Sidel’s new bottle base design helps enable production of all-rPET bottles for carbonated soft drinks
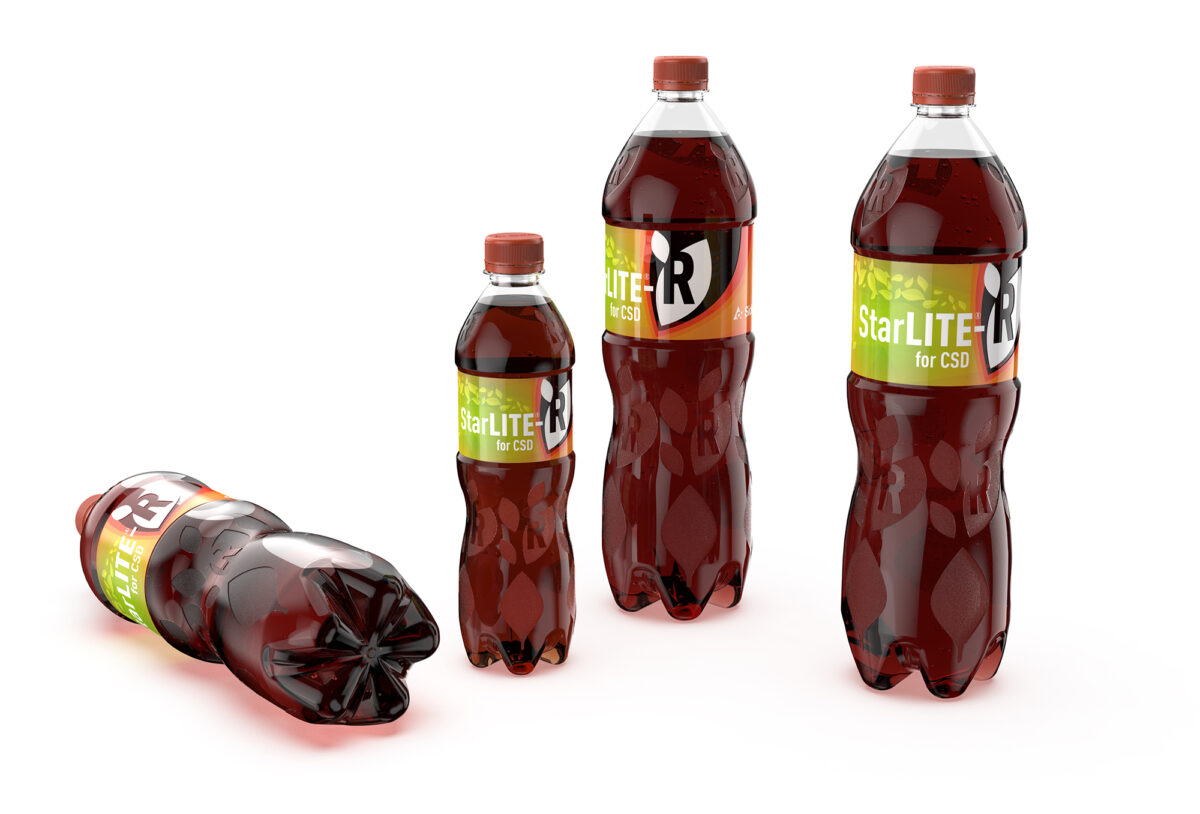
New StarLITE R bottle said to offer wider processing window of recycled PET for blow molders
Blow molding machinery maker Sidel has launched a 100 percent recycled PET (rPET) bottle base for carbonated soft drinks. Called StarLITE R for CSD, it represents an addition to its existing StarLITE family of PET bottles and base designs.
The Switzerland-based company, part of the Tetra Laval Group, notes that the variability of rPET resin has become a major challenge for the packaging industry. But it says its expertise in working with the material has allowed it to develop a solution that meets both resin variability and CSD bottle requirements. Sidel calls the new product “an important breakthrough that offers greater protection against deformation, increased resistance to bursting and optimum stability, thereby ensuring a transition to rPET bottles with no fear.”
It attributes the advances to various factors, to include improved process technology and mold base design; ultra-efficient bottle base cooling; and what it calls seamless production transition.
Laurent Naveau, packaging innovator leader at Sidel, noted the challenges that rPET resin can present to the packaging industry: “The characteristics of rPET are impacted by several factors. Firstly, by seasonality. Consumption habits fluctuate over the course of the year impacting the product category mix. And secondly, by different PET collection models which means that post-consumer PET material bales will vary from region-to-region and even country-to-country.
“The recycling process and equipment used will also influence PET resin,” Naveau said. “All these factors can pose new challenges for manufacturers looking to produce bottles with rPET content.”
