Advancements in 3D Printed Hybrid Composite Structures
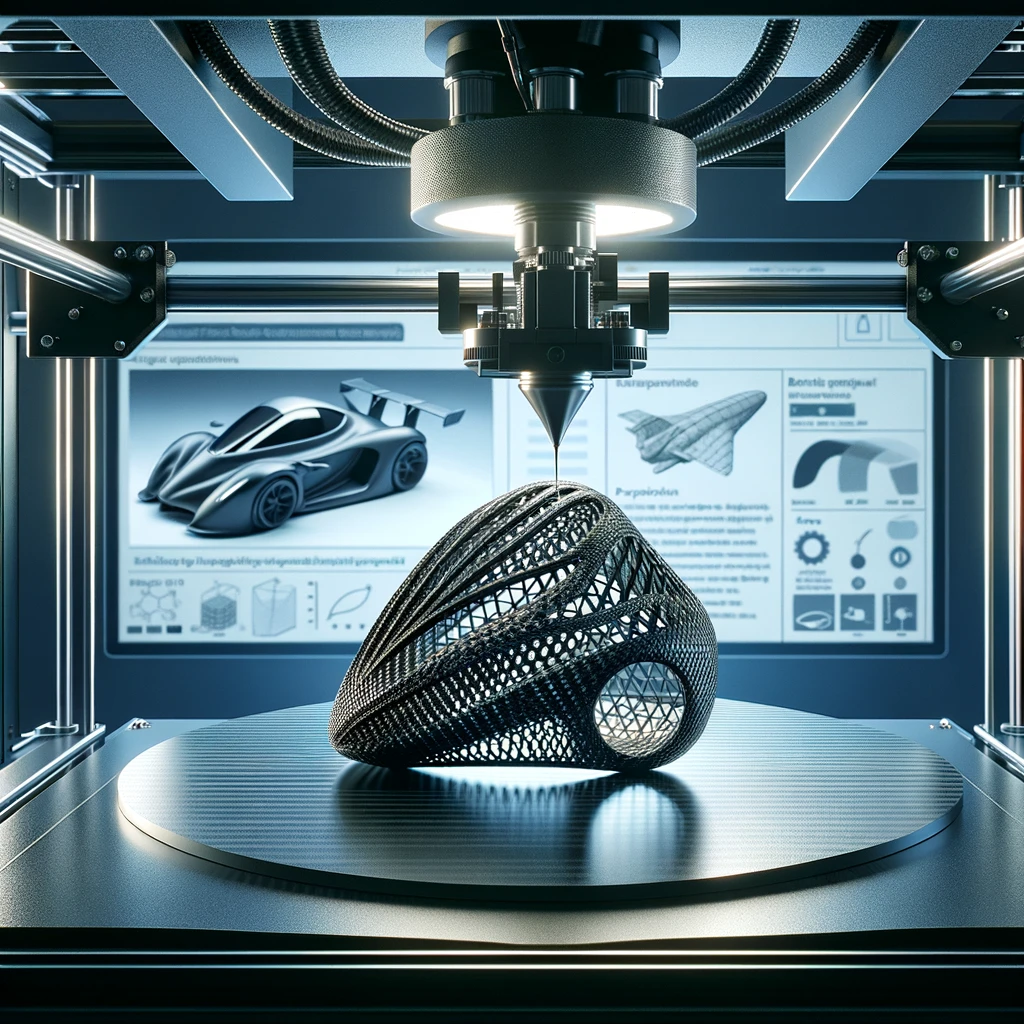
The need to lower the steep costs of traditional manufacturing, involving expensive tooling and molds, makes advancing composite manufacturing a key research focus.
Designers and engineers are increasingly exploring high-performance and lightweight design solutions, driving the adoption of complex geometries and composite materials. An innovative approach integrating 3D printing technology with hybrid composites is transforming composite manufacture.
