Dual-Wavelength Light Approach Speeds Vat-Based 3D Printing
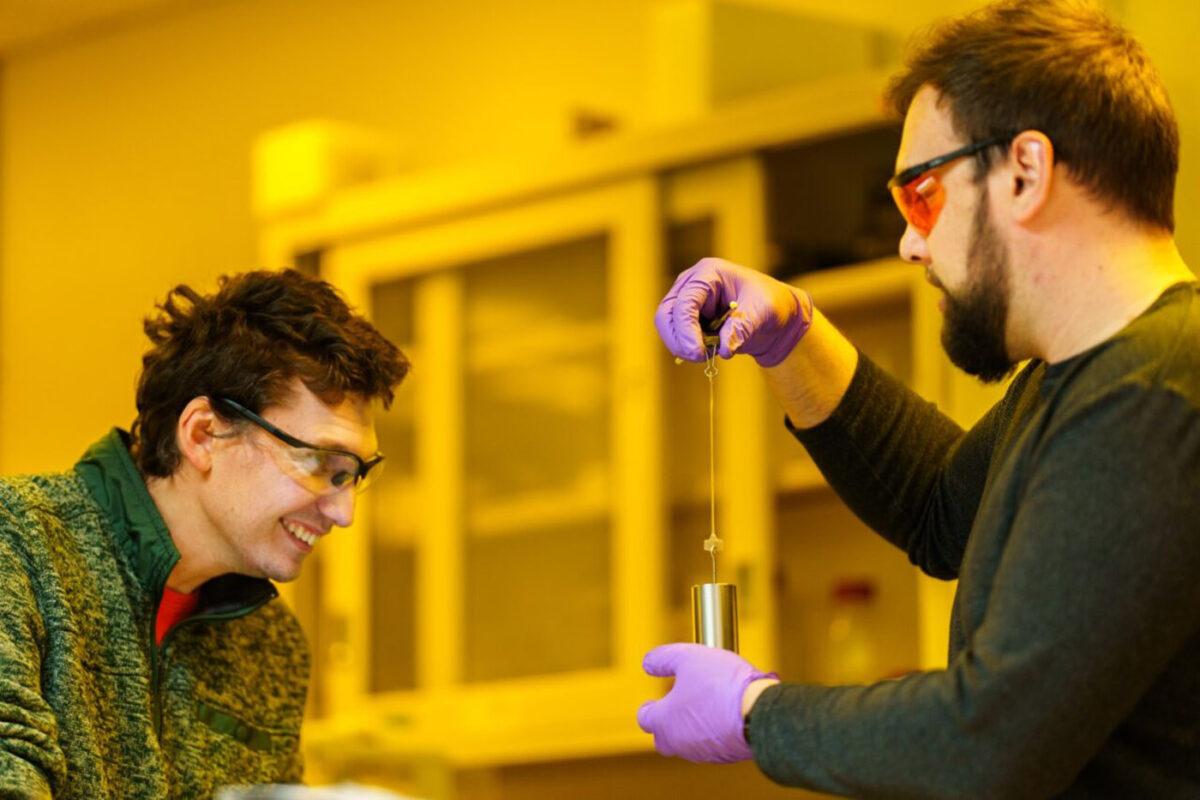
Sandia researchers say their use of faster-polymerizing DCPD allows the use of more resins, yielding stronger, more durable 3D-printed parts.
Researchers at Sandia National Laboratories have developed a new 3D printing process that uses dual-wavelength photocuring. The process can print stronger nonmetallic materials five times faster than traditional stereolithography (SLA) or digital light processing (DLP) methods.
You can also read: Laser Printed Polymers: 3D Printing without Solvents
A team of chemists and materials scientists at Sandia’s headquarters in Albuquerque, N.M., says this new approach uses new resin chemistries as well as dual-wavelength light. Doing so allows them to rapidly create stronger, more durable, high-resolution parts.
They’re calling their new additive manufacturing (AM) process SWOMP, which stands for Selective Dual-Wavelength Olefin Metathesis 3D-Printing.
SWOMP Yields Stronger, Tougher Parts
“It opens up a whole new world of what you can build and what 3D materials can be used for,” said Samuel Leguizamon, a materials scientist leading the team.
Sandia claims this technology yields stronger, more durable parts than can be achieved today via SLA or DLP processes. This, they say, will enable the creation of custom-printed components with applications ranging from automotive, aerospace, membranes, or degradable materials.
Traditionally, Sandia explained, one does vat 3D printing by irradiating a vat of photosensitive liquid resin in a desired pattern. As the resin is exposed to light beneath the vat, the resin cures and hardens into a polymer layer. The printer then lifts the cured polymer and projects a new pattern beneath to cure subsequent layers.
This is where things literally can get sticky, however. As the polymer cures, it adheres to the previous layer and to the bottom of the vat. After each layer, the cured polymer must be slowly peeled from the vat to prevent damage, significantly slowing down the 3D printing process.
Implement AM’s David Tucker Weighs In
“The interface layer in the DLP or SLA printing is an area where technological innovation is improving the speed and quality of 3D printing,” explains David Tucker, an independent additive manufacturing expert who is co-founder and an instructor with SPE’s Implement AM.
He says the interface layer is where the printed object meets the surface that separates the polymer from the printing light source. The printed object will attach to the interface layer unless a strategy/method is used to prevent it (or reduce it) from sticking.
