Funding the Drive to Optimize rPET for Additive Manufacturing
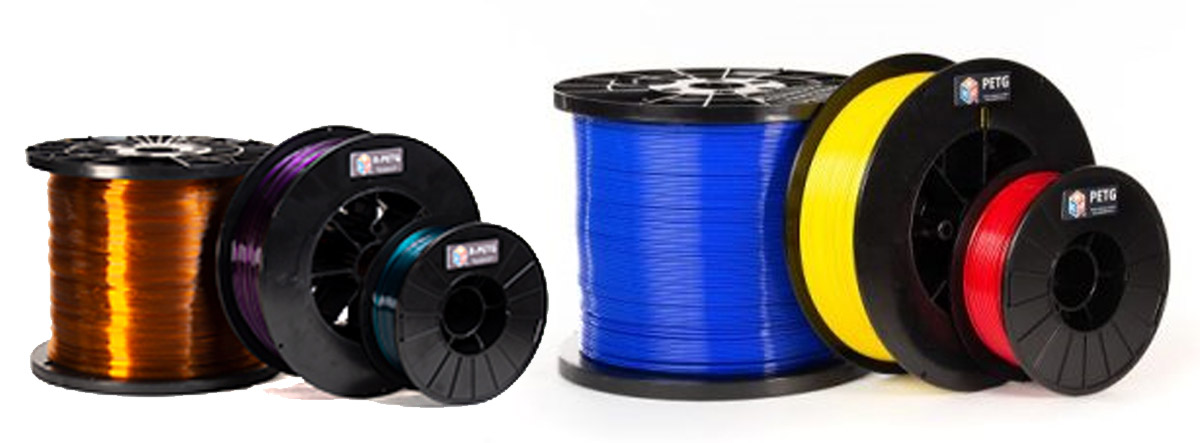
Prize from America Makes is designed to develop recycled PET for 3D printing.
A pair of U.S. defense-related organizations have awarded funds to a project designed to optimize recycled PET (rPET) and rPET-based composites in filament-fed material extrusion 3D printing.
The National Center for Defense Manufacturing and Machining (NCDMM) and America Makes, the national additive manufacturing innovation institute, recently announced that two winners will share their $1.2 million Environmental Additive Research for Tomorrow’s Habitat (EARTH) Project.
One winning project is examining “Powder and Process Optimization for Sustainable Additive Manufacturing” (POSAM), while the other aims to “Accelerate Additive in U.S. Department of Defense (DoD) Applications of High-Performance Recycled Polymers.”
This article focuses on the latter project. Currently, virgin thermoplastics are the primary feedstock for additive manufacturing (AM). America Makes notes the “urgent need to find ways to make recycled materials more user-friendly while maintaining consistent performance characteristics.”
Ohio Firm Spearheading The Effort
IC3D Inc., a Hilliard, Ohio-based company active in polymer filament production and 3D printing, is leading the rPET initiative. Its customers on this project are the U.S. Army Combat Capabilities Development Command (DEVCOM) Chemical Biological Center (CBC) and Army Research Laboratory (ARL). To advance this research, IC3D also is collaborating with Pennsylvania’s Harrisburg University and Ohio State University’s Center for Design and Manufacturing Excellence (CDME).
Polyester-based PET is known for its mechanical and thermal properties, including very good chemical resistance and dimensional stability. When used in additive manufacturing, however, the semi-crystalline nature of PET and rPET makes them prone to warping caused by changes in density brought on by the formation of crystalline regions.
That means that AM of rPET requires strict printing and ambient chamber temperatures to prevent distortions that compromise part quality, dimensional accuracy, and overall printability. Additionally, rPET requires a higher working temperature compared to other commodity 3D printing thermoplastic materials. The 3D printing industry has been slow to adopt PET due to these issues.
The goal: Develop Robust rPET Filament
Using funding from the EARTH Project, IC3D and its partners aim to develop and validate robust rPET and rPET-based composite materials suitable for filament-fed material extrusion 3D printing. The project will evaluate the suitability of various materials, compound novel materials, optimize printing characteristics, and perform material characterization and mechanical testing.
To ensure printability and enhance performance, the team plans to formulate novel rPET composites containing modifiers. “We will investigate two distinct modifiers to rPET –– two different thermoplastic elastomers (TPEs), and a pair of fiber additives: glass and carbon. In each case, the modifier acts to limit warpage in the material.”
U.S. Army Unit Provides Data on Test Parts
Using Design of Experiments (DOE) methodologies, the team will refine printing parameters and investigate the mechanical and thermal properties of the developed materials. U.S. Army DEVCOM has provided 3D data on two sets of parts –– one highly detailed and the other easier to print –– for potential case studies.
The team says it will conduct demonstrations of the optimized rPET material for each of those use cases. The goal is to pave the way for comprehensive technical, economic, and sustainability evaluations. The project’s technical period will cover the next 21 months, with an additional three months allowed for reporting.
The Effort Aims to Bolster U.S. Supply Chain
Youngstown, Ohio-based America Makes says this program “will immediately impact the growth of the domestic U.S supply chain,” as IC3D intends to commercialize an rPET material informed by the findings of this program.
The EARTH Project was funded by the Office of the Under Secretary of Defense, Research and Engineering Manufacturing Technology Office and the Air Force Research Laboratory.
NCDMM notes that its mission is to drive manufacturing technology and process advancements throughout the DoD to ensure the U.S. warfighter always has a superior advantage. It manages America Makes as one of its programs.