The University of Maine Unveils the World’s Biggest 3D Printer
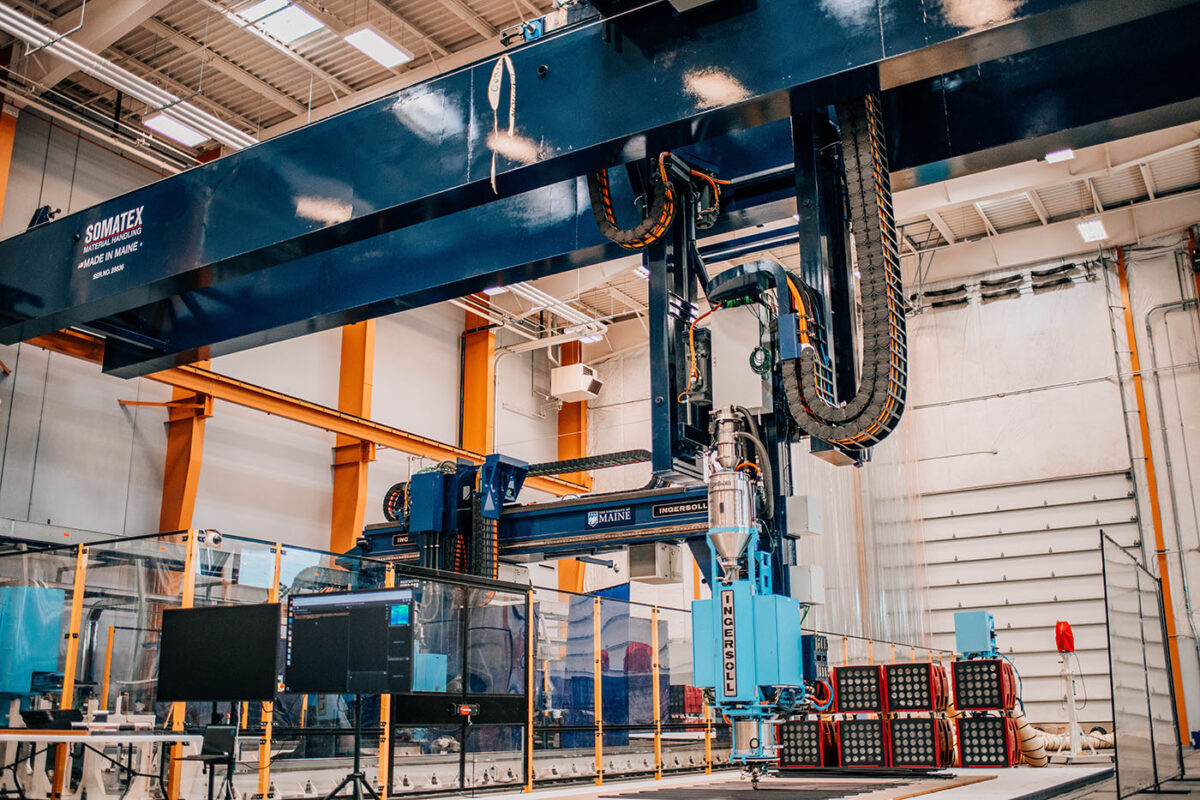
This massive advanced-manufacturing machine will be used to print housing, boats, infrastructure and military products
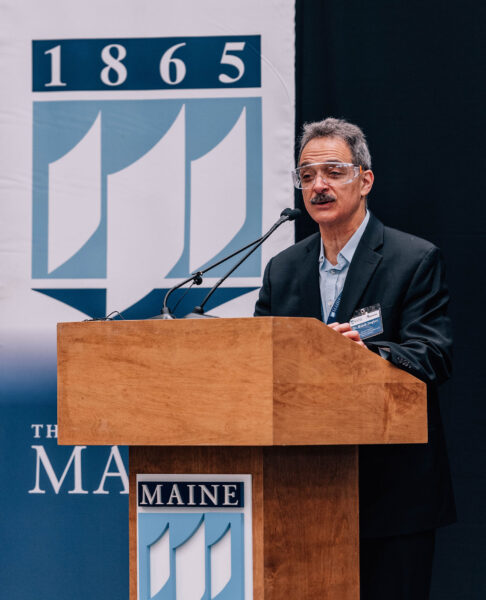
Dr. Habib Dagher, Executive Director of UMaine’s Advanced Structures and Composites Center, at the April 23 unveiling.
