Pulp and Paper Waste for Fiber-Reinforced Polymer Composites
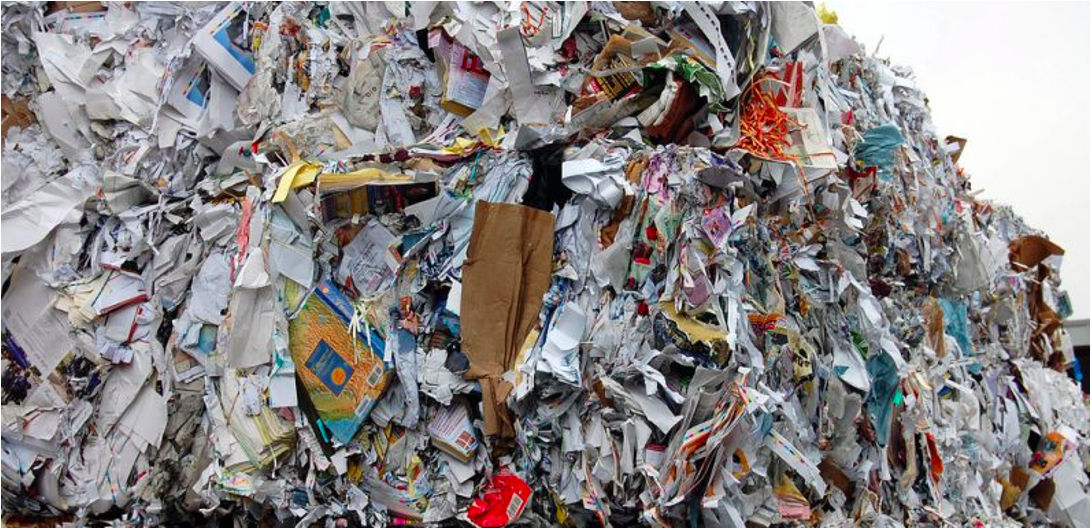
Fiber-reinforced polymer composites (FRPCs) present a promising solution for diverting waste generated by the pulp and paper industry from landfills.
The global pulp and paper industry generated 110 million tons of solid waste in 2017. In Consequence, collaborative efforts address this urgent challenge by championing circular economy principles. These initiatives focus on redirecting pulp and paper waste away from landfills and transforming it into valuable resources.
You can also read: Natural Fibers are Trending for Plastic Reinforcement
Upcycling Waste Cellulosic Fibers
Specifically, ongoing projects seek to harness waste cellulosic fibers from pulp and paper industries to manufacture FRPCs for industrial applications. This innovative approach involves utilizing recycled waste cellulosic fibers (RWCF), in addition to polypropylene, and a coupling agent known as Maleic anhydride grafted polypropylene (MAPP).
Researchers are investigating the impact of several crucial material and process factors on the mechanical and thermal properties of FRPCs. These factors include the MAPP content, screw speed (RPM), fiber size, and fiber content loading. Through meticulous analysis and experimentation, they aim to optimize the performance and sustainability of FRPCs.
Polymer Composites Tensile Properties
Scientists characterized the polymer composites’ mechanical properties following the ASTM D638 standard, employing a strain rate of 10 mm/min.
- MAPP content:Samples containing 20% cellulose fiber and progressively increasing amounts of MAPP showed notable results. Adding 3% MAPP enhanced both the tensile strength and tensile modulus. Specifically, the tensile strength increased from 32.45 MPa to 41.28 MPa, while the tensile modulus rose from 2329.2 MPa to 3207.1 MPa. However, this improvement came at a cost. The elongation at break decreased as a result. Further increasing the MAPP content to 5wt% did not lead to any improvement in strength and modulus.
- Screw speed:Increasing screw speed resulted in a decrease in both tensile strength and modulus. This decrease occurred because of the reduction in fiber length.
- Fiber size:Non-sieved FRPCs exhibited the highest tensile strength and modulus compared to all other samples. The presence of long fibers in non-sieved samples contributes positively.
- Fiber content:In all the composites with 10-30 wt.% fiber), the strength and modulus exceeded those of pristine PP. However, the tensile strength and modulus peaked at 20 wt.% fiber loading and declined at 30 wt.%.
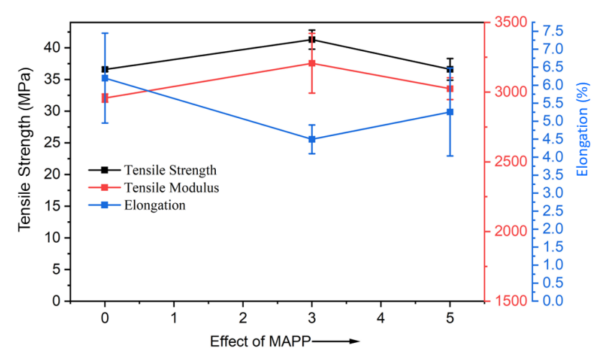
Effect of MAPP on Tensile Properties. Courtesy of Waste Cellulosic Fiber and Polypropylene Composites: A Study on Fiber Preprocessing, Loading, and Compounding. ANTEC 2024.
Thermal Behavior
Engineers tested the thermal properties from the polymer composites by subjecting the samples to heat-cool-heat cycles under nitrogen.
- MAPP content: The PP/20% cellulose fiber with progressive addition of MAPP exhibited increased crystallinity, reaching its peak at 3%. Improved dispersion, interfacial adhesion, and nucleation collectively contribute to this enhancement.
- Screw speed:Increasing compounding speed showed a decreasing trend in crystallinity. Higher screw speeds generate elevated shear forces within the extruder, leading to mechanical scission of the polymer chains. This process reduces their average length and molecular weight.
- Fiber size:Samples utilizing non-sieved fiber appeared to exhibit higher crystallinity. The presence of fines within the material could account for this phenomenon.
- Fiber content:The addition of fibers improved crystallinity, reaching its peak at 20%. However, at 30%, it declined.
Effect of MAPP on Thermal Properties. Courtesy of Waste Cellulosic Fiber and Polypropylene Composites: A Study on Fiber Preprocessing, Loading, and Compounding. ANTEC 2024.
The Ideal Match for Composites
Overall, the composite made with 20 wt.% non-sieved fiber and 3 wt.% MAPP at 300 RPM achieved the highest tensile strength, measuring approximately 42 MPa. It represents a 30% improvement, accompanied by a 47% increase in modulus.
In summary, the studies conducted reveal the significance of the factors assessed. The addition of fibers enhances strength and modulus, peaking at a 20% fiber loading. Crystallinity increases with fiber introduction but declines beyond 20%. These findings provide a solid foundation for future research and development of more efficient and sustainable FRPCs.