A New Way of Controlling the Parison in Extrusion Blow Molding
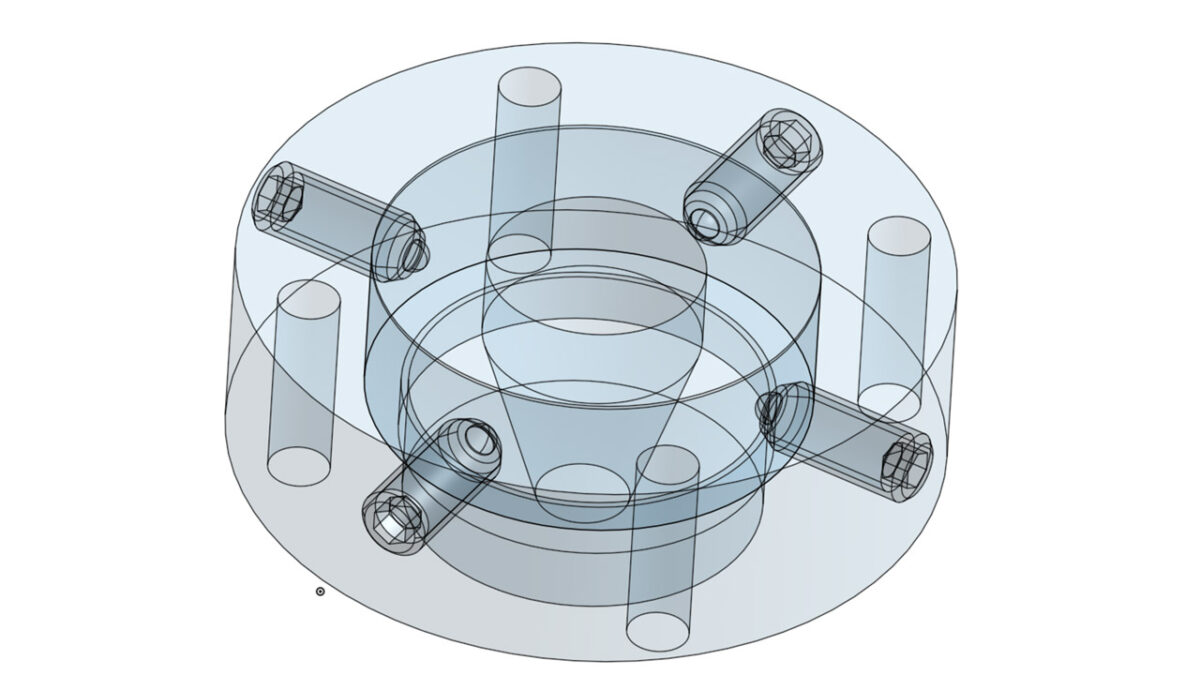
Ottmar Brandau’s new patent suggests using die rings with spring-loaded pistons
A newly issued patent aims to enhance control of the parison in extrusion blow molding, thereby minimizing production disruptions and improving the quality and consistency of hollow objects such as plastic bottles.
The EBM process includes extruding molten resin through an annular gap, formed between a die and a mandrel disposed inside the die, explains Ottmar Brandau, president of Markham, Ontario-based Pet All Manufacturing Inc. and the holder of the patent. The extruded resin forms a parison extending from the die. The configuration of the annular gap determines the diameter and thickness of the parison. To form the hollow object, the user places a mold around the parison and introduces air inside of it to inflate the parison against the mold.
The molten plastic is under high and varying pressure inside the die head. The pressure varies with the extrusion speed, melt temperature, die gap, and material composition. The melt flow index of the resin may be different from batch to batch and the regrind percentage is often adjusted during the day, as the scrap percentage changes.
The impact of pressure and temperature changes

Ottmar Brandau
Additionally, the pressure changes when the die gap varies during the cycle, a normal occurrence for most bottle programs. Temperature can also change when resin comes out too quickly from a day bin and the temperature inside differs significantly from the outside temperature or when the inside temperature changes between day and night, as most blow molding operations are not climate controlled.
These temperature and pressure changes can affect parison uniformity. A round bottle requires an even wall thickness in the parison that is running straight. When the parison curls to one side, the bottle wall further away from the parison will blow thinner. Many bottles have a minimum thickness requirement that can then be jeopardized, usually in the bottom corner. A parison with thickness variations above acceptable tolerances can delay production and cause costly manufacturing problems. When the manufacturer’s quality control (QC) department finds bottles outside the required specifications, for example, the entire batch of bottles made since the last QC check must be quarantined, which becomes a costly and time-consuming process.
Machine operators have relied on die holders that displace the die in a horizontal direction, with bolts, to change the shape of the annular gap, Brandau says. Older die holder rings have four or more bolts spaced evenly around the die ring. Modern systems use a three-bolt adjustment to allow the adjustment from the front, while the machine is running, by inserting long Allen keys through holes in the safety gate. However, three-bolt adjustments are more difficult to operate and take longer to master.