When it comes to 3D printing, the University of Maine likes to go big. Already home to the world’s biggest 3D printer, the university on April 23 unveiled a polymer printer four times that size. It foresees using it to print houses, boats, and infrastructure and even helping to develop military vehicles.
The university has dubbed the machine the Factory of the Future 1.0 (FoF 1.0). It is housed in the Advanced Structures and Composites Center (ASCC) on the UMaine campus. The new printer’s frame fills up the large building and can print objects 96 feet long by 32 feet wide by 18 feet high, equaling a print volume of 55,296 cubic feet. It consumes as much as 500 pounds of thermoplastic material per hour and can print a modest single-story home in about 80 hours.
Numerous Partners Supported the Project
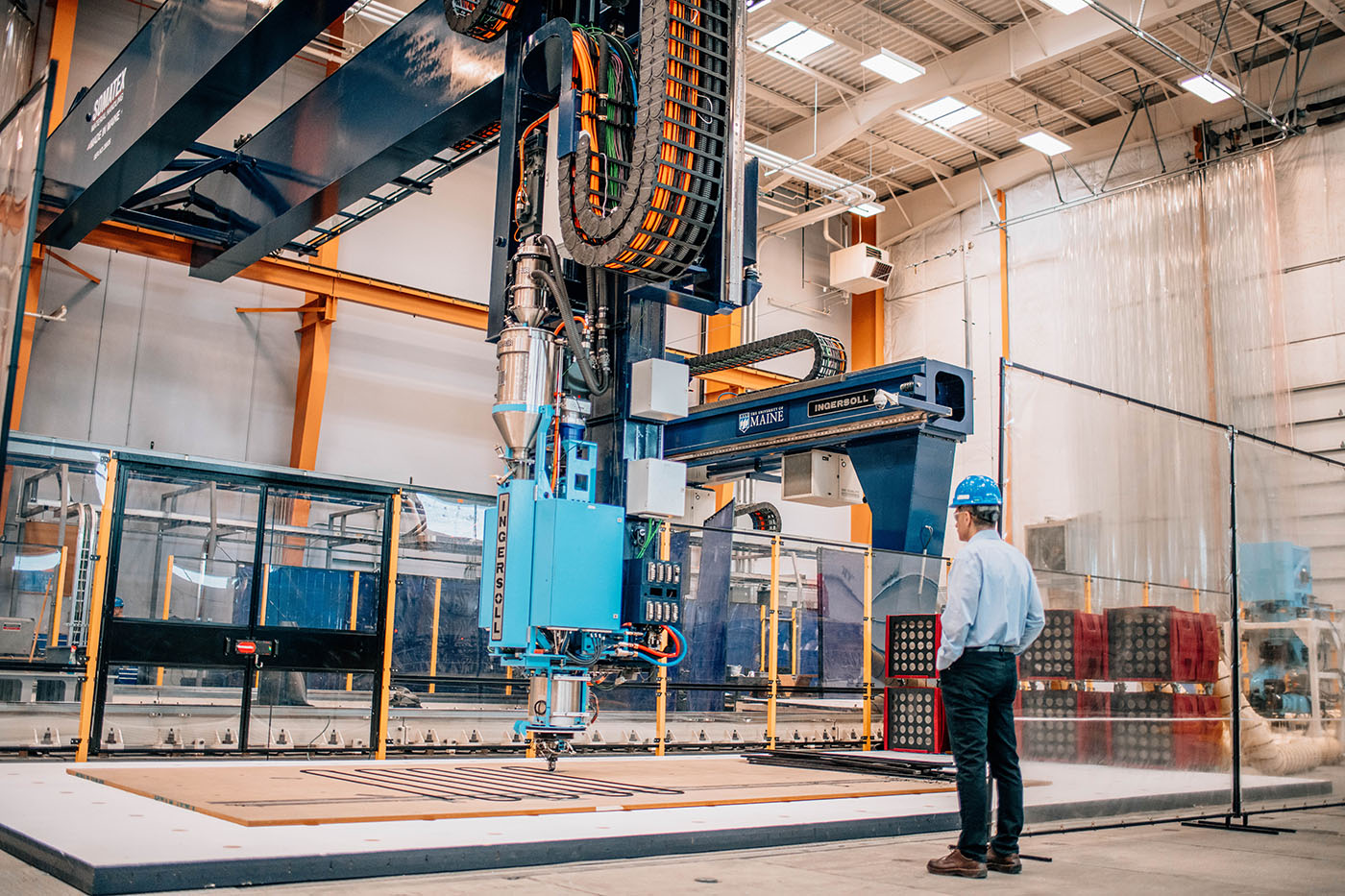
Dr. Dagher watches the printer in action. He says it will be used to manufacture housing, boats, infrastructure and military vehicles.
