AI-Driven Predictive Maintenance in the Plastics Industry
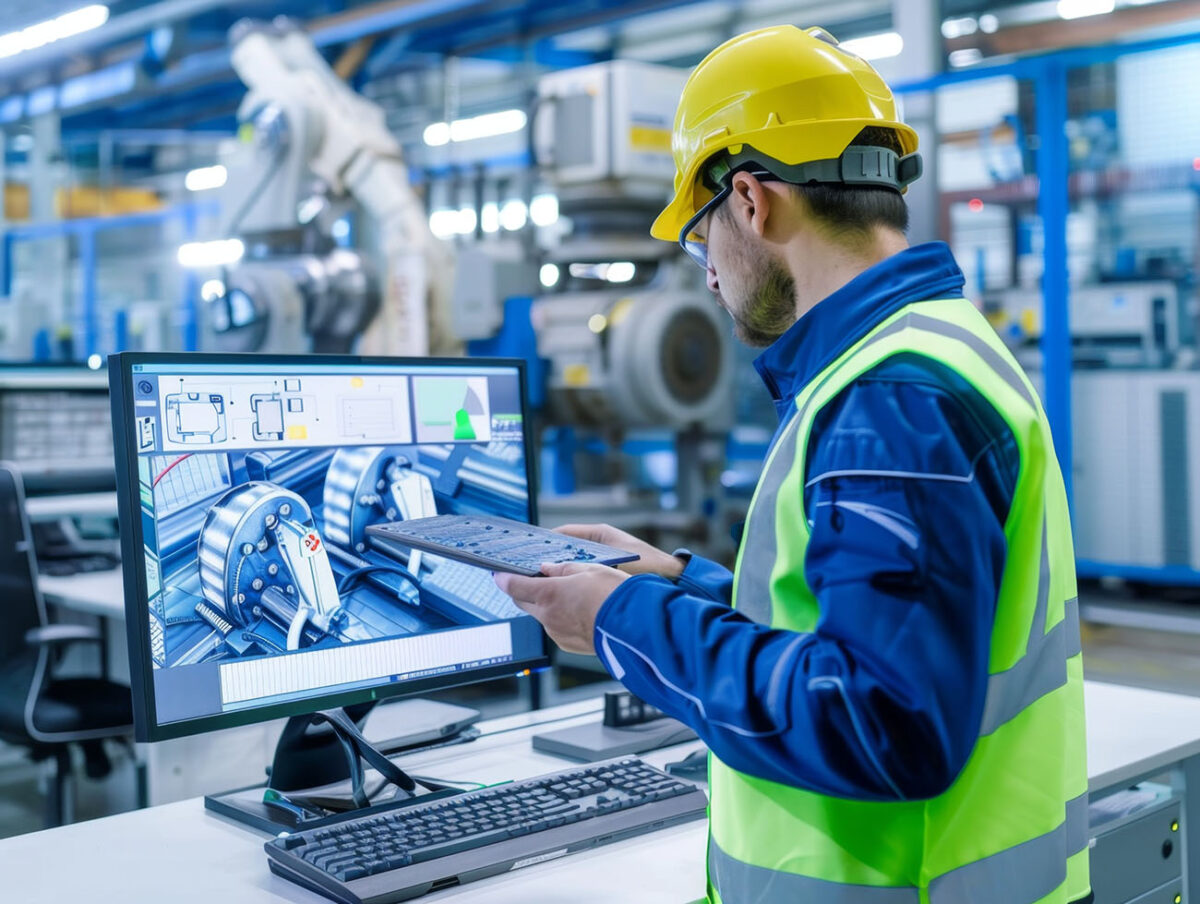
Artificial intelligence (AI) transforms the plastics industry through predictive maintenance, which uses data-driven insights to foresee equipment failures.
AI has emerged as a transformative tool for the plastics industry in today’s rapidly evolving technological landscape. As companies strive to maintain a competitive edge, AI offers innovative solutions to improve operational efficiency and product quality. One of the most promising applications of AI in the plastics industry is predictive maintenance. It is a proactive approach that leverages data-driven insights to foresee equipment failures before they occur. Plastic manufacturers can significantly reduce maintenance costs, optimize production processes, and enhance quality by implementing AI-driven predictive maintenance strategies.
You can also read: AI Mastery: Scaling from Research to Serial Application
AI and IoT Integration
AI-driven predictive maintenance in the plastics industry combines hardware and software components to effectively monitor and analyze equipment data. The hardware includes IoT devices that collect real-time data from manufacturing equipment. Moreover, these devices capture essential parameters like temperature values, vibration levels, pressure measurements, flow rates, and motor current consumption. AI systems analyze this data on the software side to identify patterns and anomalies that could indicate potential equipment issues. By leveraging machine learning algorithms and advanced analytics, these AI systems can predict equipment failures before they occur. It allows maintenance teams to take proactive measures. This integration of IoT and AI reduces unplanned downtime and enhances equipment lifespan and efficiency, leading to significant cost savings and improved production quality.
AI-Driven Advantages and Key Players
AI and IoT offer numerous advantages. These include minimizing downtime, enhancing production efficiency, optimizing maintenance costs, improving safety, and boosting product quality. As a result, many companies are investing in these technologies. Some of the key players in the plastics industry that have embraced AI for predictive maintenance include:
- SABIC: The Saudi Basic Industries Corporation uses AI technologies to enhance operational efficiency and reduce maintenance costs. Their AI systems analyze data from sensors and equipment to predict potential failures.
- INEOS: This global manufacturer of petrochemicals and plastics uses AI technologies to monitor their equipment in real time. It predicts maintenance needs and reduces downtime.
Challenges in AI Implementation
As the plastics industry adapts to new challenges, integrating AI and IoT for predictive maintenance becomes crucial. This advancement drives sustainable growth and operational excellence. However, successful implementation requires careful consideration of challenges like data management, integration complexity, and cybersecurity. Addressing these challenges head-on is essential for maximizing the benefits of AI-driven predictive maintenance.