Polypropylene Recycling from Disposable Face Masks
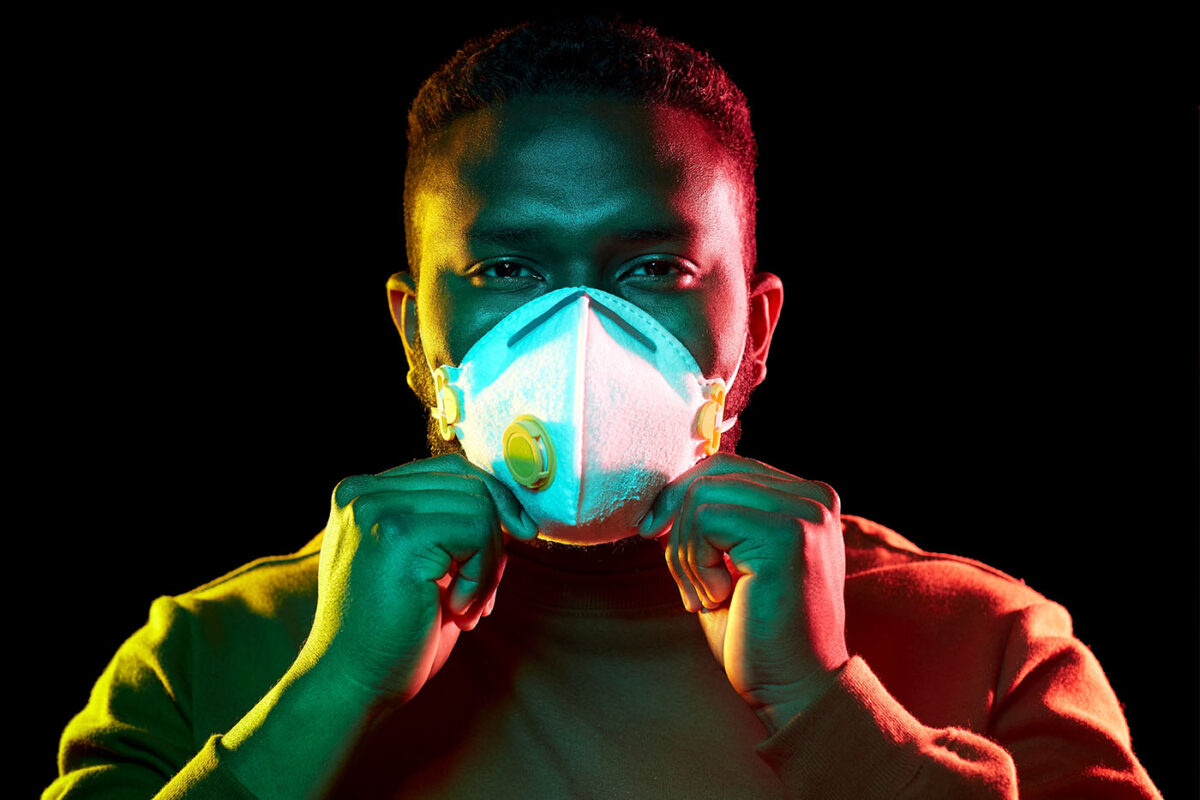
Solvent-targeted recovery and precipitation (STRAP) process stands out as a promising alternative to polypropylene (PP) disposable face mask recycling.
The COVID-19 pandemic triggered a significant surge in the use of disposable face masks as a precautionary measure. Although these masks are crucial for containing the spread of the virus, they have also posed a new environmental challenge. People worldwide use millions of disposable face masks, and many of them eventually wind up in landfills and dumps. By 2023, global production of personal protective equipment resulted in an annual waste output between 4.68 and 6.24 million tons.
You can also read: AI-powered Sorting Project Boosts Polypropylene Recycling
Polypropylene (PP) predominantly constitutes disposable face masks. This plastic has a high market value but is one of the least recycled. As a result, the U.S. Department of Energy (DOE) funded research through the Center for Chemical Upcycling of Waste Plastics (CUWP). The work contributed to designing the STRAP process of PP from disposable face masks. Furthermore, researchers developed an environmental and techno-economic analysis of this method to evaluate its feasibility compared to virgin PP production.
Recycling PP via STRAP Method and Decolorization
STRAP method enabled the extraction and separation of approximately 90 wt% of PP within a dissolution time of 5 minutes. Additionally, N, N-Dimethylacetamide facilitated the removal of color from the recovered PP, resulting in a high-purity PP. The recovered plastic exhibits thermochemical properties like those of virgin PP resin.
