Advancements in LDPE Synthesis and Recycling
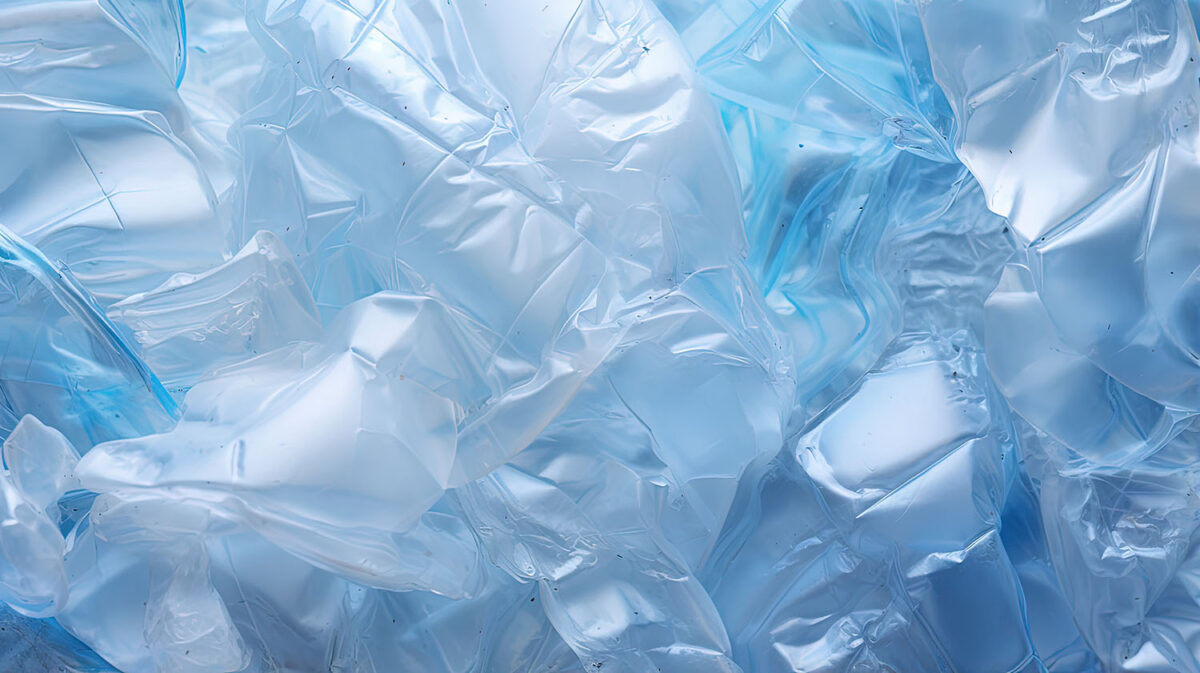
Low-density polyethylene (LDPE), a pivotal plastic, is conventionally manufactured under extreme conditions, featuring robust aliphatic C─C bonds that hinder effective recycling. Despite its widespread use in packaging, merely 5% of LDPE is recycled due to its high-pressure (2,500 to 4,000 bar) and high-temperature (250°C) production requirements.
Innovative LDPE-Mimic Development
Addressing these challenges, scientists at Universität Bayreuth, Germany, pioneered a low-pressure and low-temperature synthesis process to mimic LDPE’s chemical structure while enhancing its recyclability. Employing coordinative chain transfer polymerization (CCTP), they synthesized two macromonomers closely resembling commercial LDPE under mild conditions (2 bar and 70°C).
Key Findings and Significance
Prof. Rhett Kemp, leading the study, emphasized the novel catalysts’ role in producing defined building blocks conducive to LDPE-mimic synthesis. The resulting material, LDPE-mimic, comprises a backbone and potential long-chain branches, facilitating reversible attachment and cleavage under acidic and basic conditions. Introduction of ‘recycled points’ via ester linkages further streamlines polymerization and depolymerization, enhancing LDPE-mimic’s recyclability and solubility in organic solvents.
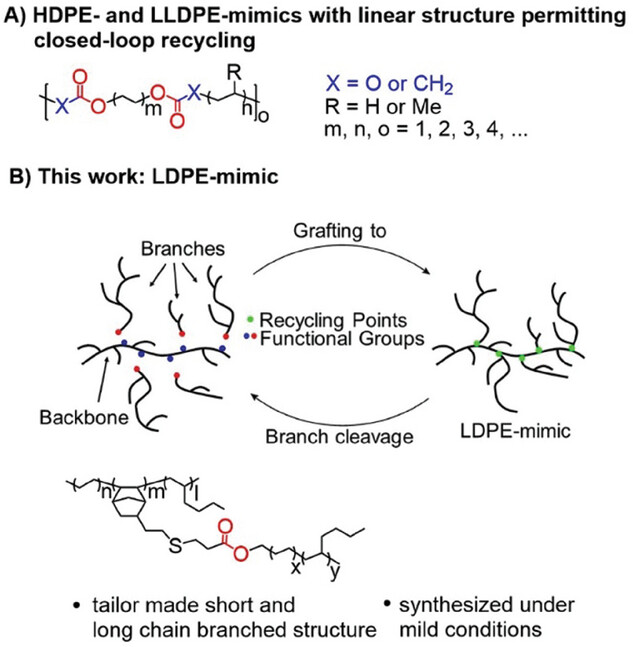
State-of-the-art regarding polyethylene mimics and the work presented here. A) High-density polyethylene (HDPE) mimic or linear low-density polyethylene (LLDPE) mimic based on bio-based, propylene- or (poly)ethylene-based feedstock. B) Structural and functional low-density polyethylene (LDPE) mimic with recycle points introduced here.
Assessment against commercial Lupolen LDPE 1800P revealed LDPE-mimic’s similarity in melting point, density, crystallization temperature, and tensile behavior. Notably, the integration of recycled points did not accelerate thermal decomposition, affirming LDPE-mimic’s viability for sustainable plastics engineering.
Implications for Sustainable Plastic Engineering
This breakthrough offers a promising pathway to enhance LDPE’s sustainability profile, reducing energy-intensive production and promoting circularity through improved recyclability. By leveraging innovative synthesis methods and recyclable points, the industry can advance towards a more sustainable future in plastics engineering.
You can learn more in ‘A Closed-Loop Recyclable Low-Density Polyethylene,’ recently published in Advanced Science.