The Complexity of Recyclate
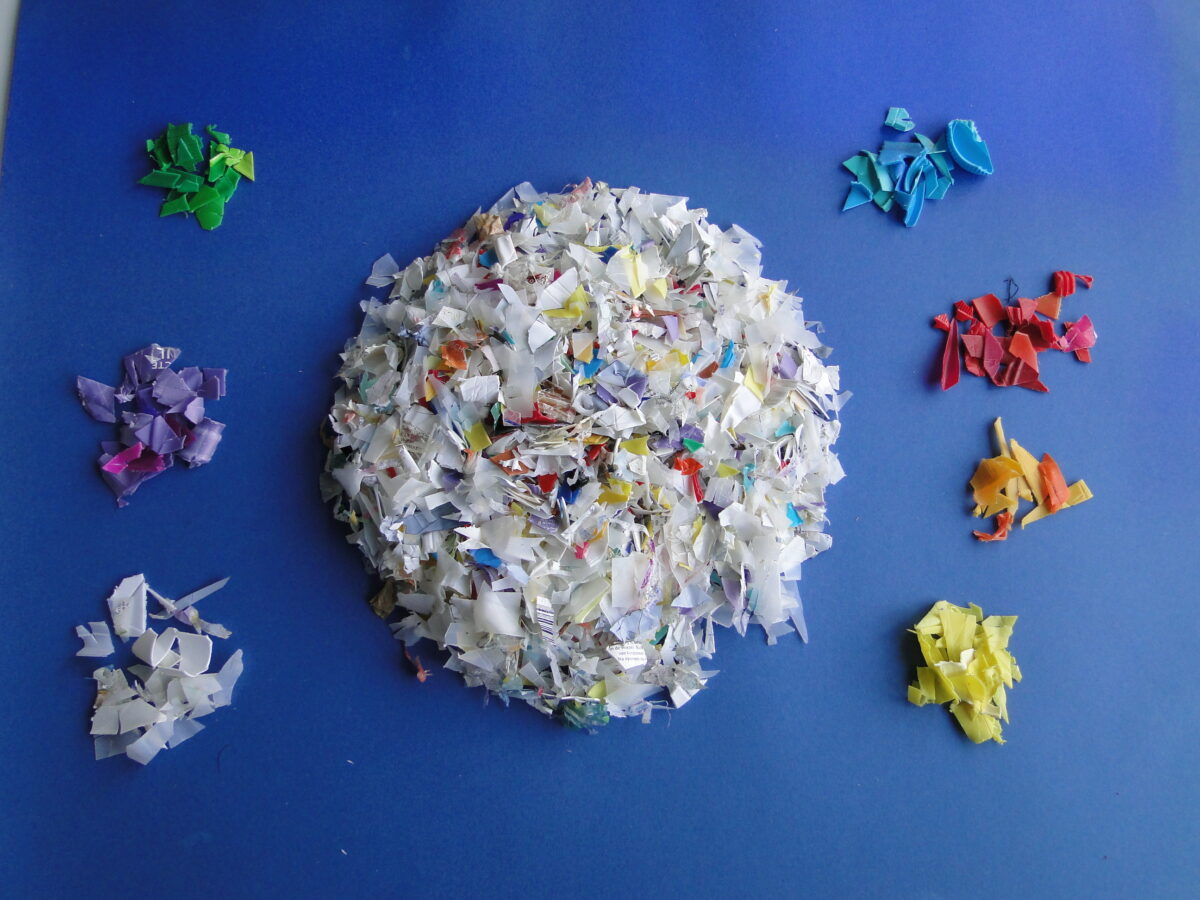
Each batch of recycled plastic is different, so testing and analysis are critical for processing and quality.
The focus on sustainability means companies are working to incorporate more recycled materials into their plastic products. However, recycled materials come with high variability levels that affect how machines run and the quality of finished products. This challenge leads to new approaches in both online and offline testing and analysis that address variations as they arise.
You can also read: New Polyolefins Meet Demanding Use and Sustainability Needs.
