Leveraging AI to Speed Product Design Simulations
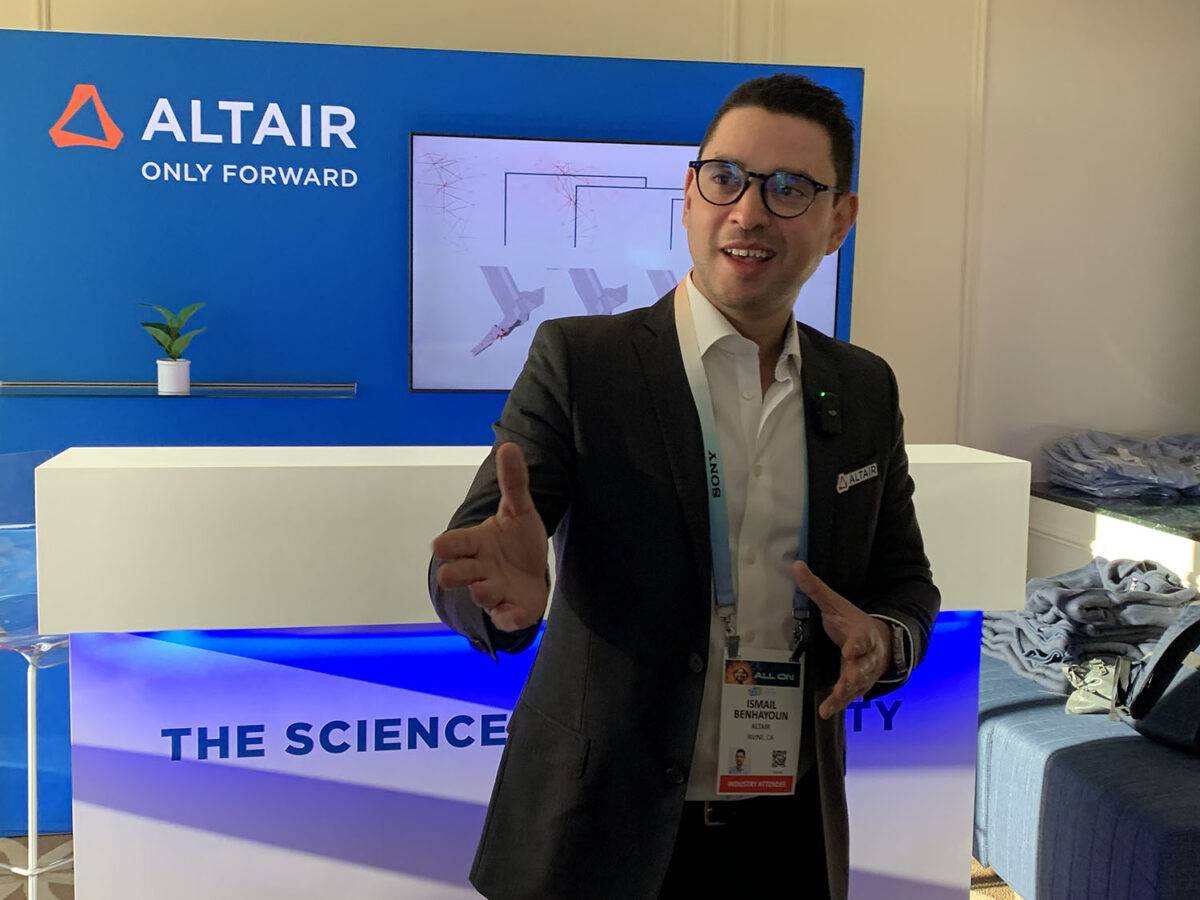
Altair software – from a ‘geometric deep learning’ tool to digital twins – is giving product developers powerful new weapons
Artificial intelligence is everywhere. That certainly was the case at the recent CES 2024 consumer technology trade show in Las Vegas, where exhibitors were touting their use of AI in everything from vehicle engineering to sporting goods and household appliances. David Byron, innovation strategy director at Michigan design studio Sundberg-Ferar, even used the term “AI washing” to draw attention to companies overhyping the technology.