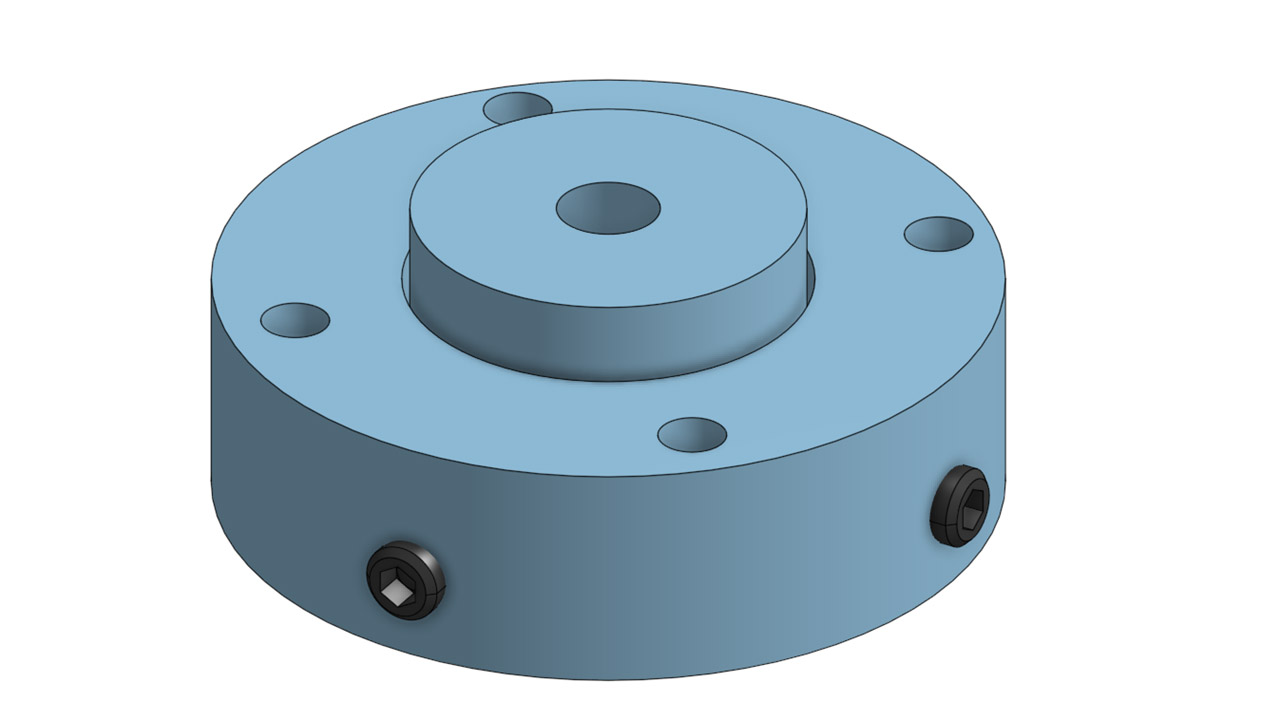
Fig. 2) Modified ring with plungers
Such adjustments are often performed multiple times a day and may require pausing production to perform the adjustments on some machines. To counter the curling parison, a machine operator would push the die toward the slow-moving side, essentially reducing the gap at the fast-moving side of the die. This could become necessary several times per production day, causing delays, possible quarantine procedures when a minimum wall thickness is out of tolerance, and costly regrind or sorting procedures. If faulty bottles are sent to a customer, an entire truckload may be returned, jeopardizing customer relationships.
Using spring-loaded fasteners
Brandau says his newly issued patent addresses this problem by suggesting die rings with spring-loaded pistons in three, four or more locations, placed around the die holder ring. The spring-loaded fasteners are arranged to apply pressure to respective positions on the outer surface of the die. This process still
permits movement of the die within a plane that is substantially orthogonal to a longitudinal axis of the mandrel in response to pressure variations of the molten resin, thereby altering the shape of the annular gap.
It has been shown that whether the uneven parison thickness is caused by changes in temperature or pressure, these pistons are able to correct the parison flow without operator intervention, for as long as the dies run the same bottle. There is only an initial adjustment that is necessary; the spring-loaded plungers do the rest.
Brandau tested three units in a production environment, with operators filling out a form every time they made an adjustment to the process. After the initial setup, the parts ran for 32 days without manual intervention, whereas a typical die holder ring will be adjusted three to five times per day.
Brandau has been in blow molding since 1978 and is the author of five books describing both stretch and extrusion blow molding. He is president of the consulting firm Apex Container Tech Inc. as well as PET All Manufacturing, a machine distributor of blow machines of various types. Those interested in obtaining more information on how to get a trial die ring should contact him at [email protected].