Polyolefin Analysis for Recyclate
Polymer Char, of Valencia, Spain, develops and commercializes instrumentation for measuring molar mass and chemical composition distributions in polyolefins, including recycled polyolefins. “Chemical composition distribution properties are important, especially for linear low-density polyethylene, high-impact polypropylene or any industrial copolymer obtained with two reactors or two catalysts,” says Benjamin Monrabal, R&D director. “We have been so specialized in this that we are the only supplier of this type of instrumentation to the polyolefins industry.”
Automation in Polyolefin Analysis
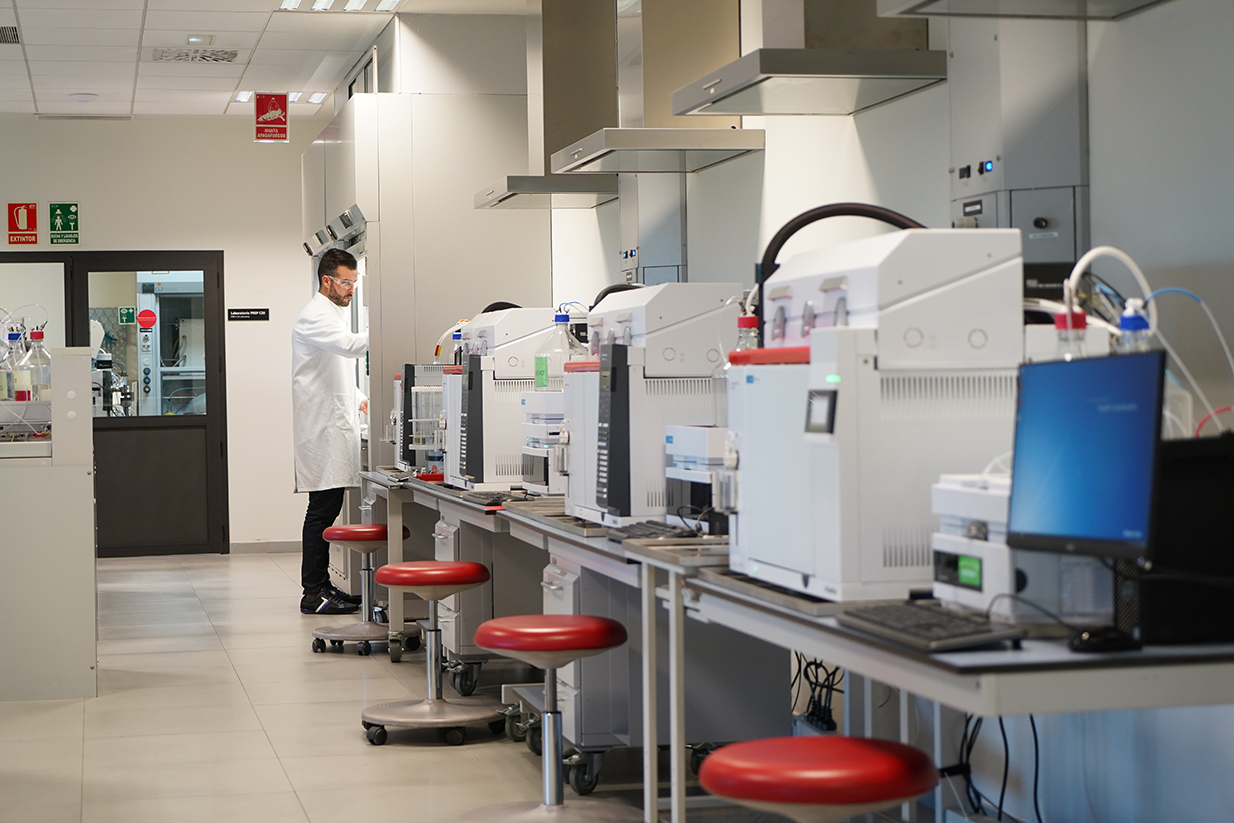
Polymer Char is expanding analytical services with a laboratory for molar mass distribution, chemical composition distribution and viscosity analysis. Courtesy of Polymer Char.
Alberto Ortin, a scientist at Polymer Char, points out that all the company’s instruments are automated, which is important for polyolefins. “Polyolefins are analyzed at elevated temperatures, using chlorinated solvents for dissolution, which entail many inconveniences,” he remarks. “Thus, it’s key to automate the processes, including sample preparation, so the analysts don’t need to handle solvents or wear protective equipment.”
