Polymer Resources Adds Capacity to Satisfy Demand for Engineering Compounds
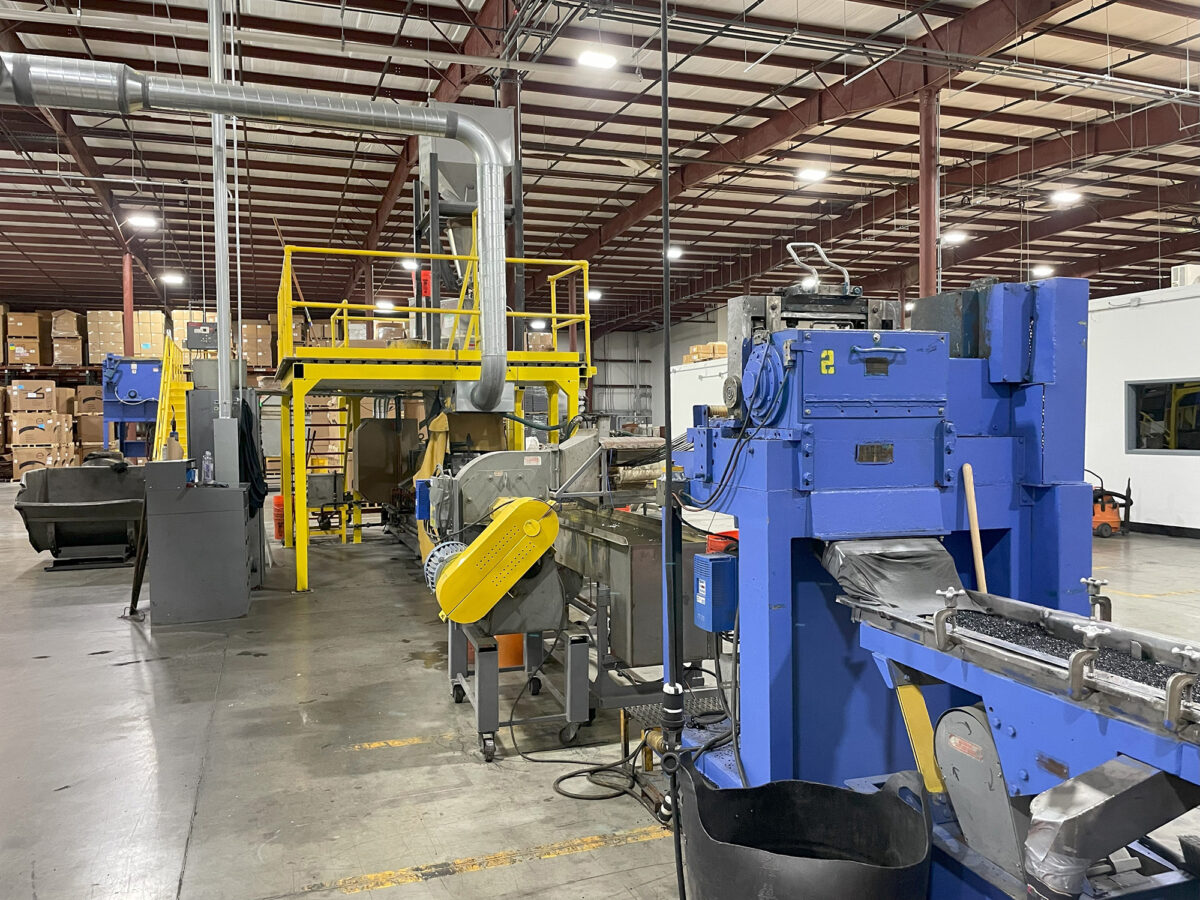
New extrusion line and larger plant help company meet growing sales demand
Scott Anderson has crossed a lot off his to-do list. The president and chief operating officer of engineering resins compounder Polymer Resources Ltd. (PRL) expanded capacity at company headquarters in Farmington, Conn., and at a second location, in Rochester, N.Y.; added plant and office space in Rochester; and is working toward ISO 14001 certification as a sustainable business.
As reported on Aug. 15, the company is broadening its line of sustainable compounds that contain 50 percent or more recycled content and eyeing a capacity expansion in 2024 with addition of another twin-screw compounding line in Rochester.
The company owns land adjacent to its Rochester site which could accommodate a 100,000-square-foot building. “This will make expansion as easy as possible when we cross that bridge,” Anderson said. “We believe the current capacity is good through 2024.”