You can also read: AI-Driven Carbon Fiber
Hybrid Composites: Forefront of Material Innovation
Merging multiple fillers to enhance mechanical performance and reduce weight stands at the cutting edge of material innovation. While glass fiber (GF) remains dominant in industrial applications, other fibers have evolved to address technical challenges.
Carbon fibers (CFs) emerged in the late twentieth century as a popular replacement for metallic components in automotive, aerospace, and other industries. Aramid fibers, which are valued for their thermal stability, find use in ballistics, automobile hoses, and high-temperature materials. Basalt fibers are gaining popularity in civil engineering and nuclear power plant building. Ceramic and boron fibers serve specialized, high-temperature applications, adding to the wide landscape of fiber-reinforced materials.
Developing insights into modern composites involves correlating processes, structure, and properties, understanding their mechanical, heterogeneous, and anisotropic features, and mastering 3D printing techniques.
Advancing Developments Using Machine Learning
Researchers have investigated traditional statistical methods like the design of experiments (DOE) and theoretical approaches, encountering challenges due to their reliance on extensive experimental tests and a narrow emphasis on significant traits. Theoretical modeling, which includes continuum mechanics and micromechanical models, provides information about phenomena like stretch-induced softening and anisotropic damage parameters. Despite major attempts, obstacles remain, especially when dealing with various fillers or experimental uncertainty.
Developing computational approaches, particularly those involving advanced machine learning (ML) algorithms, are transforming the research of composites. Ranging from nanoscale interface mechanics to macroscopic structural designs.
Recent studies in “Composites Part B: Engineering” reveal data-driven machine learning surpasses traditional analysis of composite mechanisms in additive manufacturing. Specifically, algorithms like Convolutional Neural Networks excel at deriving microstructural details from experimental data.
Applications of 3D Printed Hybrid Composite Structures
The Polymer Engineering Center, the University of Wisconsin, and the University of North Carolina led a research project that created a carbon fiber reinforced composite bike saddle to showcase an innovative hybrid composite manufacturing process. This process involves utilizing a dual curing 3D printed epoxy to fabricate the final part geometry, combined with the co-curing of pre-impregnated carbon fiber reinforcement.
The result is a bike saddle optimized, designed, and manufactured in less than 24 hours, all without the need for traditional tooling. This approach not only accelerates production but also offers greater flexibility and efficiency in designing and producing high-performance composite components.
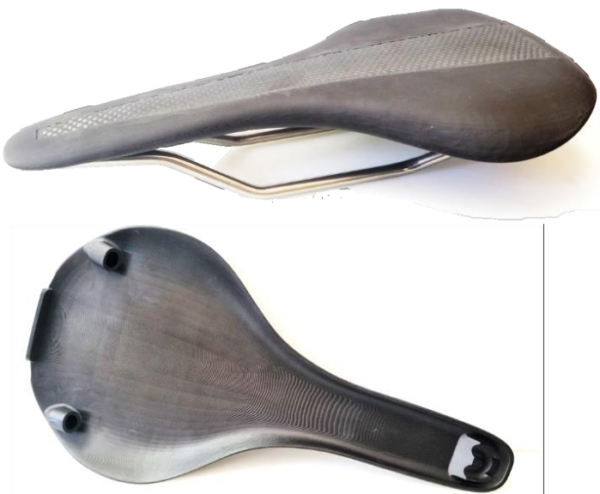
Epoxy-carbon fiber hybrid structure with a complex geometry bike saddle. Courtesy of Polymer Engineering Center, University of Wisconsin, and the University of North Carolina.
Composite materials find diverse applications, notably in aerospace and structural engineering. Moreover, addressing challenges like deltoid gaps in sharp-angled structures ensures proper load transmission in configurations such as spar/wing skin assemblies.
Meanwhile, partnerships with research institutes explore the potential of fiber-reinforced composites for lightweight truss structures, aligning with resource-efficient construction trends. Innovative winding processes autonomously join composite profiles, offering flexibility and collision-free production of closed-frame structures. Combined with development materials such as EPX82 joining elements, these technologies enable cost-effective mass production of lightweight composite truss structures, facilitating their adoption across various industries.