PET Thermoforms- A New Landscape for PET Recycling
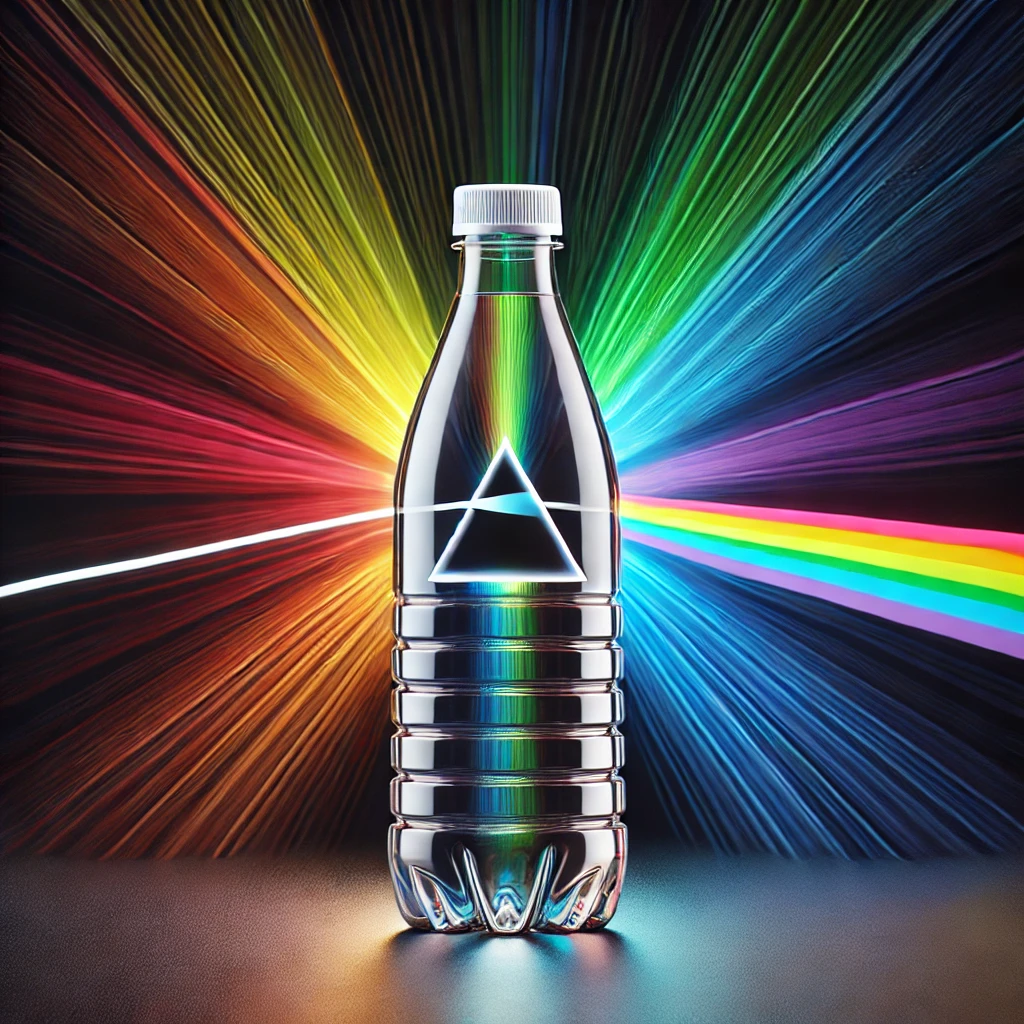
Recycling PET bottles has set a standard for other industries, but PET thermoforms are still gaining momentum. This industry segment is paving the way for a new landscape in PET recycling.
So goes California, and so goes the country. At least, that is what they say (sometimes) in the United States. In terms of polyethylene terephthalate (PET) recycling, there is plenty of evidence that this adage is true. The state has just enacted the country’s most aggressive legislation regarding PET recycling. California is the first U.S. state to require beverage containers to use a set amount of recycled plastic: 15 percent in 2022, then increasing to 50 percent by 2030. This could set an example for other states, though the economics must justify investment in other locations. PET bottles are a known entity with a proven track record in recovery and recycling, but PET thermoforms are another species. A slate of speakers assembled by the Singapore-based Centre for Management Technology addressed this topic on November 10 at a half-day webinar titled “Americas Thermoform Recycling and Food Contact Recycled Packaging.”
