Key Innovation in Hybrid Epoxy Composites
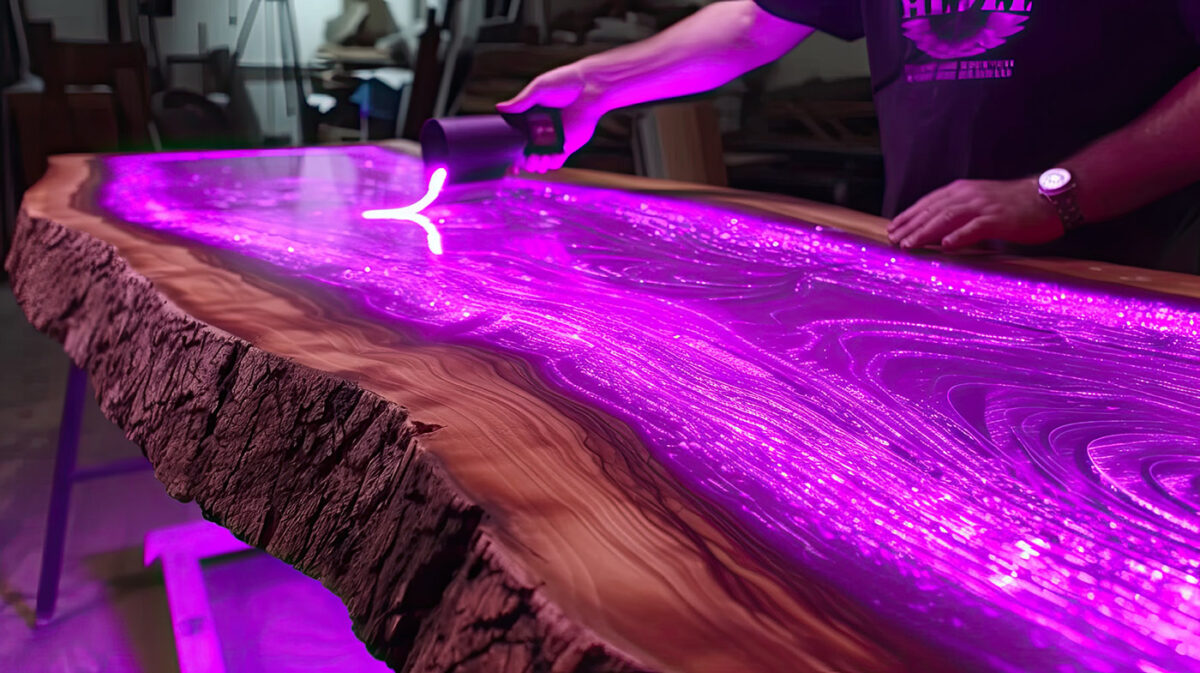
Hybrid polymer composites with new blends of unsaturated polyesters and hybrid epoxy resins could enhance performance in various industries, including aerospace and automotive.
Researchers have integrated orthophthalic, isophthalic, and terephthalic unsaturated polyester resins with bisphenol-A-based epoxy-vinyl ester resin to boost the properties of epoxy resins. They created 14 combinations of these resins and subjected them to rigorous physical, chemical, and mechanical testing. The results show that both binary and ternary blends perform better than traditional single-resin systems.
You can also read: Advancements in 3D Printed Hybrid Composite Structures
Crosslinking and Performance Enhancement
The key findings from the study highlight the enhanced crosslinking in these composites, which is central to their improved performance. Researchers used advanced diagnostic methods like Fourier-transform infrared spectroscopy (FT-IR) and scanning electron microscopy (SEM) to analyze the materials. These tests revealed better polymer chain interactions and crosslinking processes, evidenced by denser and more uniform structures in SEM images.
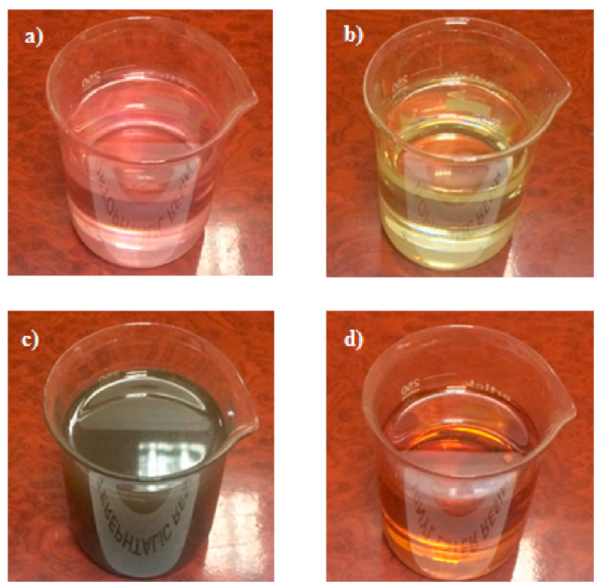
a): Orthophthalic polyester, b): Isophthalic polyester, c): Terephthalic polyester, and d): Vinyl ester.Courtesy of Engineering properties of hybrid polymer composites produced with different unsaturated polyesters and hybrid epoxy.
Practical Applications and Manufacturing Efficiency
Another significant advantage of these hybrid composites is their ability to maintain standard gelation temperatures. This attribute allows manufacturers to produce new materials under typical manufacturing conditions without requiring special treatments. This, also makes them highly practical and cost-effective for industrial applications.
Durability and Energy Absorption
The study also noted remarkable improvements in impact resistance and energy absorption capabilities. Researchers found that binary and ternary resin blends are more durable, making them ideal for applications where materials are subject to frequent mechanical stresses. This makes them particularly suited for sectors such as automotive and aerospace, where materials need to withstand extreme operational demands.
Tailoring Hybrid Epoxy Composites for Specific Needs
The research further demonstrated that the choice of resin combination affects the composite’s final properties. For instance, blends that include isophthalic resin typically offer better thermal stability and mechanical strength than those incorporating orthophthalic resin. This finding suggests that manufacturers can customize these materials to meet specific engineering requirements, enhancing their applicability across a wide range of industries.
As companies continue to seek out better and more adaptable materials, these hybrid polymer composites promise to deliver not only improved performance but also greater sustainability and efficiency in production and use.