Dual-Curing: A Game Changer for Additive Manufacturing
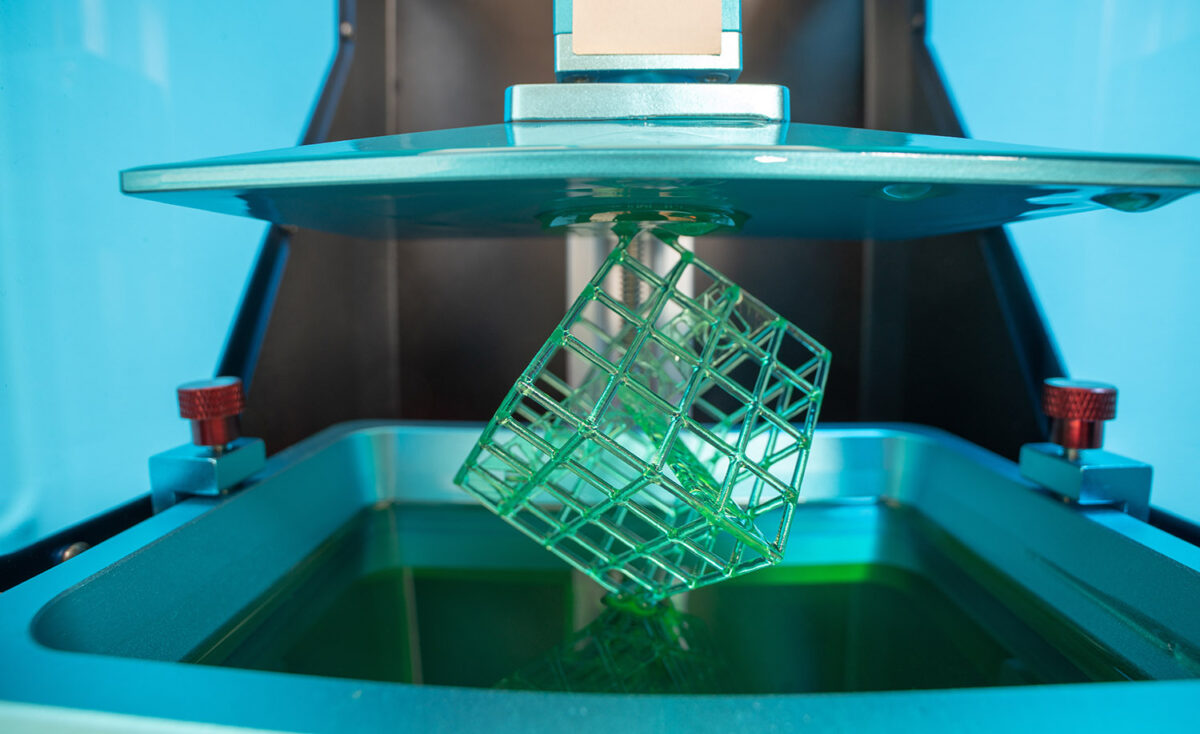
Dual-curing represents an innovative approach that enhances control over the final properties of parts through a multistage curing process.
Additive manufacturing has evolved significantly over the past few decades, with fused deposition techniques leading the way in thermoplastics processing and stereolithography in thermosets. However, these technologies primarily focus on producing custom parts and small series. Moreover, some techniques encounter challenges in part functionality. This includes variations in mechanical properties due to anisotropy, porosity, geometrical accuracy, and aesthetics.
You can also read: Swiss Researchers and MIT Spin-off Develop Way to 3D Print Slow-curing Polymers
The Need for Dual-Curing
In stereolithography, a nonuniform degree of curing can compromise part strength, as uneven mechanical properties may emerge along the printing direction. Traditional curing methods, like UV light, often fail to penetrate the deepest layers, causing incomplete cures that can lead to shrinkage and distortion.
Exploring the Concept
Dual-curing merges two polymerization processes within a single thermosetting formulation, activating them either simultaneously or sequentially with selective triggers like UV light and heat. This approach effectively cures unexposed areas in photopolymerization processes, particularly at elevated temperatures.
