Redefining Recycling: Depolymerization of PET
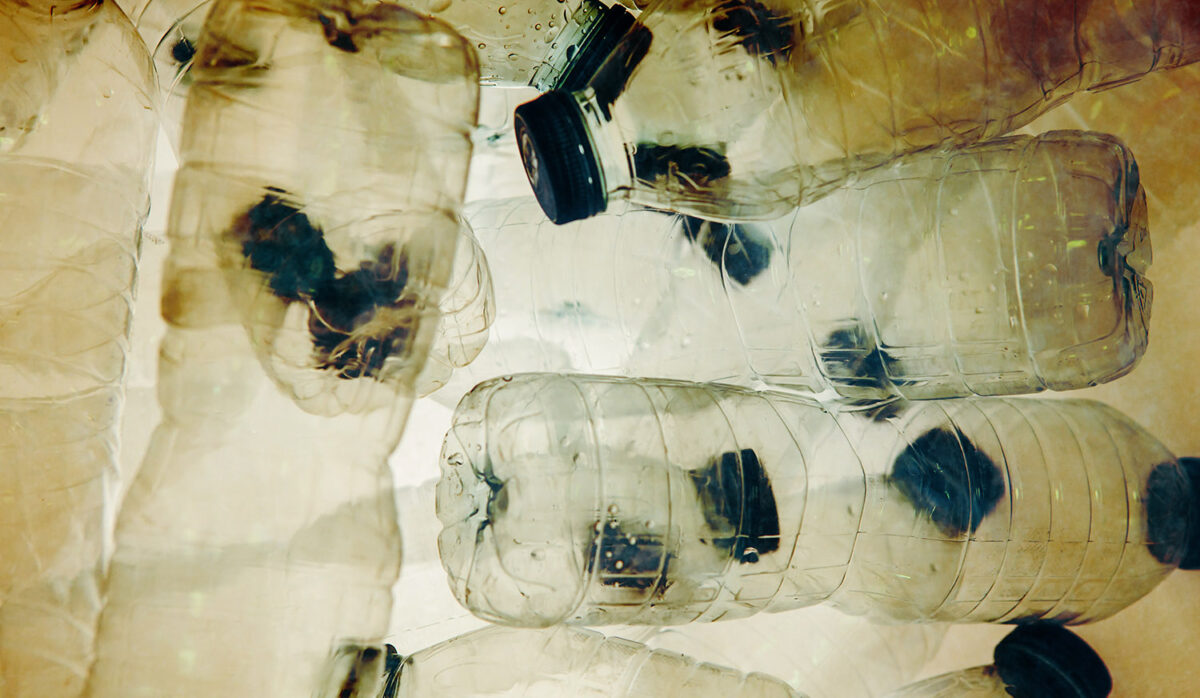
Chemical recycling, particularly the depolymerization of PET presents a groundbreaking approach to tackling the global plastic waste dilemma.
This innovative process transforms PET, one of the most commonly used plastics, back into its constituent monomers or other valuable materials. By breaking down PET at the molecular level, chemical recycling surpasses traditional mechanical recycling methods, which often struggle with quality degradation and limited applicability.
You can also read: Golden Design Rules: Enhancing PET Recycling Through Design
Depolymerization not only offers a promising route to infinitely recycle plastics but also aligns with the principles of circular economy, where materials are kept in use for as long as possible. As the world grapples with the escalating issues of plastic pollution and waste management, the depolymerization of PET emerges as a key technology in the evolution of sustainable materials management.
Exploring Depolymerization of PET
Global PET consumption totaled 89.3 million metric tons (MMT) in 2021. PET is the fourth most consumed plastic in the world. Scientists are focusing on developing practical advances for PET depolymerization due to the high consumption of PET.
The image below shows seven techniques studied for PET depolymerization to produce rPET or other commodities. TPA, EG, DMT, DET, BHET, BDM, and MHET are the most common products of PET depolymerization.
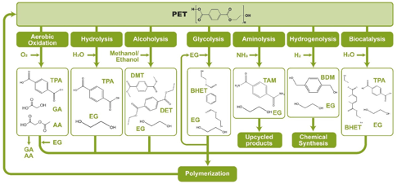
Strategies for PET chemical recycling. Courtesy of Green Chemistry.
Advancements in Depolymerization of PET
As restrictions tighten, new chemical recycling processes centered around catalysis are emerging.
- Hydrogenolysis with noble metals
This process converts polymers into hydrocarbons (ranging from C1 to C50). It cleaves the carbon–carbon bonds in the presence of hydrogen and noble metals (e.g., Ru, Pt, etc.) as catalysts.
- Functionalization and reactive extrusion
Is a strategy to valorize plastics. For this purpose, chemical groups (such as aromatic rings, halogen, etc.) are added to them using chemical methods like reactive extrusion. The latter involves an extruder as a continuous chemical reactor.
- Microwave-assisted conversion
This technique heats the reaction system, reduces reaction times, and improves the kinetics of some chemical reactions. Furthermore, microwave radiation enables electromagnetic energy to be absorbed uniformly and efficiently at microwave-absorbing points (such as the catalyst surface).
Commercial Activity of PET Depolymerization
Currently, several strategies exist for PET depolymerization. However, most of them remain at laboratory scale because their commercial implementation didn’t work. Some exceptions are:
- HydrolysisThe US and Switzerland have advances for commercial purposes. For example, Circ, a US-based start-up, utilizes hydrothermal processing to hydrolyze PET fiber to TPA and EG.
- MethanolysisEastman Chemical has unveiled plans to construct a $250 million PET methanolysis plant in Tennessee. Loop production also have a patent in methanolysis, but they are struggling with industrialization.
- GlycolysisVarious companies are actively pursuing the commercialization of glycolysis processes, each employing unique approaches. JEPLAN uses metal hydroxide and EG for PET glycolysis. Loniqa utilizes an imidazole-based catalyst tethered to a magnetic iron oxide nanoparticle. IBM developed VolCat, a PET glycolysis process catalyzed by a volatile organic base.
- BiocatalysisIn 2021, Carbios inaugurated a demonstration plant for their enzyme-catalyzed process. The company currently operates a 1.2 kton per year demonstration facility and aims to establish a 40 kton per year facility by 2025.
You can read the full article of plastics recycling technologies here.