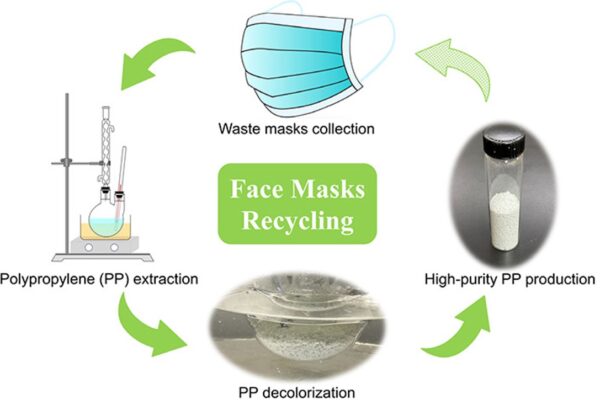
High-purity polypropylene from waste disposable face masks via STRAP method and decolorization. Courtesy of Green Chemistry.
Diminishing Environmental Impact
Researchers conducted an environmental impact assessment for the STRAP process, focusing on recovering polypropylene (PP) colored. This analysis compares the environmental impacts of producing 1 kg of PP using conventional methodologies against the STRAP method. The depicted data illustrates that the carbon footprint of the STRAP process without color removal (0.57 kg CO2 eq./kg PP) is notably diminished compared to virgin resin production (2.07 kg CO2 eq./kg PP). Remarkably, the STRAP process engenders approximately 72% fewer emissions. This underscores its potential as a sustainable alternative for PP recovery.
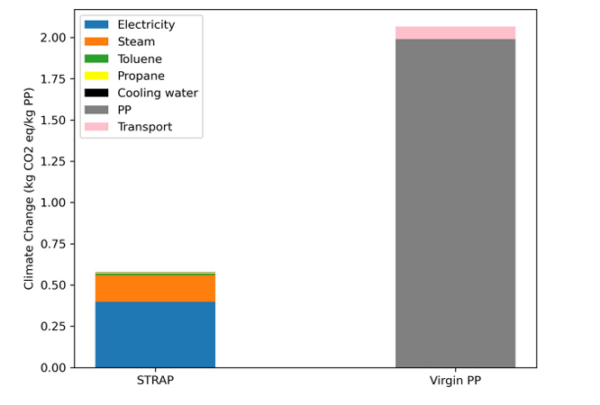
Climate change impact of producing colored PP via the STRAP process compared with virgin PP. Courtesy of Green Chemistry.
Economic Feasibility
Finally, scientists developed a techno-economic and sensitivity analysis of the STRAP process for recovering PP colored. The first indicates that processing a capacity of 5,292 tons of PP colored annually, results in an MSP of 1.42 USD/kg. This price is comparable to the average market values of virgin PP and the cost of post-consumer PP (0.94-2.52 USD/kg). Moreover, the total capital investment amounted to 24.7 million USD, with an annual operating cost of 1.87 million USD. On the other hand, sensitivity analysis shows the impact of economies of scale across various processing capacities.
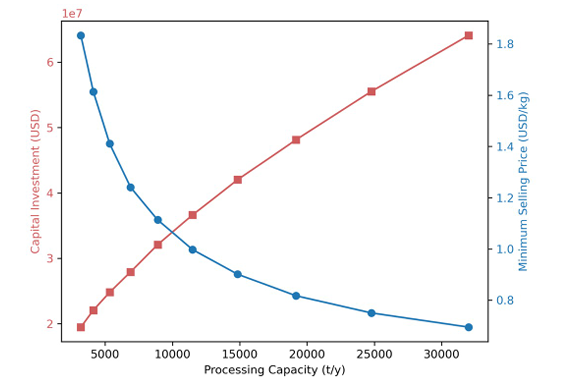
Sensitivity analysis for economies of scale of the STRAP process without color removal. Courtesy of Green Chemistry.
The results reveal that beyond an annual capacity of 7,000 tons, the MSP of the polypropylene (PP) produced via the STRAP process is approximately half the maximum market value of virgin resin and the price of post-consumer PP (ranging from 0.94 to 2.52 USD/kg). These findings underscore the economic viability of the STRAP process without color removal. It also implies that this technology could scale up to reclaim PP from discarded face masks. Thus, enabling both environmental and economic benefits.