Innovative Case Studies
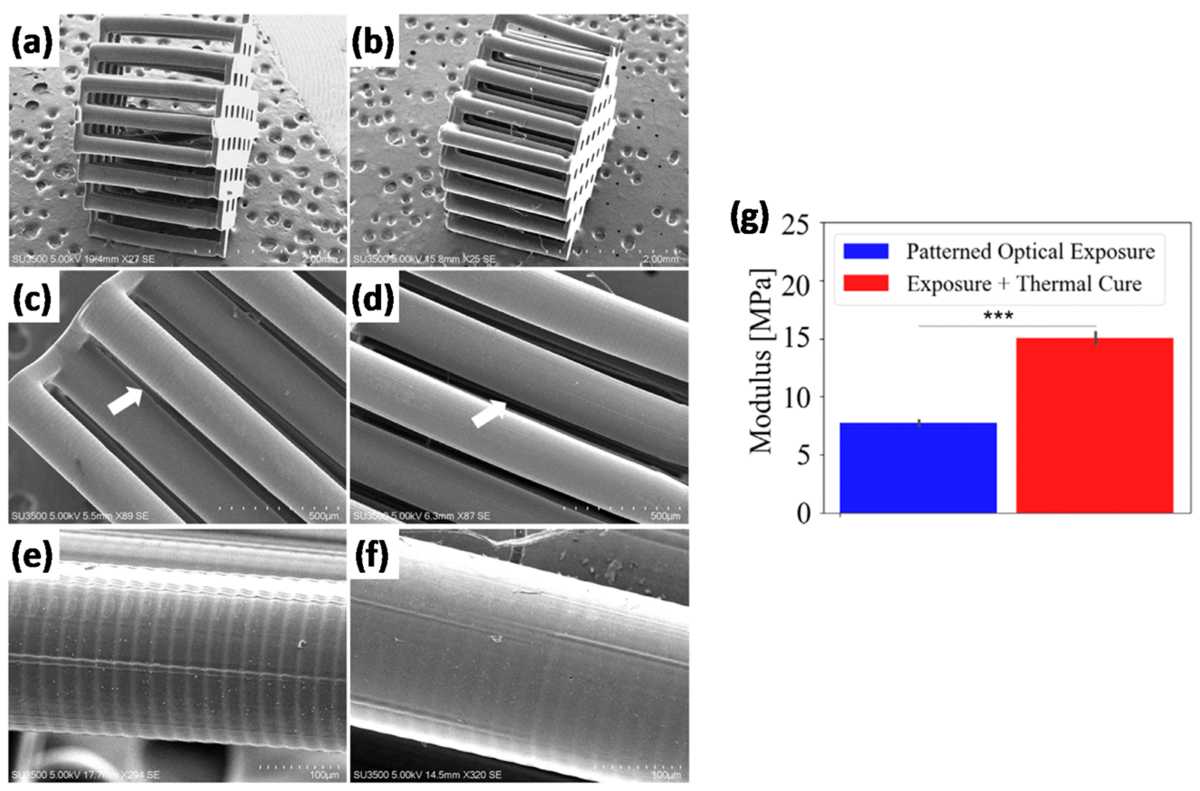
(a–f) SEM images for multilayer 3D printed parts fabricated via SL: (a,c,e) photo-cured structure compared to (b,d,f) thermally postcured multilayer samples; the arrows in (c,d) identify the pillar structure shown in (e,f). (g) Effect of thermal treatment on the mechanical properties of the multipillar structure. Courtesy of Understanding and Improving Mechanical Properties in 3D printed Parts Using a Dual-Cure Acrylate-Based Resin for Stereolithography. Link for Understanding and Improving Mechanical Properties in 3D printed Parts Using a Dual-Cure Acrylate-Based Resin for Stereolithography
Gupta et al. successfully applied dual-curing with a peroxide initiator in an acrylate/methacrylate-based stereolithography formula, observing up to a 30% increase in strength after thermal post-curing, thanks to the polymerization of residual monomers.
Zhang et al. introduced a second treatment for 3D-printed parts involving material structure rearrangement through bond exchange transesterification reactions, instead of a secondary polymerization. Using a suitable catalyst at high temperatures, this method further crosslinks the material’s network during post-treatment, markedly boosting mechanical properties and achieving equilibrium conditions. This technique also provides the materials with welding, healing, and recycling capabilities, setting them apart from other 3D-printed materials.
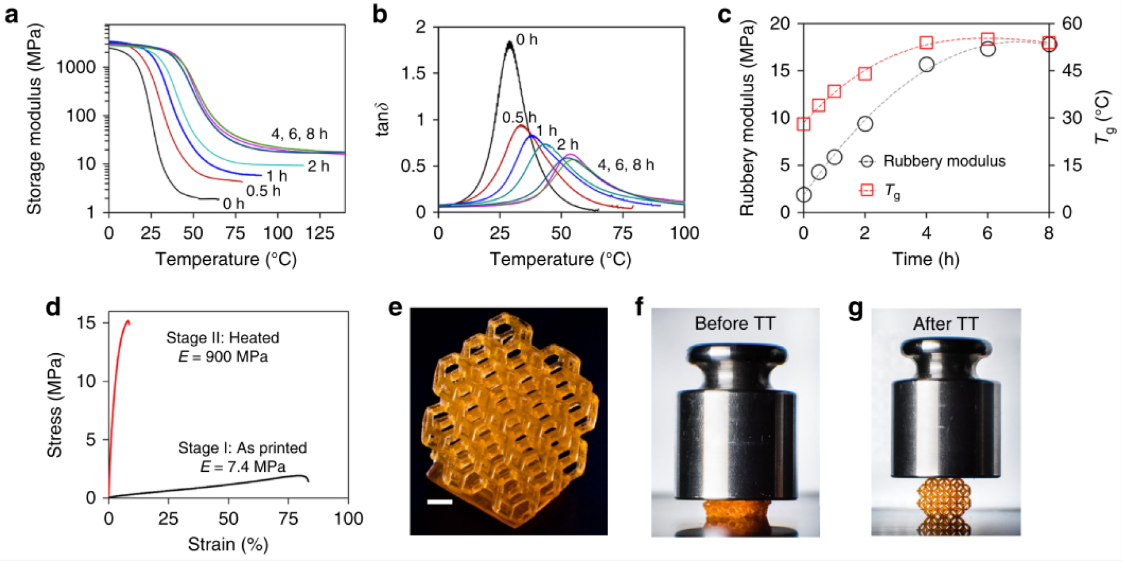
Demonstration of changes in stiffness of 3D printed thermosets caused by transesterification reactions leading to network structure rearrangement. Courtesy of Reprocessable thermosets for sustainable three-dimensional printing. Link for Reprocessable thermosets for sustainable three-dimensional printing : https://www.nature.com/articles/s41467-018-04292-8
Future Directions
DC presents a promising solution to the limitations of various additive manufacturing techniques, especially in stereolithography. Advancements in this area are crucial for improving printing quality and mechanical properties. By continuing to innovate in dual-curing processes, manufacturers can overcome the existing hurdles of mass production, paving the way for broader applications and the realization of additive manufacturing’s full potential.