Biomethanol-Based Silicone Rubber – A Future Perspective
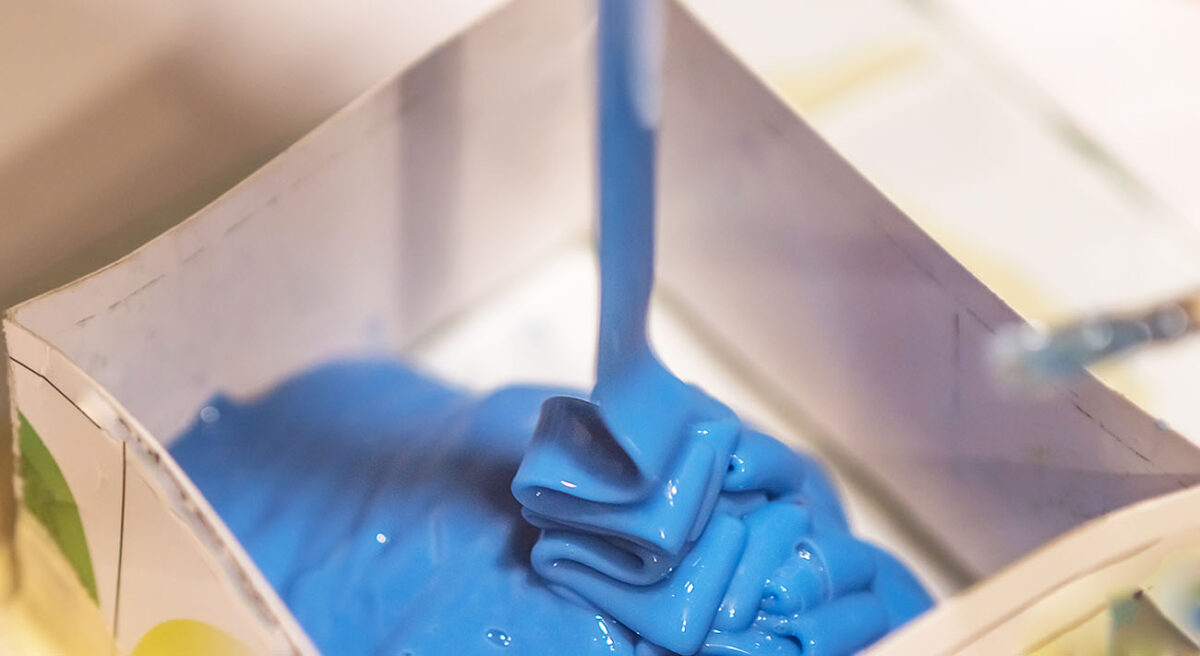
The German company WACKER has adopted the mass balance approach, which enables the simultaneous processing of fossil-based and renewable raw materials to produce silicone rubber.
Since 2018, WACKER has integrated biomethanol, a plant-based methyl alcohol generated from petrochemical and plant-based resources, into its production process. This bioethanol is mass-balanced, guaranteeing that the quantity of eco-products sold corresponds to the amount of bioethanol used.
You can also read: Bio-Based Plasticizers: a Sustainable Approach to Enhance PLA Performance
This method is certified by TÜV Nord under the standard and ensures that products labeled as “bio-based” are genuinely derived from renewable resources, supporting sustainability goals.
WACKER’s eco portfolio includes various biomethanol-based silicone products, from silicone fluids and defoaming agents to fabric softeners and silicone sealants.
See also: Advances in Silicone Technology for – 4spe.org
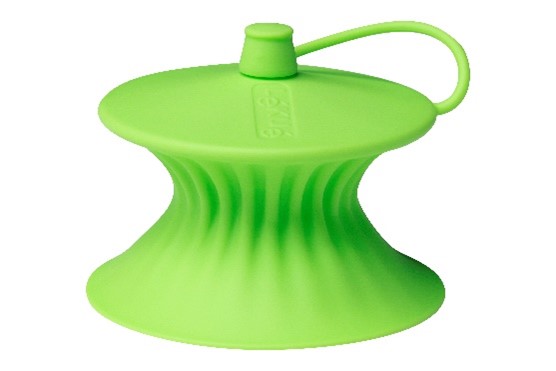
Lemon press made from SILMIX® eco R plus TS 40002, a food-grade silicone rubber derived from biomethanol. Courtesy of WACKER.
Mass Balance Approach in Silicone Manufacturing
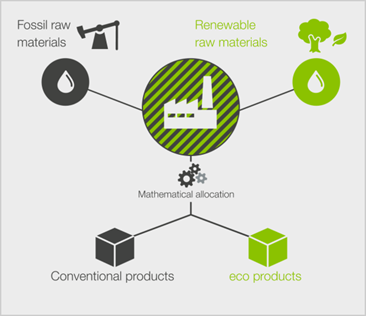
Manufacturers use a combination of fossil and renewable feedstocks within the same system to produce products. Courtesy of WACKER.
In silicone manufacturing, the integration of a mass balance approach is crucial for enhancing sustainability and minimizing environmental impact. The principal elements in this process are silicon and methanol, which serve as critical raw materials.
Initially, methanol undergoes conversion to methyl chloride, which subsequently reacts with elemental silicon through the Müller-Rochow process. This reaction yields various methylchlorosilanes, which are fundamental to further production stages.
However, the application of the mass balance approach extends beyond these initial production stages. This method incorporates finished silicone products by balancing pigments and other organic additives with equivalent amounts of biomethanol.
Mass balance approach ensures the entire production process maintains an eco-friendly footprint, meeting modern demands for sustainable industrial practices. By adopting this method, silicone manufacturers can achieve a comprehensive environmental strategy.
This technique not only boosts the sustainability of silicone production but also fosters a circular economy within the industry by prioritizing renewable resources and minimizing waste generation.
See also: Shell’s Recycling Plans for the Future and What to Implement Now
Future Perspective: Biomethanol-Based Silicone
The transition to biomethanol-based silicones is seamless due to the chemical identity between methanol and biomethanol, ensuring no changes in product properties or processing techniques. This enables manufacturers to adopt eco-friendly options without extensive testing or modifications, promoting easier and faster integration of sustainable practices.
Future developments are likely to expand the range of biomethanol-based silicone products. WACKER has already introduced various eco-grade silicones under the ELASTOSIL eco portfolio, including tear-resistant liquid silicone rubber and multipurpose solid silicone rubber grades. The potential to convert other products to biomethanol-based versions upon request highlights the flexibility and scalability of this approach.
The chemical industry’s commitment to reducing fossil raw material usage through innovative strategies like the mass balance approach is driving considerable progress in sustainable manufacturing. Furthermore, integrating biomethanol into existing production lines may involve initial costs and logistical adjustments.
Manufacturers need to ensure robust supply chains and maintain the quality and consistency of biomethanol to avoid production disruptions. Overcoming these challenges requires collaboration across the industry, investment in research and development, and supportive regulatory frameworks that encourage the use of renewable resources.