Affordable Metal-Additive Manufacturing for the Plastics Industry
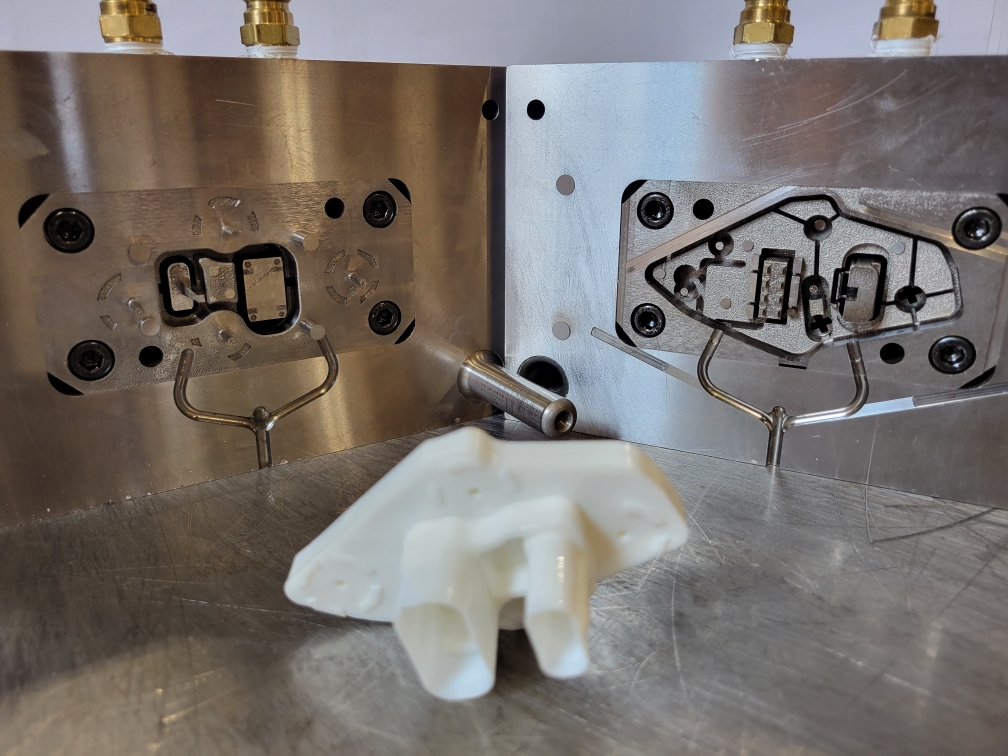
Xact Metal spoke to Plastics Engineering at NPE 2024 about how the company is transforming the metal additive manufacturing landscape by making it more accessible and affordable.
The company identified a gap in the industry, where high costs often hinder the adoption of metal 3D printing technology, especially in the plastics industry. By using the same high-quality lasers as their expensive counterparts but focusing on design costs and building the machines in-house, Xact Metal can significantly reduce costs. This approach democratizes access to metal additive manufacturing, making it feasible for more mold shops to integrate this advanced technology.
You can also read: The Impact of 3D Printing on Mold Making
Innovative Materials and Exclusive Partnerships
A key innovation from Xact Metal is introducing the Corrax material from Uddeholm. This material resembles low 300 series stainless steel in corrosion resistance while being more malleable than 420 stainless steel. The unique properties of Corrax make it ideal for various applications in the molding industry. Xact Metal’s exclusive global partnership with Uddeholm ensures that Corrax is available in additive form. This partnership enhances the material’s availability and underscores Xact Metal’s commitment to providing cutting-edge solutions to their customers.
Impact on Mold Manufacturing Efficiency
3D printing technology has proven to be a game-changer in mold manufacturing, offering substantial efficiency improvements. Xact Metal’s case studies highlight how 3D printing can dramatically reduce cycle times and save costs. For instance, a 20-year-old tool with worn-out cores saw a cycle time reduction from 20 seconds to 18 seconds after being equipped with 3D-printed conformal cooling inserts. Although a 10% reduction might seem modest, it translates into significant savings when the tool operates 24/7 throughout the year. Moreover, lightweight mold inserts with conformal cooling cut costs and have a positive environmental impact by reducing energy consumption.