Recently, the company has expanded to offer simpler instrumentation for processor quality control labs. “We came up with the idea to develop separation techniques and instruments that are particularly designed for quality control purposes,” says Monrabal. “Processors who don’t want to spend a lot of money or purchase sophisticated instrumentation can use these quality control devices to measure the molar mass distribution, soluble fraction percentage or intrinsic viscosity. This QC line of instruments is now one of our most popular.”
Manufacturing facilities use these instruments for process control. Consequently, companies can quickly change grades in the reactor. This enables them to see earlier whether reactor adjustments help move the polymer toward a desired microstructure.
Monrabal notes that measuring the intrinsic viscosity of PET is a highly requested application. To address this need, the company developed the Intrinsic Viscosity Analyzer (IVA). The IVA provides a reliable and automatic viscosity meter for analyzing the intrinsic viscosity of polymeric materials in solution.
You can also read: Industrial Automation: Cloud Asset Integration for Smart Manufacturing
Expansion of Analytical Services
The company is also growing its analytical services by opening a Polymer Analytical Laboratory (PAL) for molar mass distribution, chemical composition distribution, viscosity analysis and other relevant polymer properties. “We are one of the only companies that can perform high-temperature gel permeation chromatography, or HT-GPC, at the same time as chemical composition analysis, which provides tremendous information about the material’s microstructure,” says Ortin. “This is helpful, for instance, when processors are used to running a material, and then, suddenly, they see changes in the end product. The microstructure information can be used to find errors or figure out if there is a difference in the material that is leading to different properties in the end product.”
Monrabal adds that analysis of recycled materials will be an important focus of the new PAL facilities. “Using recycled materials is making processing more complex because processors don’t receive a homogenous material, and you have to match product quality even when using recyclates that come from different sources. We are working on building a Polymer Analytical Laboratory brand with a focus on characterization of polymers, and recycled polymers are an important part of this.”
Analytical Methods for Recyclate
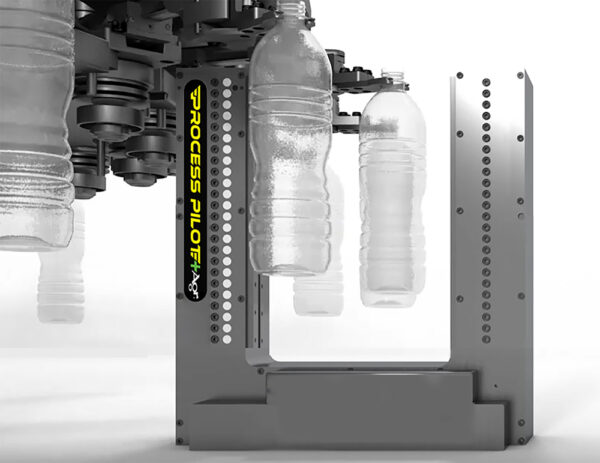
The Process Pilot+ system offers consistent processing of bottles with high levels of rPET content. Courtesy of Agr International.
Fraunhofer LBF, as a research and technology organization, develops analytical methods and collaborates with clients worldwide. The institute’s recyclate analysis began with a request from a packaging company. They wanted to know how much recycled content was in an unknown sample. This information was critical because incorrect amounts could lead to liability issues.
“Based on this and other requests, we developed technologies for determining recycled content,” says Brüll. “We discovered we could use the same analytical methods for recyclates as for virgin materials. These methods include chromatography, spectroscopy, and mechanical tests.”
The institute then began receiving requests for characterizing the recycled content of samples. One can use this to determine which sorting processes produce the best recyclates, for example. “We get a lot of inquiries from collection and sorting companies. Usually, they are not as equipped with the analytical tools that a virgin resin producer would have,” says Brüll. “However, the more they know about their recycled material, the better they can position themselves in the market.”
You can also read: Rheometer: 5 Keys for Optimal Selection
Addressing Variability in PCR
The institute frequently determines how much recyclate a product can incorporate without affecting its durability or production processes. Brüll says the biggest difference with recyclates is their fluctuation by region and season, causing significant quality variation.