But AI certainly is real and can bring huge benefits when employed properly. One company doing so is Troy, Mich.-based Altair Engineering Inc., which used a customer suite at the event to showcase its broad portfolio of software solutions for designers and engineers.
You can also read: AI for Enhanced Materials Development and Manufacturing
The 39-year-old firm’s physicsAI “geometric deep learning” package, for example, is helping product developers to speed the digital simulations of their designs significantly.
Using AI to Slash Simulation Time
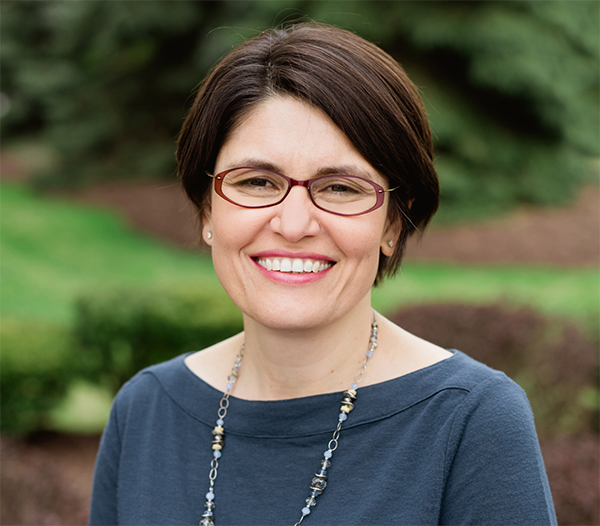
Dr. Fatma Kocer, Altair’s VP of engineering data science
Dr. Fatma Kocer, Altair’s vice president of engineering data science, said in a telephone interview after the show that this product allows a client to use existing simulation data to train a machine learning (ML) model. Once trained, this model can slash “what-if” simulation studies from months to days, she said. Traditional computer-aided engineering (CAE) programs are effective, but way too slow to satisfy most product developers.
“Once trained, physicsAI models can deliver predictions up to 1,000 times faster than traditional solver simulations, enabling teams to evaluate more concepts and make better design decisions.”
This AI-powered technology operates directly on mesh or computer-aided design (CAD) models to quickly produce fully animated physics outcomes across diverse physics applications. These fast physics predictions, noted Kocer, eliminate the time-consuming hand-crafting of parameters needed with other training methods.
Leveraging Digital Twins
Ismail Benhayoun, meanwhile, demonstrated another example of the company’s expertise in the Altair suite at CES. Benhayoun, Altair’s senior technical director for product design in the U.S., highlighted a coffee case study. Gruppo Cimbali SpA, an Italian maker of espresso coffee machines, uses Altair’s technology to create a precise digital twin of its machines. These allow Cimbali engineers to run simulations that improve both the appliance’s energy usage and fine-tune its design aesthetics.