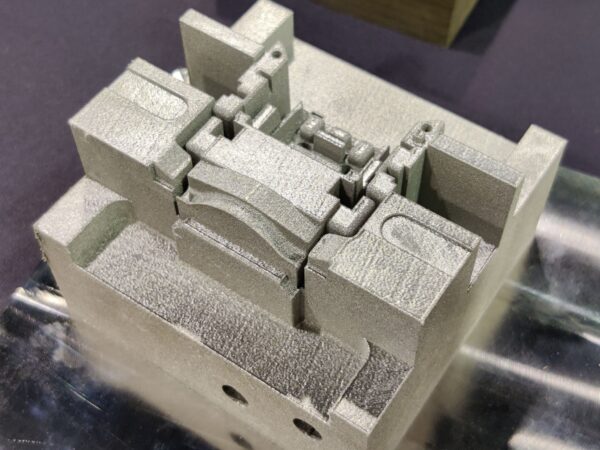
Xact Metal tooling insert. Courtesy of Xact Metal.
Adoption and Potential of 3D Printing in the Plastics Industry
The plastics industry gradually recognizes and adopts 3D printing technology, especially in mold making. Xact Metal emphasizes the need for sophisticated software to analyze and optimize designs. As the industry becomes more familiar with 3D printing’s capabilities, mold makers see it as an essential tool rather than a novelty. This shift is crucial for the widespread adoption of 3D printing, which promises to revolutionize traditional manufacturing methods.
“It’s a big educational issue for us. There must be a process in which professionals understand the additive manufacturing logic to design parts and see it as a functional process, not just prototyping,” said Juan Mario Gomez, Chief Executive Officer at Xact Metal.
Engineering Performance and Productivity
Engineering performance and productivity are crucial in the tooling industry. Xact Metal’s technology excels in producing precise 3D geometries that meet stringent engineering requirements. The company highlights the importance of not compromising quality while striving for productivity gains. By leveraging their technology, Xact Metal enables mold makers to achieve high performance and efficiency in their operations. This approach ensures that the industry can maintain high standards while benefiting from the advancements in 3D printing technology.
“We realized there’s a gap in the industry to make metal additive manufacturing more affordable but still get value out of the performance. We build all the machines in-house. So, therefore, we get better-captured processing, which allows us to reduce our prices,” said Scott Kramer, Senior Application Engineer at Xact Metal.
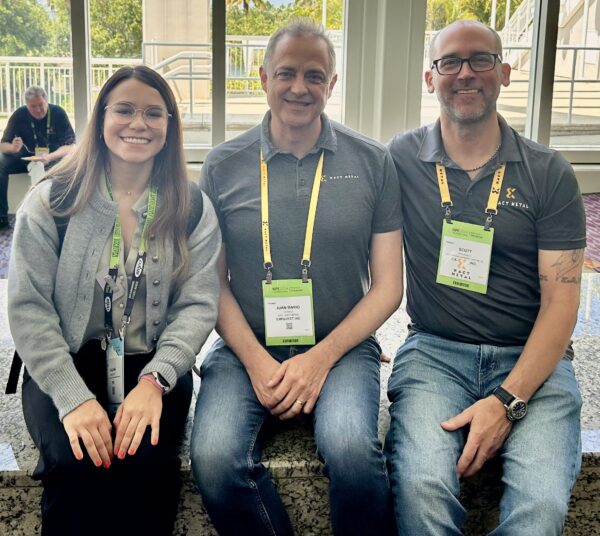
Juliana Montoya, Director of Content at Plastics Engineering; Juan Mario Gomez, CEO at Xact Metal; Scott Kramer, Senior Application Engineer at Xact Metal.
Case Studies and Applications
Xact Metal’s case studies showcase the practical benefits of their technology. JST Tooling, for example, saved $34,000 by using 3D printing to create a prototyping tool, significantly reducing lead time. The ability to produce parts quickly and affordably highlights the transformative potential of 3D printing. These success stories demonstrate that 3D printing is not just for prototyping but also for full-scale production. The technology’s versatility allows it to be used across various applications, from tooling to fixtures and jigs, making it a valuable asset for manufacturers.
Future Prospects and Industry Impact
The future of the tooling industry looks promising with the integration of 3D printing technology. Xact Metal’s affordable solutions make it easier for companies to adopt this technology and reap its benefits. Younger generations, familiar with 3D printing from their educational experiences, will likely drive further innovation and adoption in the industry. As more companies recognize the value of 3D printing, it will become a standard tool in the manufacturing toolbox, complementing traditional methods and opening new possibilities for efficiency and innovation.