Electronification of Medical Devices Creates Markets for Plastics
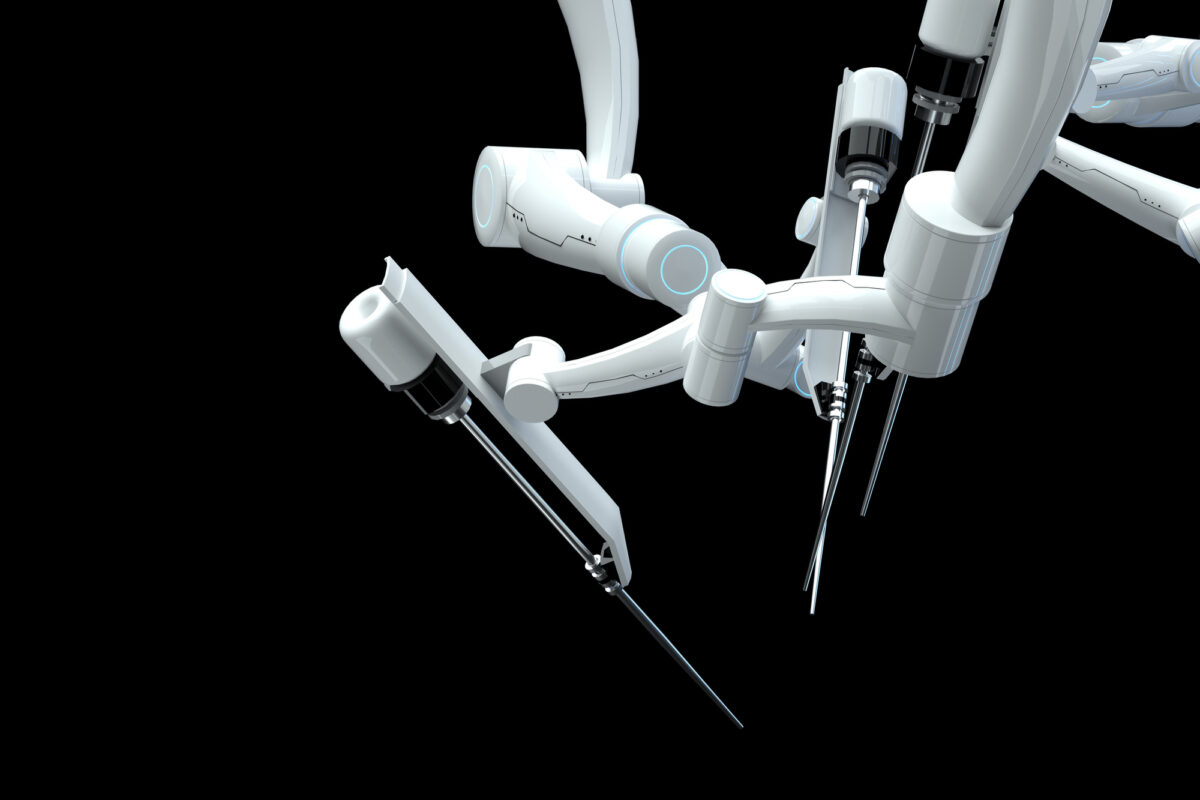
Automation-rich components benefit from advanced electronics and plastics process capabilities
First of a three-part report
Medical technology and medical plastics are entering a new world of device manufacturing and use that relies on the benefits of high-tech electronics, robotification of surgical procedures and remote monitoring of implanted sensors to promote patient health.
A feature of this evolving market is the growing electronification of medical devices, an automation-rich capability that will be a catalyst in doubling the size of the medical device industry in the not-too-distant future, according to Neal Walters, a partner at the global management consulting firm Kearney.
Medical Devices Benefit From High-Tech Electronics
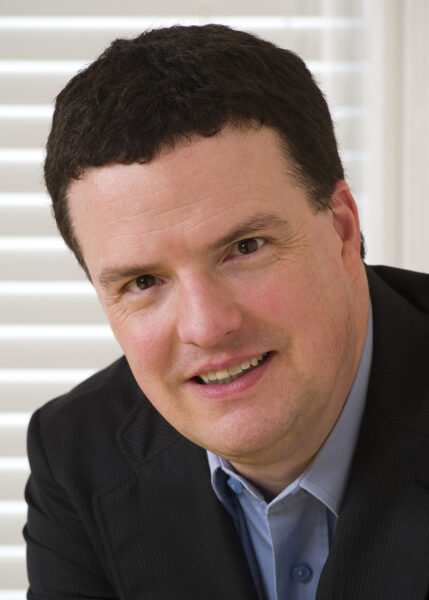
Neal Walters, partner, Kearney.
In an interview with Plastics Engineering, Walters said that the electronification of advanced medical devices is part of a total $1 trillion growth market for high-tech and micro-sized electronics that includes applications like electric vehicles and autonomous driving systems, this last being the ultimate goal of vehicle automation.
He added that a small but growing group of OEMs, contract manufacturers and visionary startups will profit most from the development and use of advanced medical devices whose technologies are made possible with electronification and the automation it delivers. The reason for this is the extreme dimensional accuracy and placement precision that these devices must have—capabilities that only a few manufacturers have the technology and capital to develop.
The fabrication capabilities required for many plastics components of robotic devices are thus extraordinary by themselves, as well as essential for successful surgery. Processes such as injection molding, micro injection molding and 3D printing will play important roles in integrating ever-smaller electronics with robotic parts. The low-volume, highly custom capabilities of 3D printing will be especially important in developing complex part shapes for small spaces in electronic applications.
Accuracy and Speed of 3D Printing Fit Product Needs
If 3D printing can bring the accuracy for patient-specific applications, Walters said, it will create demand for the process as a fabrication option. As an example, he cited orthopedic devices where surgeons typically bring multiple sizes of implants to an operating room and decide, based on x-rays and other data, which size to use. “I can envision a future where use of accurate scans generates a patient-specific device in-situ, or close to it,” he said. In New York City, there could be one center that works with a hospital in rapidly printing a device based on measurement data taken from a patient, Walters said.
In future reports Neal Walters will describe how electronification of medical devices will affect surgery, patient recovery and long-term wellness. He’ll also look at what will be required of the plastics that are specified for use with robots.