Polyurethane (PU) Recycling: Growing Challenge and Innovation
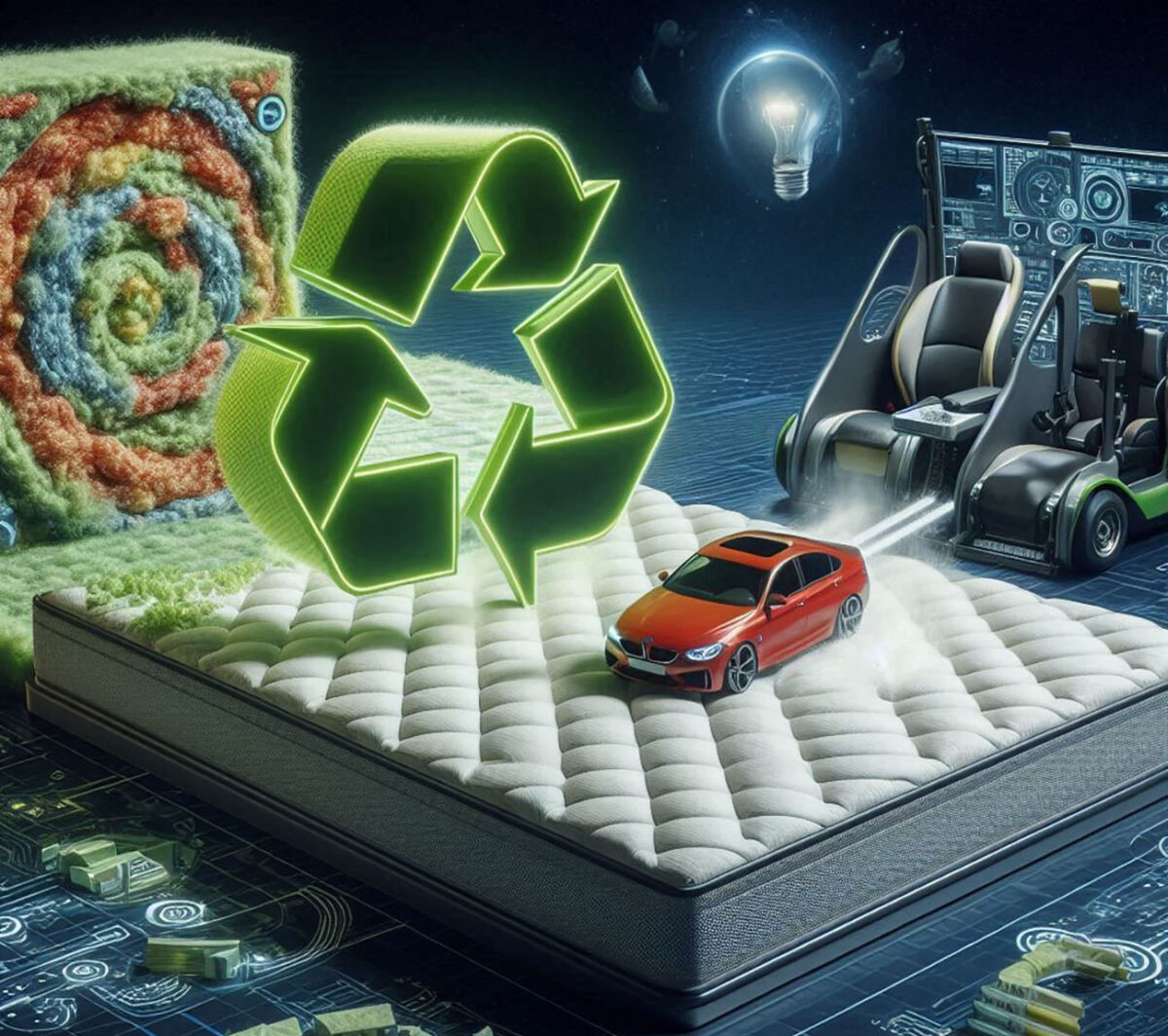
The rapid increase in industrial and domestic waste makes polyurethane (PU) recycling a critical topic of study. Innovative recycling strategies are essential to manage this substantial plastic waste.
This Plastics Engineering research explores the current status and prospects of PU recycling, highlighting key technological advancements and ongoing initiatives.
You can also read: Silent Polyurethane Tires for Electric Vehicles, Antibacterial Polymers: Advancing in Public Health, Electronification of Medical Devices Creates Markets for Plastics , Polymeric Biosensors: A New Era in Medical Diagnostics
Current PU Recycling Methods
Several methods are available for recycling PU: mechanical recycling, monomer recovery, feedstock recycling, incineration, and landfill.
- Mechanical recycling: is a low-cost and straightforward process that involves regrinding PU foam, rebonding the particles with isocyanate, and adhesive pressing.
