Novel Process Affordably Turns Waste Plastic Into ‘Green’ Hydrogen
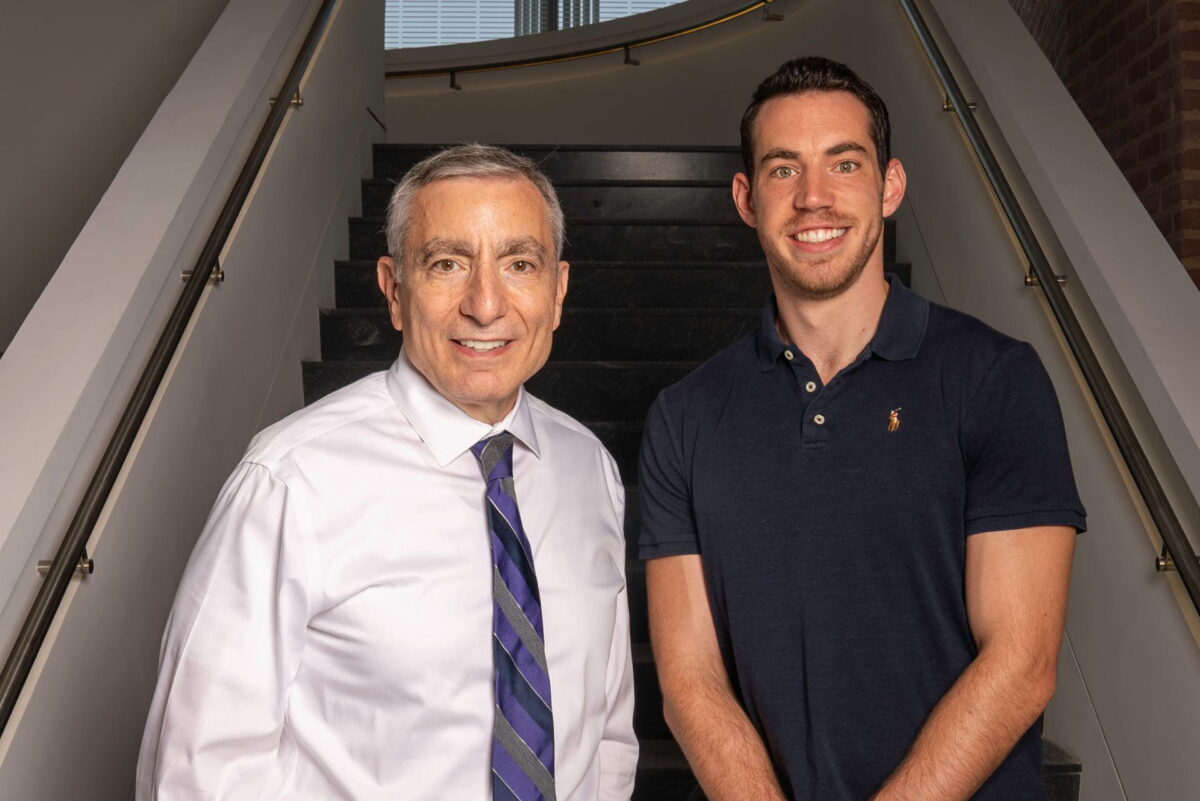
Rice University researchers say “rapid flash Joule heating” yields H2 and high-value graphene
Researchers at Rice University in Houston say they have found a way to harvest green hydrogen –– a sustainable alternative to fossil fuels –– from plastic waste using a low-emissions method that could more than pay for itself. Current methods to produce hydrogen are said to either be too expensive or to generate too much carbon dioxide.
The newly developed process yields high-value graphene as a byproduct that if sold on the market could more than offset the production costs, according to Kevin Wyss, a Rice doctoral alumnus and lead author on a study published in the journal Advanced Materials.
“In this work,” Wyss says, “we converted waste plastics –– including mixed waste plastics that don’t have to be sorted by type or washed –– into high-yield hydrogen gas and high-value graphene. If the produced graphene is sold at only 5 percent of current market value … clean hydrogen could be produced for free.”
