Extrusion Troubleshooting – Key Drivers (Part 2 of 3)
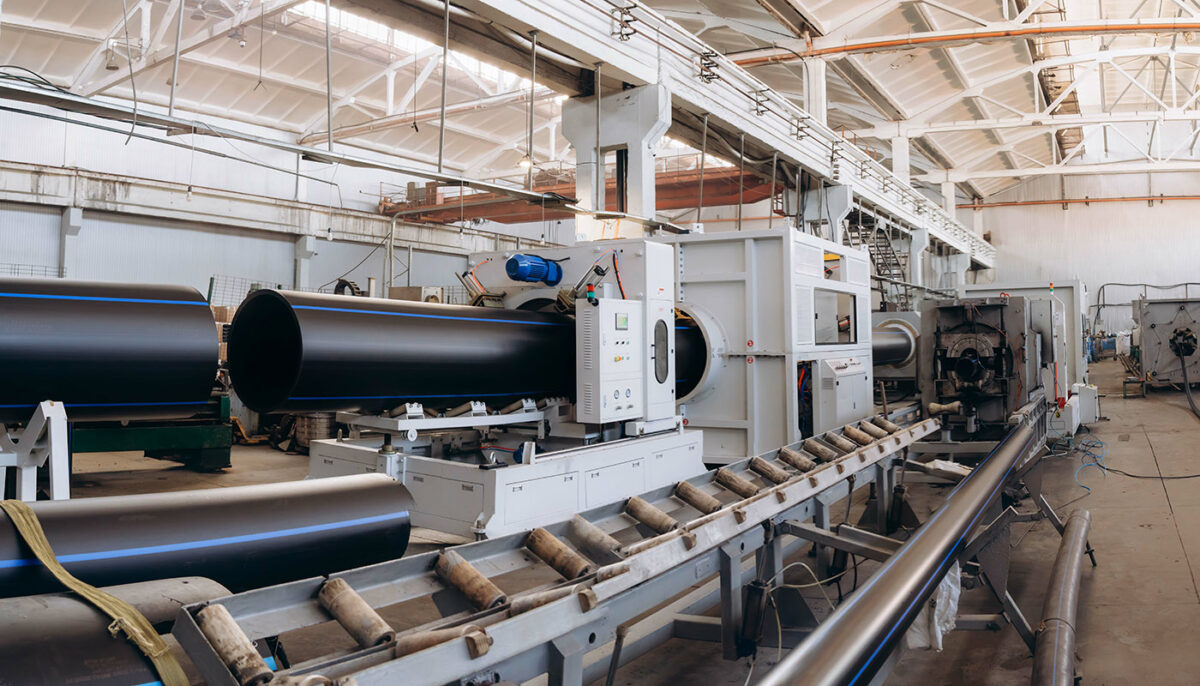
Extrusion has contributed to a 5.5% increase in the construction sector’s growth, underscoring the importance of addressing its troubleshooting factors.
Are we experiencing extrusion troubleshooting once more? This second chapter aims to provide further insights into the industry. One key sector fueling the expansion of extrusion in Europe is construction, which saw a 5.5% growth between 2020 and 2021. Not only does it exhibit high demand, but it also yields positive outcomes thanks to customized solutions crafted through substantial investment in research and development.
You can also read: Extrusion Troubleshooting – The Current Key Drivers (1 of 3)
Given this promising outlook, it becomes crucial to focus on potential troubleshooting drivers to ensure high productivity, competitiveness, quality, and profit. To address this need, we’ve put together a comprehensive guide into three articles. Here is part 2.
Unmelted Particles in the Extruded Part
The origin of the problem probably comes from the mesh package, incorrect temperature set-up, and contamination, among others. To repair this issue, it is necessary first to check if there are any holes to be considered in the screen pack to replace them immediately and second, if there is good or bad heating through the whole line (this includes the high plate and the extruder die). Finally, increasing the temperature in the compression and metering zones could be helpful.
Off-color Extrusion Profile
The reason for an off-color profile involves polymer degradation, poor or incorrect mixing, and inadequate die design. The 4 alternatives to remedy this circumstance may be first to reduce screw temperatures or speed, two, to add mixing heads or concentrators to achieve homogeneous pigment mixing, and/or as a third measure, optimize die flow or use a smaller or slower extruder for material output.
High Die Pressure Drop
This is due to clogging or incomplete melting of the resin, here increasing temperatures, as well as replacing screen packs or using screens with large openings can attenuate or reduce pressure drops outside the range of a qualified process range.
Rough Surface / Die Lines / Melt Fracture
The root cause of this problem lies within the isolated die and resin area. To tackle such issues, adjustments must be made to the die design and/or temperature, lowering the melt temperature, and/or employing a material with either a lower molecular weight or a wider molecular weight distribution.
You can also read: Plastics extrusion Market is Growing at CAGR of 6.72% between 2023 and 2030.