UMaine worked with several partners to produce the printer, including Rockford, Ill.‐based Ingersoll Machine Tools Inc. and Detroit-based Somatex Inc., a crane and hoist specialist. It received funding from the Army Corps of Engineers, the U.S. Department of Defense, and the Department of Energy.
Ingersoll also made the university’s previous huge printer, MasterPrint, which in 2019 was honored by the Guinness World Records as the world’s largest at the time. They used it then to print what Guinness certified as the largest solid 3D‐printed object and the largest 3D‐printed boat. The boat, called 3Dirigo, measured 25 feet long and weighed 5,000 pounds. UMaine printed it entirely out of Techmer PM’s Electrafil ABS 1501 3DP –– a carbon fiber‐reinforced ABS resin formulated specifically for large-format additive manufacturing (LFAM).
The parties determined the relative size of the new printer compared to the existing one by assessing the print volume of each. The current MasterPrint has a print volume of 60 ft long by 22 ft wide by 10 ft high = 13,200 cubic feet. The FoF 1.0’s print volume of 55,296 cubic feet yields a ratio of 4.189 times greater.
Printer to Run a Wide Variety of Materials
As for the materials likely to run on FoF 1.0, Dr. Habib Dagher, executive director of the ASCC, said: “We are exploring a wide range of existing, modified and new resin systems. The equipment can handle a wide range of low-temp to very high-temperature aerospace-grade thermoplastics.”
Most of what it produces is recyclable, so “you can basically deconstruct it, grind it up if you wish” and “do it again”, according to Dagher. He says they will use the new printer “to catalyze the future of sustainable manufacturing in a number of industries.”
Dri-Air Industries Inc. of East Windsor, Conn., supplied the material dryers used in the project.
FoF 1.0 isn’t merely for large-scale printing, UMaine points out. It dynamically switches between various processes such as large-scale additive manufacturing, subtractive manufacturing, continuous tape layup and robotic arm operations. Access to it and MasterPrint “will streamline manufacturing innovation research at the center. The two printers collaborate by sharing the same end-effectors, or by working on the same part.”
Developing Collaborative Robotics and AI
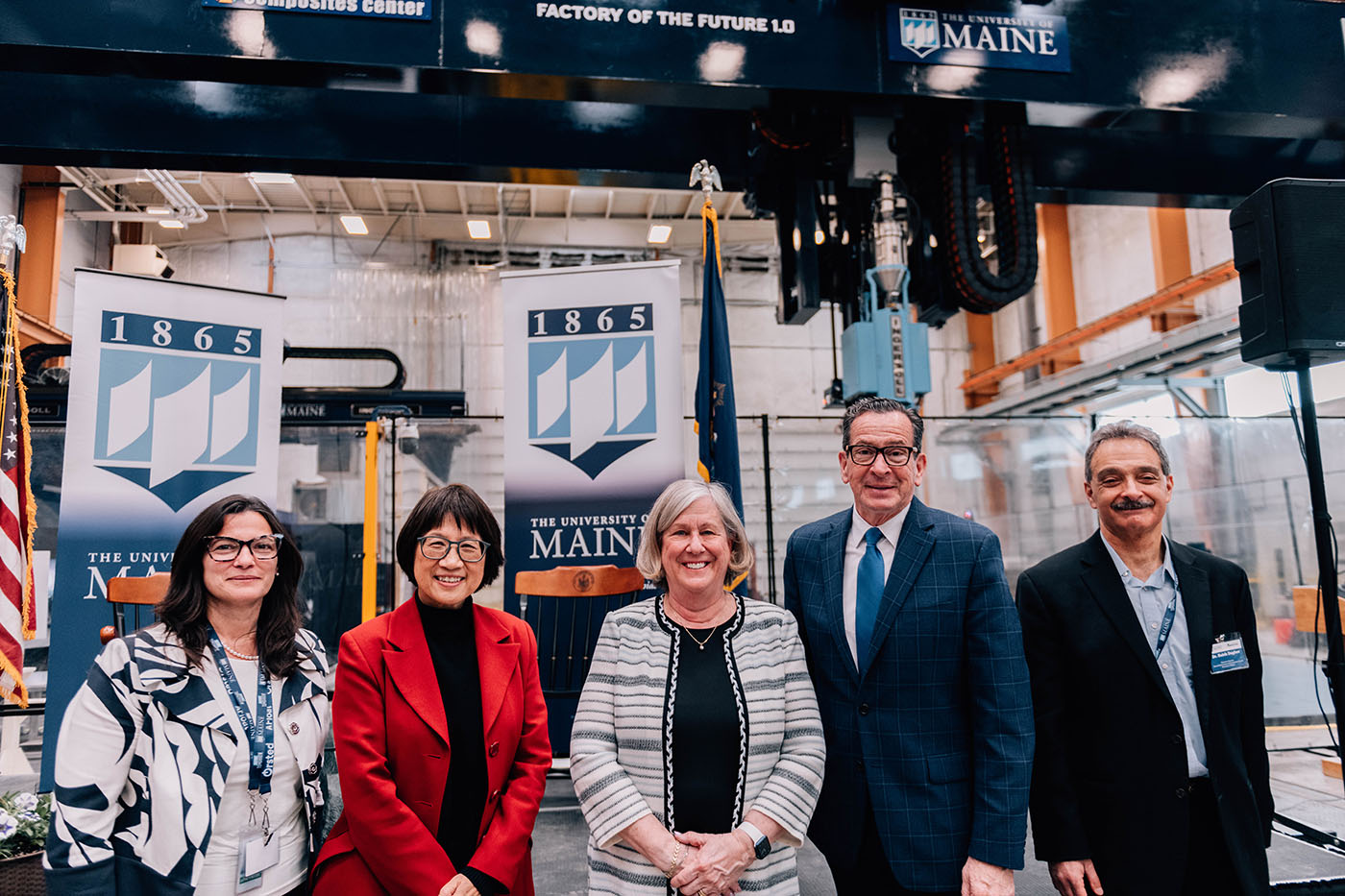