Despite Fluctuatuons, PRL Is Ahead of Its 5-Year Sales Plan
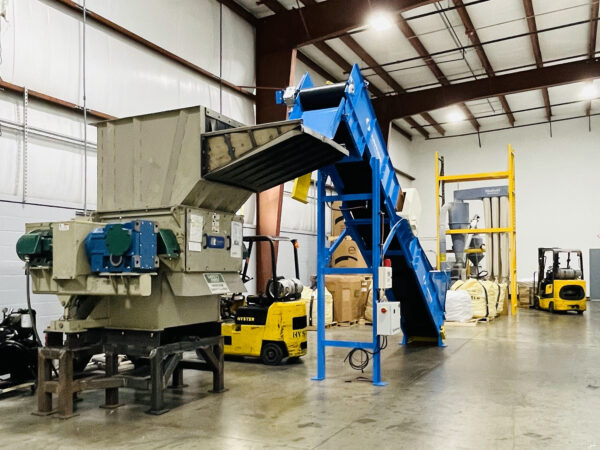
PRL’s expanded Rochester plant features increased grinding and shredding capacity for recycling plastics from in-plant and outside sources.
Operations overall look good, as well. “We’ve doubled business over the last five years,” he noted in a telephone interview. “We’re seeing a small pullback this year from too much inventory in the system,” an after-effect of the COVID pandemic, when demand for materials and plastics products drove up sales—and inventory—for suppliers. “Business is slowly coming back to reality now, but we’re still well ahead of our five-year plan.”
In the Rochester expansion, PRL said in a statement that it increased overall capacity 40 percent, largely through installation of a 65mm Coperion co-rotating twin-screw extruder that was in the Farmington plant. Anderson, who declined to reveal specific capacity figures, said the Coperion line makes four extruders in the Rochester plant: two single-screw lines—one 3.5-inch diameter and the other 4.5-inch diameter—and 40mm and 65mm co-rotating twin-screw lines.
PRL also increased the size of the Rochester plant to 60,000 square feet. The project expanded the footprint of the facility from 35,000 square feet, previously divided between two buildings, to 60,000 square feet in one building. This provided more space for compounding, shredding and grinding. The last two operations are a plus for recycling plastics scrap generated by PRL and other sources, as well as for storage, a laboratory and offices, and improved workflow.
The Farmington plant, meanwhile, installed a new Leistritz co-rotating 60mm twin-screw line that’s rated capable of processing up to 2,200 pounds per hour of engineering resins.
The company’s process flexibility allows it to deliver orders ranging from 250 pounds to truckload quantities. “The different extruders give us the capability to run different size batches,” he said.
Custom Color Matching Is a Major Part of PRL’s Business
According to Anderson, 60 percent of PRL’s business is custom color matching. “We’ve offered specific and highly accurate color matches for over 40 years. We do an excellent job in matching color the first time and maintain that match on succeeding orders, which is critical.”
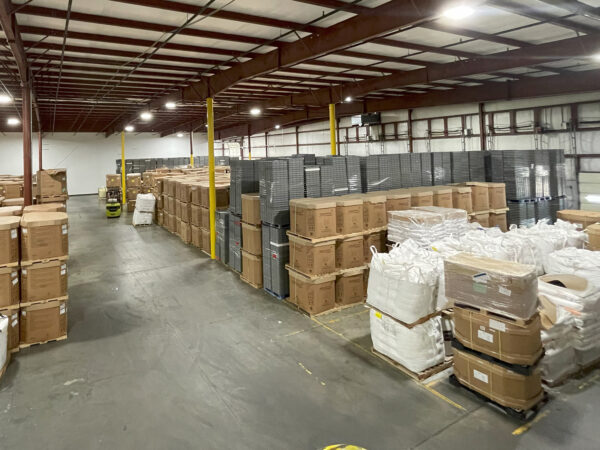
Almost doubling the Rochester plant to 60,000 square feet created ample warehousing space for storage and shipment of compounds.
The instruments PRL uses include Datacolor and X-Rite spectrophotometers. “Every custom-colored pellet we send out is compared to color chips and our spectrophotometers,” said Anderson. “We maintain chips for three years to assure color is right. We’ve had several companies transition from doing color at the press to having us do custom colors for them.”
“Customers come back [to us] because of consistency,” he added. “Even virgin resin that is clear varies; tint can change lot to lot.”
“The latest software technology helps our color matching team get to a 98 percent match on the first scan,” Anderson said. “The last 2 percent is an art, and always will be. It’s a technology that’s iterative, so the more color matches you do, the closer you get.” PRL operates two Arburg injection machines dedicated to molding color match chips.
PRL is one of two companies owned by Les Klein—the other is Polymer Engineered Products (PEP), of Rochester, an injection molding business. Klein started what would become Polymer Resources 50 years ago as a resin trading company. He began compounding in the late 1970s to gain greater control over quality. Klein became a partner in the injection molding business and took it over when the founder left to pursue another business. Anderson said PEP has around 20 injection machines ranging from 50 to 950 tons.
Anderson has been at PRL eight years. He spent almost 20 years at resin producer GE Plastics/SABIC in automotive sales, polycarbonate sales and in pricing work. “I was looking to do something a little smaller and this is it,” he said.
At PRL, “We pride ourselves as a service company that provides a great pellet.” Referring to the company’s investment in sustainable products and operations, he added, “This sustainable journey makes us better at everything.”