The Physics Behind a Cup of Coffee
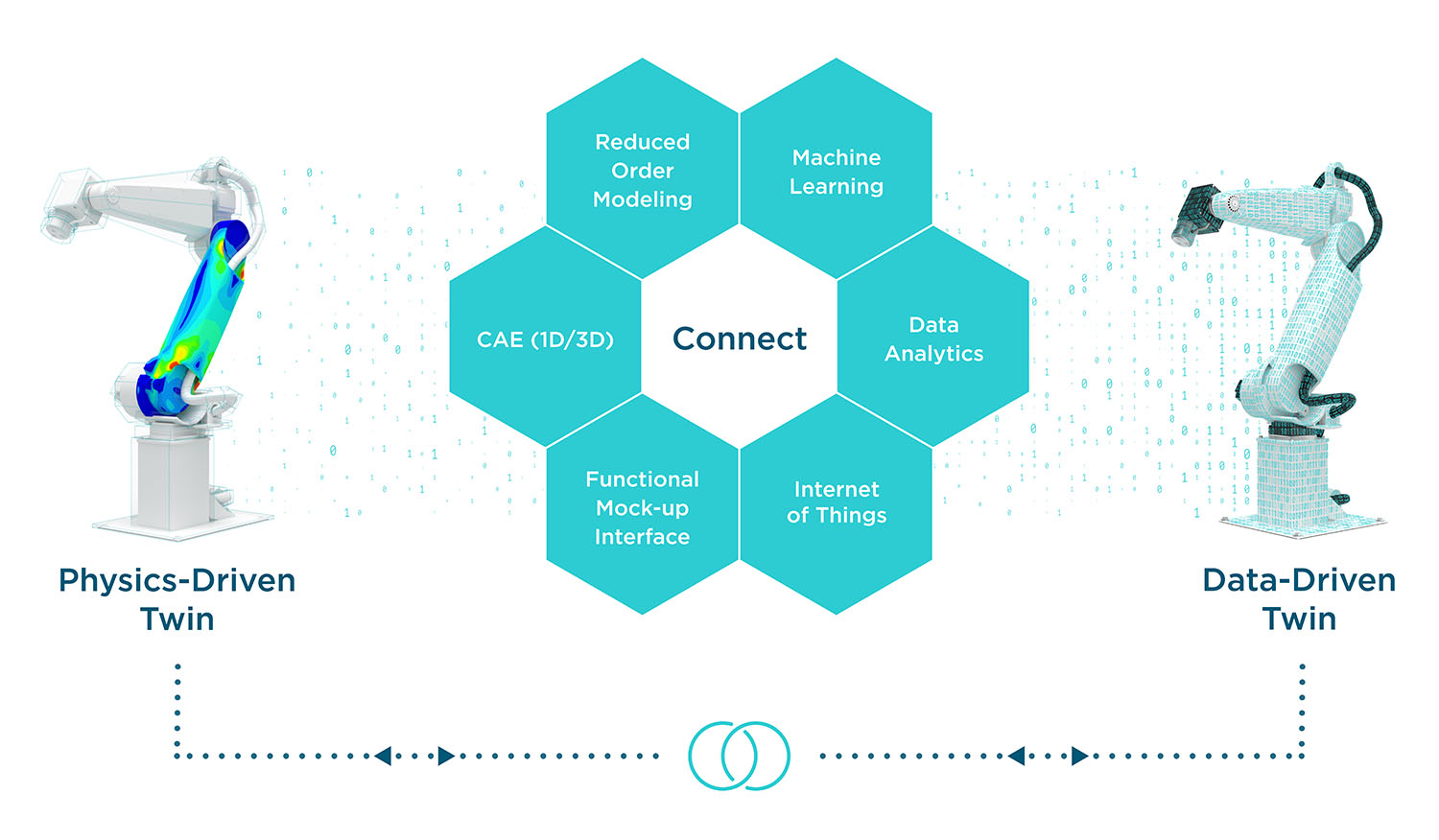
Altair’s DigitalTwin solutions are powered by its sophisticated AI, simulation, data analytics, and high-performance computing (HPC) software.
In this video, Luca Gatti, a Cimbali energy and sustainability expert, explains why they found it necessary to model and study the physics behind a cup of coffee.
Gruppo Cimbali used Altair TwinActivate software, which simulates the entire system and enables real-time digital twin deployment.
This video, meanwhile, features John Skabardonis, polycarbonates technical marketing manager for the electrical/electronics industry at Covestro LLC, interviewing Benhayoun at CES about Altair’s digital twin capabilities.
A Portfolio of Materials Data Resources
Altair also offers product lifecycle management software to model alternate materials that can help not only improve end-product performance but also enhance overall sustainability. The company describes its Material Data Center as a resource for engineers, designers and scientists. It has been developing in the area of material modeling for years but bolstered that when it acquired M-Base Engineering + Software GmbH in October 2020.
With its broader portfolio of software products, Altair aims to optimize the applied convergence of AI, data analytics, high-performance computing (HPC), Internet of Things (IoT) and simulation. As with the Cimbali example, a key part of this involves its significant digital twin capabilities. (Download its 48-page 2022 Digital Twin Global Survey Report here.)
With these tools, the firm says, teams can design, build, test, optimize, evaluate what-if scenarios, perform predictive maintenance, and extend the remaining useful life of their products –– all digitally — without needing physical prototypes.