“We are on the way to a circular economy, and by supplying our partners with analyses and helping them with the interpretation of data, we can help show that plastic is not bad, it’s part of a solution,” says Brüll. “Based on our findings we may offer recommendations on how to improve a sorting or collection process or what the best applications are for certain recycled materials, for example.”
Looking ahead, he sees food contact materials as one of the next applications for plastic recyclates and increase recycled content. “Health and safety issues will be much more relevant for materials that come into contact with food,” says Brüll. “Proper analysis becomes even more critical because we need to detect trace levels of certain chemicals,” Brüll emphasized.
You can also read: Additives to enhance post-consumer recycled (PCR)
Variability Detection in Plastic Packaging
Agr International Inc., of Meridian, Pa., offers online and offline equipment for testing plastic packaging. This includes pressure and top-load testing capabilities as well as inline systems that perform automatic process control for PET bottle blow molding machines.
“We work with all the major carbonated beverage producers, water bottle and lightweight water bottle producers in the U.S. and around the world,” says Sudha Jebadurai, COO. “Some of our customers are running over 100,000 bottles an hour, which means even 10 minutes of bad production can be costly.”
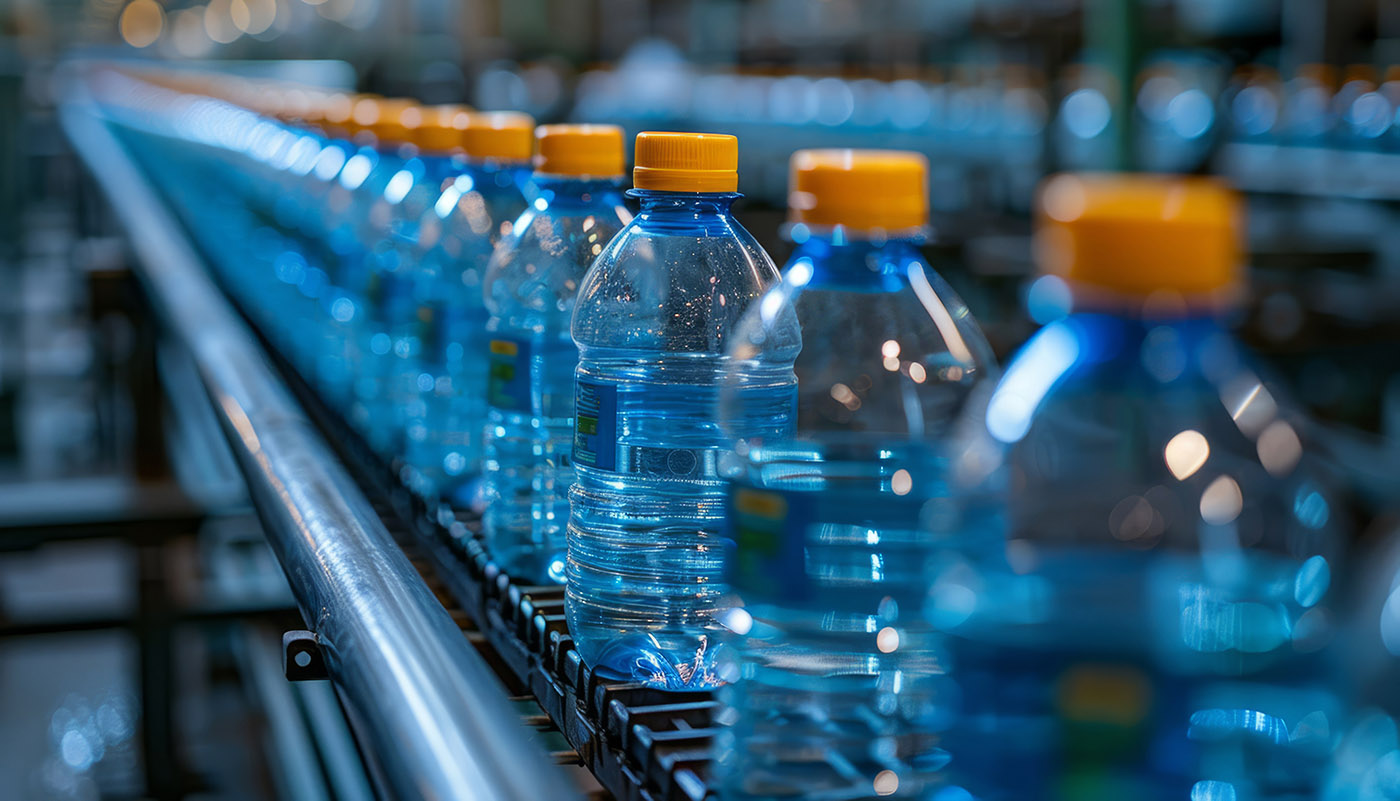
Running over 100,000 bottles an hour, even 10 minutes of bad production can be costly for some manufacturers.