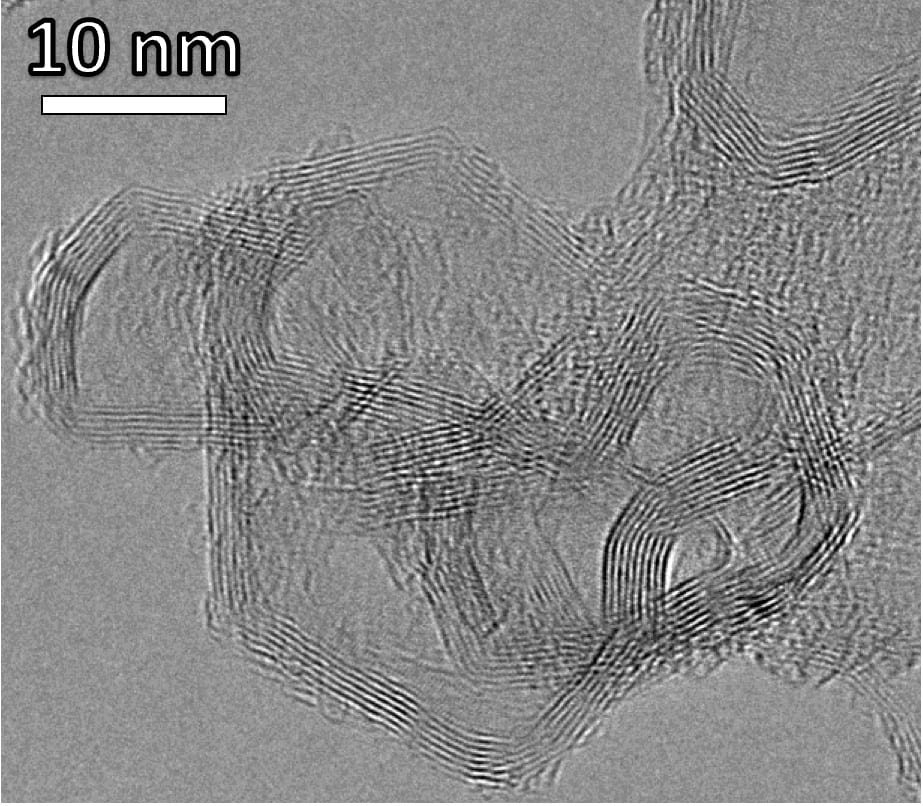
Transmission electron microscope (TEM) image of layered stacks of nano-scale flash graphene sheets formed from waste plastic. Courtesy of Kevin Wyss/Tour lab
Hydrogen gas (H2) is the primary storable fuel for pollution-free energy production, with more than 90 million metric tons used globally each year. More than 95 percent of H2 is synthesized through metal-catalyzed steam methane reforming that produces 11 metric tons of CO2 per ton of H2. By comparison, “green H2” from water electrolysis using renewable energy releases no CO2, but costs up to three times more to produce, making it currently economically unviable.
‘Gray’ vs. ‘green’ hydrogen
“The main form of hydrogen used today is ‘gray’ hydrogen, which is produced through steam-methane reforming” and churns out a lot of CO2, said James Tour, Rice’s T. T. and W. F. Chao Professor of Chemistry and a professor of materials science and nanoengineering. “Demand for hydrogen will likely skyrocket over the next few decades, so we can’t keep making it the same way we have up until now if we’re serious about reaching net zero emissions by 2050.”
The researchers exposed plastic waste samples to rapid flash Joule heating for about four seconds, bringing their temperature up to 3,100 degrees Kelvin (or 5,120 degrees F). The process vaporizes the hydrogen present in plastics, leaving behind graphene –– an extremely light, durable material made up of a single layer of carbon atoms.
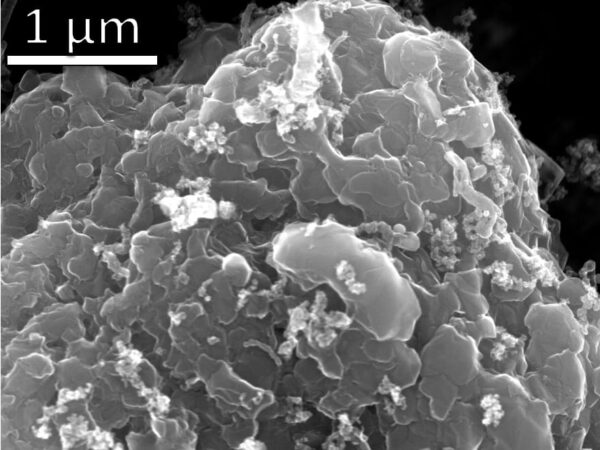
Scanning electron microscope (SEM) image of layered stacks of nano-scale flash graphene sheets formed from waste plastic. Courtesy of Kevin Wyss/Tour lab
“When we first discovered flash Joule heating and applied it to upcycle waste plastic into graphene,” Wyss explained, “we observed a lot of volatile gases being produced and shooting out of the reactor. We wondered what they were, suspecting a mix of small hydrocarbons and hydrogen, but lacked the instrumentation to study their exact composition.”
The university obtained funding from the U.S. Army Corps of Engineers to buy the equipment needed to characterize the vaporized contents.
“We know that polyethylene, for example, is made of 86 percent carbon and 14 percent hydrogen,” Wyss said, “and we demonstrated that we are able to recover up to 68 percent of that atomic hydrogen as gas with a 94 percent purity. Developing the methods and expertise to characterize and quantify all the gases, including hydrogen, produced by this method was a difficult but rewarding process for me.”
The Rice researchers’ study states that a life-cycle assessment has yielded a 39-84 percent reduction in emissions compared to other H2 production methods, suggesting the flash H2 process to be “an economically viable, clean H2 production route.”