- Chemical recycling: leverages the thermal reversibility of urethane links. It uses organic compounds to depolymerize PU into monomers and oligomers, which can be separated into useful streams like polyols and amines. The primary chemical processes include acidolysis and glycolysis, performed on an industrial scale.
Technological PU Recycling Advancements
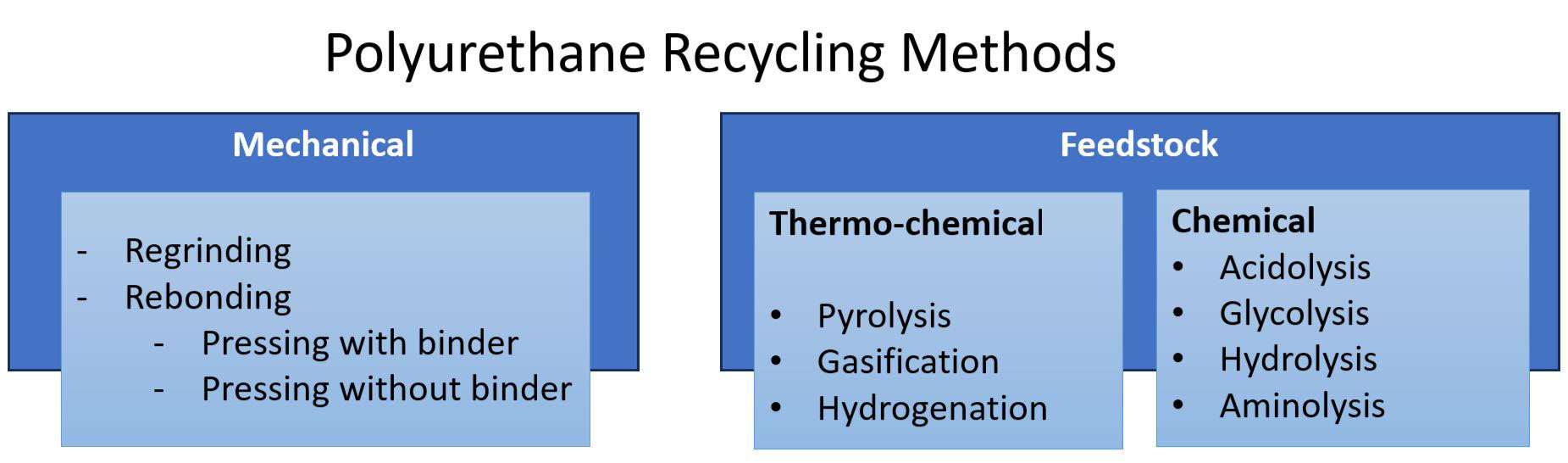
Several methods are available for recycling PU: mechanical recycling, monomer recovery, feedstock recycling, incineration, and landfill. Nevertheless, innovative recycling methods like thermochemical, generate highly reactive building blocks, such as C2 and C3, which are essential for producing valuable intermediates and chemicals. Courtesy Macromolecular Chemistry and Physics, Copyright (2020).
Thermochemical recycling transforms plastic waste into gas and oil, including pyrolysis, gasification, and hydrogenation. Pyrolysis has gained renewed interest in capturing carbon and producing reusable materials for the chemical industry. These processes generate highly reactive building blocks, such as C2 and C3, essential for producing valuable intermediates and chemicals.
Current Initiatives and Future Directions
Several countries have initiated foam collection programs to manage flexible foam waste from mattresses and furniture. For example, France’s Eco-Mobilier program is setting a precedent, with similar initiatives discussed in the UK, the Netherlands, and Belgium. Moreover, these national recycling programs aim to develop a value chain from collection to the creation of new materials and applications, which requires significant research and technological advancements.
In the US, local initiatives focus on physically recycling flexible foam consumer waste, turning it into sheets for the carpeting industry. The EU-funded project “PUReSmart” aims to develop a complete circular product life cycle, making PU a truly sustainable material.
Innovations and Future Prospects
Looking forward, redesigning PU polymer architecture for easier recycling is crucial. Some promising approaches include chemically recyclable PUs from β-methyl-δ-valerolactone (MVL) polyesterol, which can be recycled into the MVL monomer. Additionally, vinylogous urethane vitrimers can be reprocessed like thermoplastics, although converting them back into foam remains a challenge.
Conclusion
The challenge of managing PU waste is driving significant innovation in recycling technologies. Additionally, from mechanical and chemical methods to thermochemical processes, various strategies are in the exploration and implementation phase globally. National and international initiatives, coupled with ongoing research, are crucial for developing sustainable solutions.
By rethinking polymer architecture and enhancing recycling techniques, PU can transition towards a more sustainable lifecycle, addressing both environmental and economic concerns.
To read more: Current and Future Trends in Polyurethanes: An Industrial Perspective