You can also read: Golden Design Rules for PET Thermoformed Packaging
PET Trends
Laura Stewart, communications director for the National Association for PET Container Resources (NAPCOR), presented updated statistics and details of the current landscape for PET thermoform recycling in the United States. In 2009, NAPCOR identified a gap in the market whereby PET thermoform containers were not being collected for recycling. At the time, NAPCOR estimated approximately 1bn lbs of PET thermoforms were available, yet in 2011, only 45MM lbs were recycled. In 2018, over 1.8bn lbs of PET was recovered, 41 percent of which was plastic fiber.
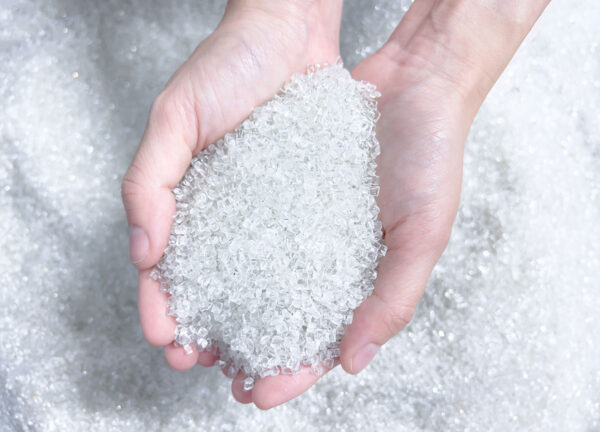
California Strawberry Commission and Driscoll’s are committed to using PET thermoforms as supplemental feedstock for PCR.
Though the challenges are real, Stewart likened today’s environment to the early 1980s when the recycling industry was learning to cope with PET bottles. Those old enough to remember those two-liter bottles will recall the mixed materials, including a base caps on the bottom and metal caps on top. With an increasing number of brands promising to increase their use of PCR, demand-side economics are pointing to an eventual shortfall in rPET. It is posited that PCR thermoforms could help to address this, yet the applications must be aligned and suitable. Helpfully, the California Strawberry Commission and Driscoll’s are committed to using PET thermoforms as supplemental feedstock. The California mandates are inspiring California-led solutions with major investments in clamshell-to-sheet operations. Companies like CarbonLite and rPlanet Earth are well-known industry success stories, with others providing critical supply chain support.
You can also read: Anticipating Challenges as Demand for Recycled PET Increases
Building the Ecosystem for PET Thermoform Recycling
Octavio Victal, CEO and founder of Green Impact Plastics in Juarez, Mexico, started his company in direct response to the PET thermoform recycling challenge, he explained during his presentation. With 1.6bn lbs of PET thermoforms being landfilled, a tremendous opportunity is literally going to waste. To emphasize the financial opportunity, Victal stressed that market demand can and will set an attractive price for reclaimed thermoform flake, especially when you consider the current rate of $0.40/lb for bottle flake.
Green Impact Plastics has identified a business opportunity through an understanding of PET material properties, cutting-edge sorting technology, and incipient market demand. With an initial capacity of 20MM lbs/yr, Green Impact’s new facility is designed to process bales of 100 percent thermoforms. They processed 1.9MM lbs in 2019 and 4.8MM lbs so far in 2020. While clearly not at capacity yet, the company is nonetheless establishing a second facility in Vernon, Calif.
PET Sorting Technologies
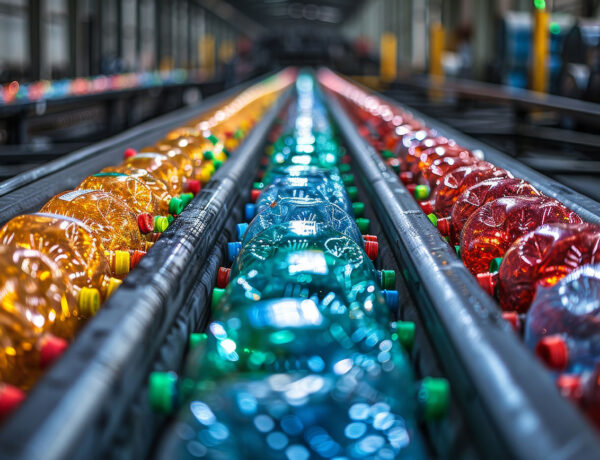
Tomra has introduced a “flying beam” sensor that detects molecular differences to differentiate between PET bottles and thermoforms.