Some key leaders attended the unveiling event. From left to right: Giovanna Guidoboni, Dean, Maine College of Engineering and Computing; Heidi Shyu, Under Secretary of Defense for Research and Engineering; Joan Ferrini-Mundy, President of the University of Maine; Daniel Malloy, Chancellor of the University of Maine System; and Dr. Habib Dagher, ASCC’s Executive Director.
The printer opens up new research frontiers to integrate these collaborative robotics operations at a very large scale, says Dagher. It uses “new sensors, high-performance computing and artificial intelligence to create born-certified systems that meet high quality standards.”
The FoF 1.0 will advance various initiatives, including developing bio-based feedstocks from wood residuals that are abundant in Maine. Techmer PM says it is again active in developing materials for this project. This technology will advance commercialization efforts such as its BioHome3D project. It will be used to create sustainable, affordable housing, while also propelling crucial technological advancements for national security, particularly in lightweight rapidly deployable structures and vessel technologies.
“Maine needs an estimated 80,000 additional homes by 2030, many specifically for households with incomes at or below the area median income,” notes Mark Wiesendanger, development director of MaineHousing, the state’s housing authority. “This new technology allows UMaine-ASCC to scale up its research and production of its innovative, bio-based 3D-printed home technology,” he said.
This effort, Wiesendanger added, creates another means of producing quality affordable housing. It also will drive costs further down, and use abundant wood residuals from Maine’s sawmills.
New Research Lab Planned on Campus
UMaine President Joan Ferrini-Mundy noted the new printer’s unveiling comes ahead of this summer’s groundbreaking of a new 48,000-square-foot research laboratory called the Green Engineering and Materials (GEM) Factory of the Future. Scheduled to break ground in August, the university is positioning the facility to enhance manufacturing innovation across multiple sectors.
“Its primary aim,” said Ferrini-Mundy, “is to facilitate and scale-up more sustainable manufacturing practices by introducing next-generation solutions and biomaterials, addressing challenges such as diminishing workforces and strained supply chains with local solutions.”