AFLatex Technologies Transforms Natural Rubber Latex Preservation
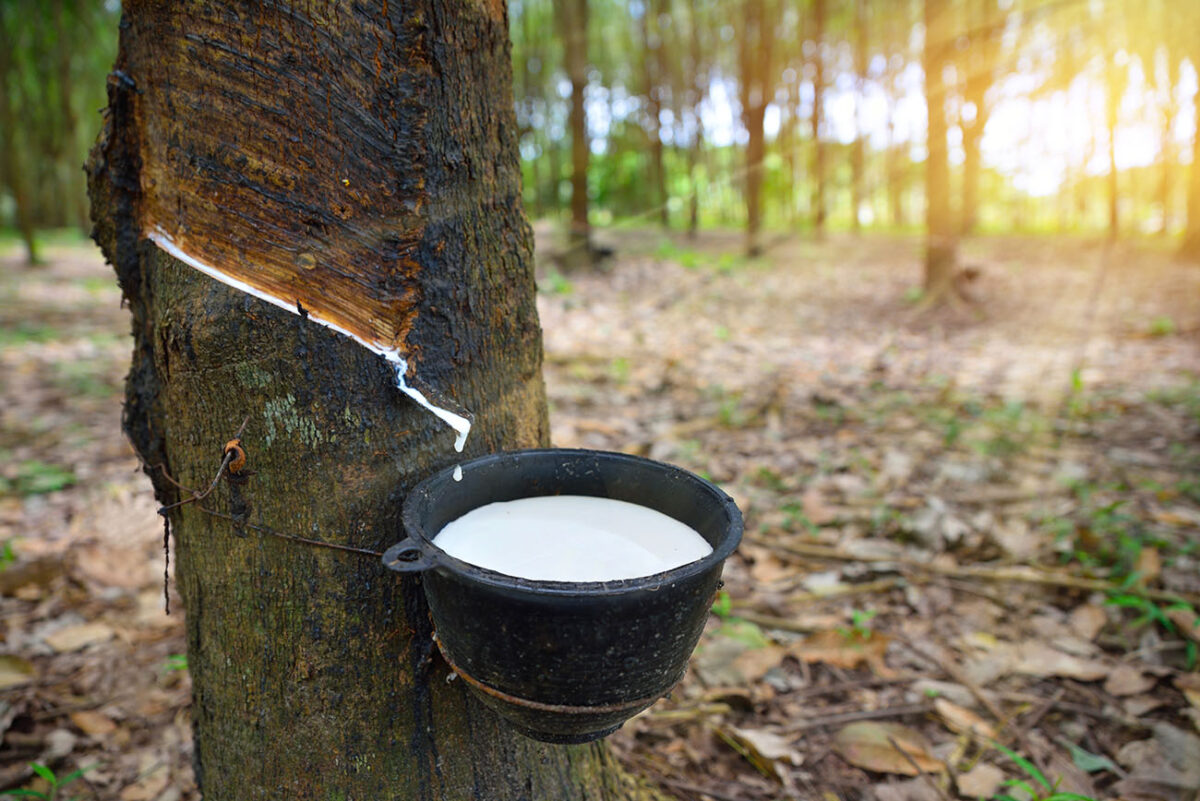
AFLatex Technologies revolutionizes natural rubber latex preservation with eco-friendly methods, reducing reliance on harmful chemicals.
Natural rubber latex (NRL) is an essential material used in various industries for its unique properties. However, NRL faces significant challenges in preservation and stabilization, primarily due to microbial degradation and coagulation. Traditional methods of addressing these problems are often based on harmful chemicals, posing risks to human health and the environment. Several researchers are investigating environmentally safe methods to preserve and stabilize NRL to address these challenges. As a result, AFLatex Technologies has emerged as a promising solution.
You can also read: Understanding Thermoplastic Elastomers: Versatile and Recyclable
NRL Benefits and Challenges
NRL, derived from rubber tree sap, is known for its exceptional elasticity, tensile strength, and abrasion resistance. It is extensively used in the medical industry, the automotive sector, and for consumer goods. Nevertheless, preserving and stabilizing NRL is challenging due to microbial degradation, leading to spoilage and material loss. Premature coagulation during storage complicates matters, making it unusable. Traditional methods use chemicals like ammonia and thiurams, which are effective but risky due to toxicity and pollution potential.
New Proposals for NRL Sustainability and Quality
AFLatex technologies represent a significant advancement in the preservation and stabilization of NRL through environmentally friendly approaches. These technologies aim to reduce reliance on harmful chemicals while maintaining the quality and usability of NRL.
Researchers at AFLATEX Technologies developed two novel liquid latex preservation methods without ammonia or harmful chemicals. One method uses dodecyl benzene sulfonic acid for stabilization and preservation. The other employs ethoxylated tridecyl alcohol for stabilization and hydrofluoric acid for preservation. Both formulations enhance rubber’s mechanical properties, ensuring worker safety and environmental friendliness.
AFLatex’s Innovations
In practical applications, AFLatex offers eco-friendly adhesives with varying rubber content for domestic (35%) and industrial (60%) use. Their latex formulation with high dry rubber content has also transformed glove manufacturing, ensured superior performance, and reduced allergenic protein content to 45%.
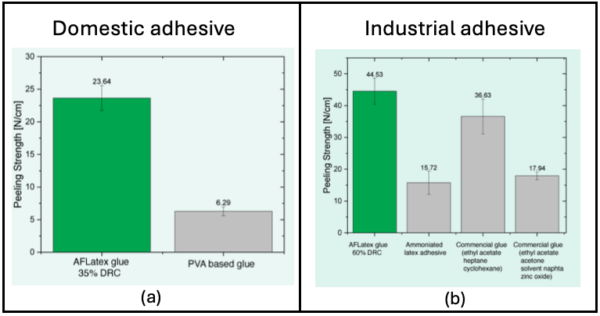
The peel strengths of AFLatex Office and Home Glue and AFLatex Industrial Adhesive were compared with commercial counterparts. (a) AFLatex Office and Home Glue showed significantly higher peel strength compared to polyvinyl acetate glue (6.29 N/cm). (b) AFLatex Industrial Adhesive outperformed ammoniated natural rubber cement, ethyl acetate, and solvent-based leather adhesives, highlighting its superior performance and solvent-free formulation. Courtesy of AFLatex Technologies.
Furthermore, AFLatex innovates by transforming solid natural rubber into foam, showcasing NRL’s versatility in various industries. These advances expand NRL’s applications and promote safer, more sustainable rubber production and use.
Moving forward, continued research and development in NRL preservation methods are crucial for mitigating environmental impact and enhancing health standards. By fostering innovation and collaboration, AFLatex and similar technologies can lead the way in achieving sustainable NRL solutions.