Tomra, a Norway-based collection and sorting technology specialist, has been a key partner for Green Impact. Carlos Atienza, Tomra’s Regional Director for the Americas, presented technical details on PET sorting. Through their new autosort equipment, Tomra has added a “flying beam” sensor that analyzes molecular differences to distinguish between PET bottles and thermoforms. Tomra states their near-infrared (NIR) scan system provides sharper focus than previous iterations. Moreover, their new “Sharp Eye” technology adds a bigger lens for greater light intensity, detecting hidden properties.
Meanwhile, Green Impact is building relationships and raising funds to expand facilities. The City of Los Angeles is the single largest waste generator in the United States. Additionally, the entire state of California discards 240MM lbs of PET thermoforms per year. Despite its reputation for not being the most business-friendly state, California appears well-positioned to see increased investments in thermoform recycling.
You can also read: Enhancing Plastic Sorting Through Deep Learning
Recycle-Ready Clamshells
In the late 1860s, farmers in California’s Parajo Valley grew the first commercial strawberries. By the 1940s, that exceptional part of the world was a hub of fruit growers and agricultural experts, researching and developing techniques to breed new varietals of strawberries. Driscoll’s was growing and shipping California strawberries across the country by 1950. Today, the company is at the vanguard of a new commitment to use ‘recycle-ready’ PET clamshells by 2025. What this means in practice is reducing the barriers to collection, separation, and re-processing of PET berry baskets. Camille Herrera, packaging development and sustainability manager, explained the company’s strategy during another session. Specifically, by switching from traditional paper labels and adhesives to biaxially-oriented polypropylene (BOPP) labels with water-soluble adhesives, reclaimers can float/sink PP and PET to effectively separate materials. This approach has been codified in the Association of Plastics Recyclers (APR) Design Guides.
Consumer Behaviour as a Driver
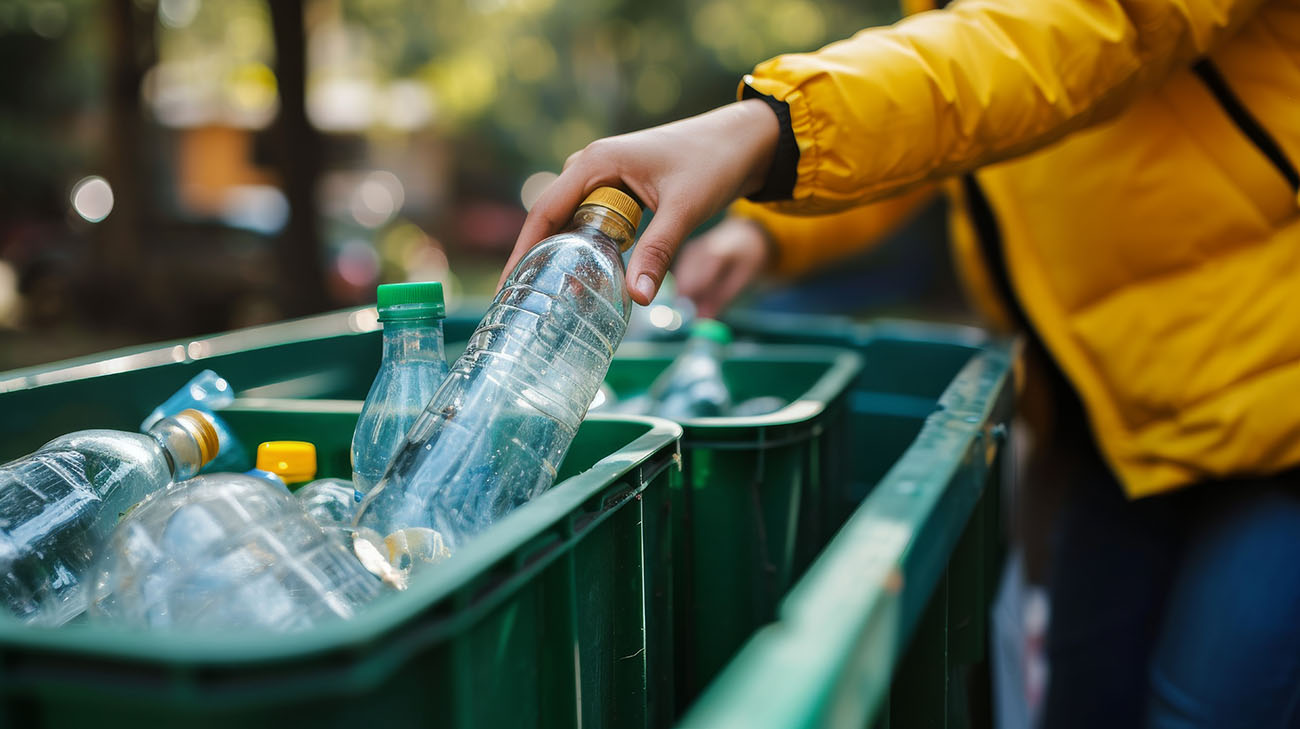
Environmentally conscious consumers are driving brand owners to adopt alternative solutions.
Many sustainability managers attest that consumer behavior heavily influences recycling. Outreach and education are key elements in changing behavior, and the How2Recycle logo program accelerates this shift. By clearly stating that PET clamshells can be properly discarded, reclaimers can more successfully recover clean material. On the demand side, Driscoll’s has also committed to using 10 percent recycled content from recovered clamshells by January 2021. They are doing this through a “Thermoform Clean Wash Flake” (TCWF) initiative that includes mass balance accounting and monthly check-ins with suppliers. Future work will include evaluation of pads and glues (used in some berry baskets), digital watermarking, and continued collaboration with the larger berry industry.