The industry has been using some innovative methods to tackle this challenge, Tucker said. These include using non-stick polymer surfaces and mechanically peeling the object from the build interface. This can be done by pulling the object up after each layer. Additionally, some manufacturers use a flexible membrane in conjunction with the mass of the polymer to drop the membrane down, separating it from the printed object.
Others are trying to solve this riddle using other approaches, Tucker notes. Innovations include the Carbon DLS process that uses an oxygen-permeable membrane to prevent the object from sticking to the interface layer. And then there’s the Viscous layer in the Azul printer. In this method, the polymer floats on a viscous fluid that prevents the object from touching the platform. This approach has a secondary advantage, as it can also remove residual heat due to the flowing of a liquid that removes excess heat and thermal buildup.
Use of Two Lights is Key to the Technology
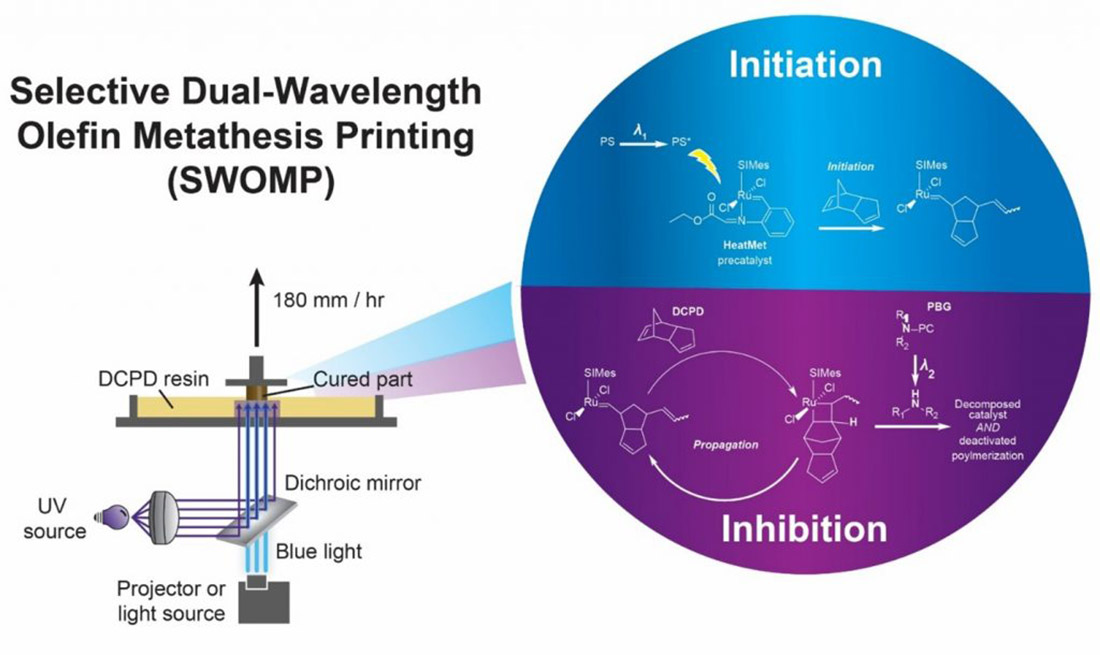
SWOMP uses two wavelengths of light simultaneously to change how certain materials are 3D printed. Graphic courtesy of Samuel Leguizamon, Sandia National Laboratories
Leguizamon, Leah Appelhans, former Sandia employee Jeff Foster and polymer scientist Alex Commisso created a way to cool the layers faster. They explained that the key to their invention is combining two lights –– ultraviolet and blue light.
The team says it was inspired by a technique known as continuous liquid interface printing (CLIP) along with a printing approach using dual-wavelength light for acrylic-based polymerizations.
With SWOMP, Leguizamon said, “You are still printing layer by layer, but you are using a second wavelength of light to prevent polymerization at the bottom of the vat. So it doesn’t adhere to the bottom. That means you can lift the cured polymer part more quickly and speed up the printing process significantly.”
Swapping Out Acrylic-based Materials for DCPD
Most vat polymerization materials tend to be acrylic-based, which lack the strength for many end-use applications. So the team experimented with dicyclopentadiene (DCPD), commonly used to produce paints, varnishes and flame retardants for plastics. They developed a way to polymerize it more rapidly with light so it can be used more efficiently in 3D printing.
“We changed building blocks of the materials from acrylic-based to olefin-based, which lets us print materials that are a lot tougher,” Leguizamon added.
The SWOMP technique, he noted, also significantly decreases waste and manufacturing time while increasing flexibility and cost-effectiveness.
A rapid three-month Exploratory Express program initially funded their work, but the Sandia Technology Maturation program is now contributing funding.
“What we are trying to do is build the toolbox of materials available,” Appelhans said. “We want designers, researchers, and engineers to be able to select the type of material they want to use.”
Sandia Seeking Collaborating Partners
One day, the team hopes to see these 3D-printed parts in rockets, engines, batteries and maybe even in fusion applications. Leguizamon said they’re already talking with Lawrence Livermore National Laboratory researchers to explore applications.
Sandia says it is seeking partners to develop and commercialize this technology. Learn more by contacting Sandia National Laboratories’ Licensing and Technology Transfer office. Go to https://ip.sandia.gov/opportunity/swomp for more information on licensing opportunities.