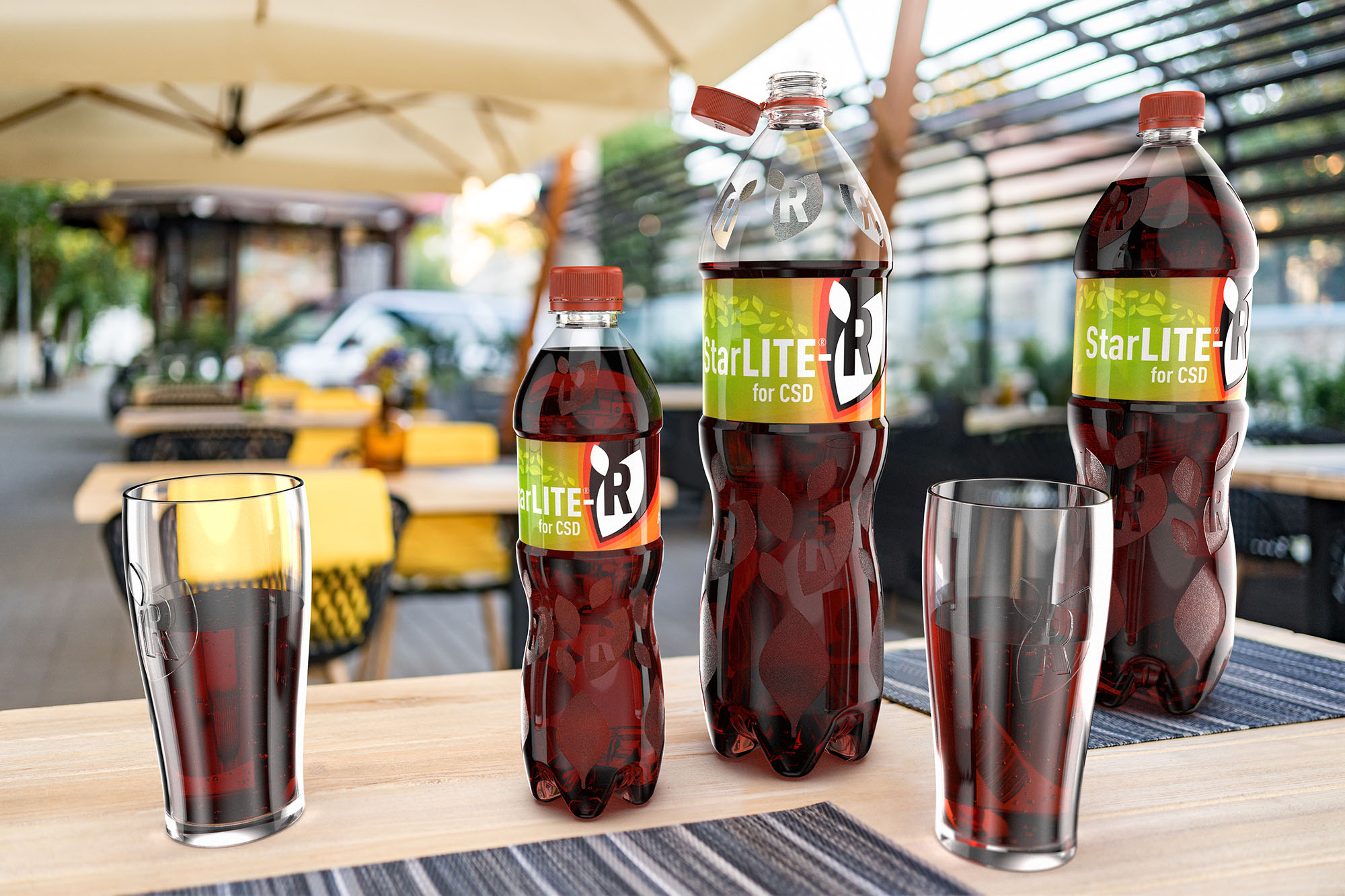
Sidel applied its 45 years of experience in both blow molding and PET packaging to create this new family of StarLITE R bottles. Courtesy of Sidel
Common CSD bottle manufacturing challenges include such issues as stress cracking, roll out and bursting during blowing. Additionally, a higher temperature is needed to process rPET, which can cause packaging manufacturers to have less control over the rPET material during the blow molding process.
Greater variability in rPET resin typically leads to a narrower process window and lower bottle quality. Sidel has tackled this problem with its new StarLITE R base, which it says helps to restore a much wider process window. The new design is easier to blow as it can be done within a wider range of parameter settings.
The new mold base profile is said to allow for excellent material distribution through advanced stretching and a high base clearance for optimum stability. The advanced stretch rod end design has improved the preform end-cap material stretching and ensures accurate injection gate centering on the bottle. And finally, a carefully calculated combination of grooves and venting holes is said to allow for high-precision base feet formation.
The new bottle also uses dual external and internal bottle base cooling to ensure a consistent shape. “Externally,” notes Sidel, “the process uses a mold base cooling circuit that focuses on the warmer bottle base zones and internally a hollow-stretch rod requiring no additional air supply is used.”
It adds that the StarLITE R can be easily installed on existing production lines and adapted to fit current bottle designs. The product is compatible with Sidel’s primary blow molding machines, including the EvoBLOW, Universal and Series 2 and is suitable for high-speed production.