You can also read: Packaging Sorting 4.0: Digital Watermarks & Fluorescent Markers
Automated Monitoring in rPET
The Process Pilot automated blow molder control system provides continuous monitoring, pinpointing problems as they arise and making adjustments. Consequently, this type of monitoring is critical as the use of recycled PET (rPET) increases. The company’s research shows rPET increases material distribution variation and bottle variances by 7 to 10 percent compared to virgin materials. Variations often jam downstream processing equipment, increasing scrap because workers must discard any bottles stuck inside the system. Additionally, rPET introduces contaminants, which can appear as black specs anywhere in the bottle.
“The additives, or toner, used to compensate for yellowing in the recycled material also cause challenges because they directly affect the heat absorption rate of the preform,” notes Jebadurai. “This ultimately changes the heating profile of the bottles, which leads to variances in material distribution that affect thickness. This, in turn, can cause issues with top load, for example, which might mean you can’t double or triple-stack these bottles.”
Agr’s blow molding management system uses a proprietary infrared light absorption technology to collect around 2,000 data points for a single bottle. “This gives us the ability to clearly detect any thin spots across the bottle,” says Jebadurai. “We have found that measuring the thickness profile captures any variance that arises, including from stretch rod failures, improper heating, wrong preforms or incorrect pre-blows.”
By keeping everything within spec all the time, the automatic system helps ensure that machines stay up and running. It also brings labor savings because there’s no need for a process person to constantly manage every variance or situation that occurs.
You can also read: The Technology Behind Food-Grade rPET
Innovations in Process Control
The newest version of the automated platform, known as Process Pilot+, can segregate different controls. Since heating changes take longer than pressure profile changes, separating them speeds up overall reaction times.
“Before this improvement, it took 60 to 90 seconds for changes to be implemented,” says Jebadurai. “Now pressure parameters change every 15 to 20 seconds,” she adds. “This helps especially when a blow mold first starts up because many bottles are discarded during heating profile adjustments. Our system’s multiple loops reduce scrap time from 5 minutes to just 30 seconds.”
Reducing scrap is crucial because bottle manufacturers often run out of rPET. “Recycled material costs more than virgin material,” Jebadurai notes. “Manufacturers are figuring out where and how to source it,” she continues. “Automation helps them use what they have efficiently and minimize waste.”
Originally published in Plastics Engineering Magazine issue May/June 2023. Edited for online by Juliana Montoya.
This assessment assumes recyclate materials derived from the existing collection/sorting/recycling systems (e.g. MRFs). Reuse of plastics packaging materials can be so much simpler if the Consumer packaged goods Companies (CPGs) would get out in the market place and take back their packages! That is the essence of Extended Producer Responsibility (EPR) that CPGs and resin companies shun as an unfair “tax” on their right to pump plastic waste onto the curbsides of municipalities. CPR companies bought that plastic once, come out, get it back, and reuse it!
Dear Thomas, thank you for reading the article and commenting! That’s exactly what we want to promote at PE Magazine.
Producers and the circular economy, in general, must prioritize and promote the reuse and refill of packaging. Companies like Algramo have already implemented this in Latin America and the US. You’re spot on. Our recycling system needs to change. EPR must not only ensure that materials and carbon keep flowing in the economy, but we also need ecodesign laws to make packaging more recyclable. Appreciate your insights on this!