You can also read: Golden Design Rules: Enhancing PET Recycling Through Design
The Fine Print
Food Safety First
Testing for FDA Approval
The FDA prominently features contaminant testing in its rules because people often reuse plastic containers for unintended purposes. For example, they might store automotive chemicals, pesticides, or paints in these containers before they enter the recycling stream. Consequently, the FDA provides specific recommendations focused on removing contaminants based on testing that simulates consumer behavior. This testing deliberately exposes plastics to contamination. Additionally, some packages, such as berry baskets or egg containers, represent very low migration risk as they protect “dry goods.” Therefore, for processors seeking to enter the recycling market, identifying these sources of material will reduce the regulatory process for contamination testing.
Beyond PET: Sorting Technologies for PP
Although billed as PET-centric, the event’s final speaker, Dr. Edward Kosior, focused on polypropylene technology. Dr. Kosior has pioneered NIR technology using fluorescent light markers to detect black plastics in the recycling stream. The PRISM sorting system used a consortium approach over six years with academic and industry groups for high-speed material separation.
Now, Kosior is launching a new consortium called Nextloopp to apply PRISM technology to polypropylene (PP), with low recycling rates. With projected virgin growth of 50 percent over the next five years, available PP for recycling seems limitless. Given the heavy use of PP in household chemical products, separating food from non-food containers is critical. Because PRISM can distinguish between food and non-food containers, unlocking a stream for food-contact PP applications is possible. Currently, only PP food packaging can be used for future rPP food applications in the European Union. Complementing PRISM, Nextek’s PPristine decontamination technology will enable a clean stream of rPP.
PET Regulation and Future Opportunities
Incentives can be either carrots or sticks. As stated at the outset, California recently enacted AB793, which establishes minimum recycled content requirements for plastic (PET) beverage containers.
In the case of new market opportunities, first movers must weigh risk and reward, raise capital, and take the plunge. When regulations and market opportunities align, the likelihood of a profitable outcome increases. In California, a 21st-century “plastics rush” seems to be underway.
You can also read: Redefining Recycling: Depolymerization of PET
Originally published as A New Landscape for PET in Plastics Engineering Magazine issue Nov-Dec 2020. Edited for online by Juliana Montoya.