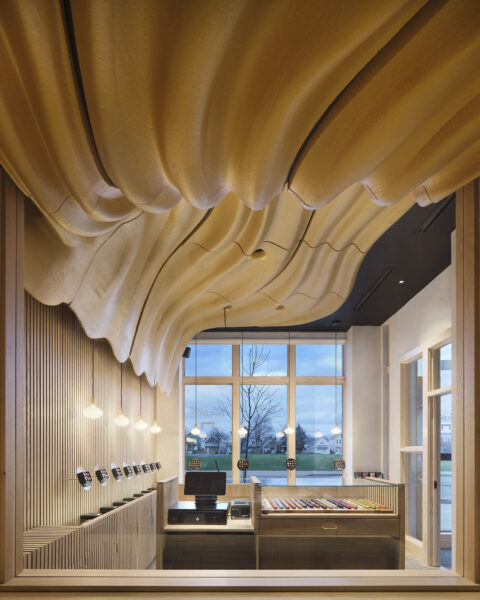
The team then sprayed the final foam shapes with a gold paint to create the dramatic end result.
The joint compound begins as a bright pink color when wet but then turns white to indicate when it’s dry. The students donned rubber gloves and carefully rubbed the pink compound all over the foam surfaces till they had built up a thickness of two millimeters or so. They also then hand-applied a couple layers of the thick, fire-resistant, intumescent paint.
Finally, they sprayed on the gold-colored finish coat. The resulting sculptural ceiling swoops, flows and includes embedded LED lights. Each of these can be dimmed individually to help create the desired ambiance.
The embedded LED downlights accent the hanging sculptural light bulbs and additional hidden, linear lighting in the shelves and the wood basins below the mirror. Amman calls the effect “light layering.”
At night, when no one’s in the shop working, Blue Table can keep the blinds open and keep particular lights on in the front showroom. “The dynamic ceiling essentially carries the brand or the idea of this delicacy of chocolate out onto the sidewalk or to the car driving by,” Amman said. “This glowing, atypical ceiling is undulating through the space and carries your eyes beyond.”
Winning Accolades
Ben Johnson is happy with the result. “Our company began as an online business without a brick-and-mortar location, while our last space, at all of 500 square feet, was designed with production in mind. When we began designing our new location with Seth it was time to create a retail space with character, that would stand out somehow.
“Seth and his team were able to pull that off through design and material choices in ways that weren’t just throwing money at the issue.” The store and its ceiling design have won several state and local architecture awards and have earned media attention nationally and abroad.
“Operating without much of an advertising budget for the last 11 years,” Johnson said, “the amount of exposure we’ve received simply for the dramatic ceiling design has been hugely helpful.”